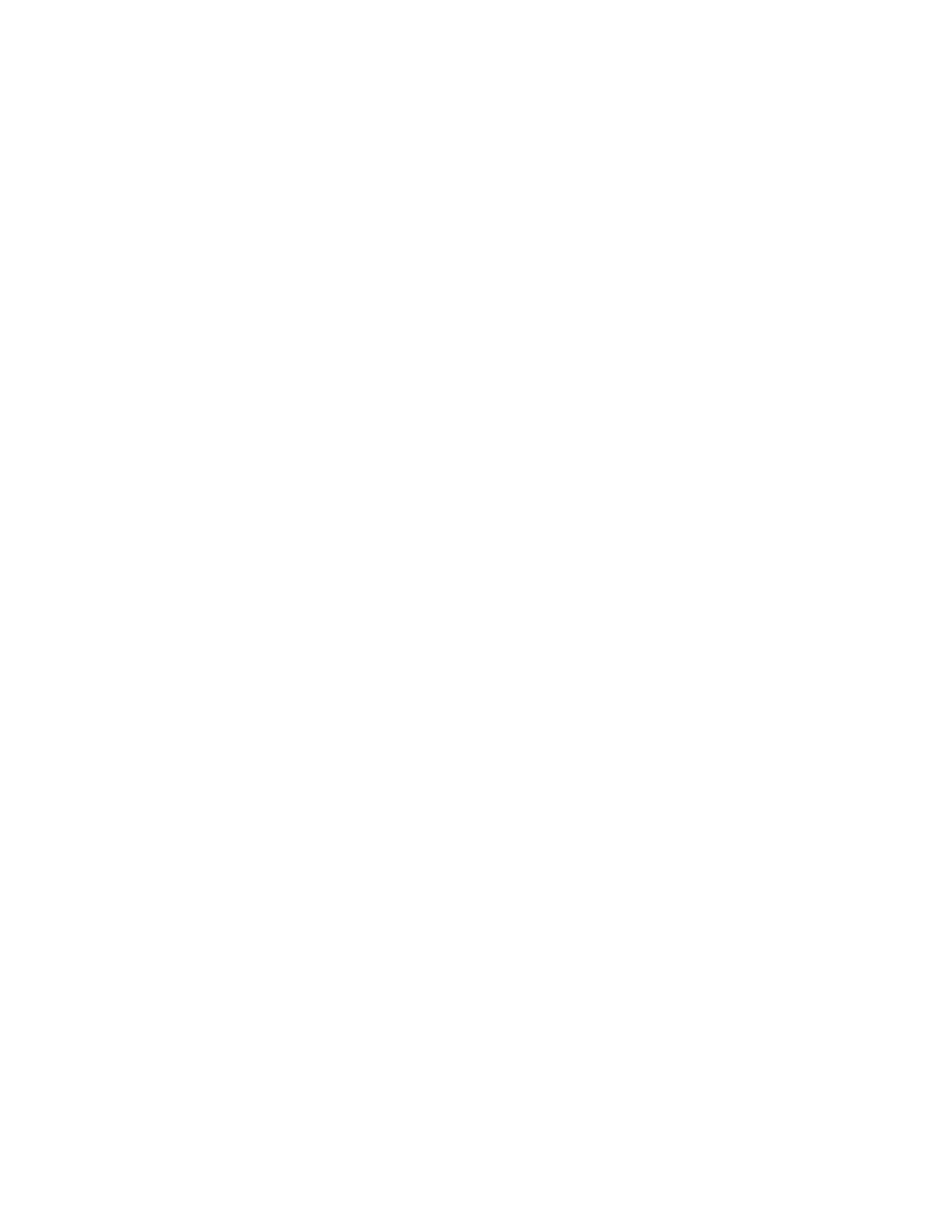
19
CONFIGURACIÓN DE PARÁMETROS - MAN(ual)
El modo MANUAL se usa cuando:
• No hay un transductor disponiblee
• Se desea programar un par de torsión RESIDUAL (estático)
• Las juntas de la aplicación tienen grados de rigidez muy
variados
• La aplicación tiene un par alto predominante
• Se va a instalar una herramienta de transmisión directa con
el software de herramientas de impulsión estándar.
NOTA: lo más recomendable es instalar el software correcto
para la herramienta que se va a usar.
Siga estos pasos para programar el Pset mediante el método
MANUAL:
1. Seleccione el Pset deseado
2. Fije el conteo (Set Count) (número de pernos por lote
(Batch) o ciclo (Cycle))
3. Calibre el transductor (CAL TRANSDUCER)
NOTA: si se usa un transductor, aparecerá la lectura observada
en la pantalla MANUAL TEACH (ENSEÑAR MANUALMENTE)
al lado del par de torsión (TQ). Si no hay un transductor
conectado, pulse la opción "NO" para avanzar a la pantalla -
MANUAL TEACH -.
En el modo MANUAL TEACH, el valor SIG tiene un valor
predeterminado de 075 y puede ser ajustado hacia ARRIBA o
hacia ABAJO. De esta forma se ajusta el índice de presión/flujo
del aire para que el usuario pueda ajustar el nivel de par. No
obstante, un valor entre 110 y 115 sería muy probablemente el
valor máximo a no ser que el suministro de aire sobrepase los
90 psi y 50 scfm.
Hay cinco pasos que se deben seguir para programar una
aplicación en el modo MANUAL.
— PROGRAMACIÓN MANUAL —
Ponga en marcha la herramienta con un perno de prueba y
mantenga apretado el gatillo hasta que el casquillo deje de
girar.
NOTA: ESTE PASO PUEDE TARDAR UNOS 5 SEGUNDOS.
En el modo MANUAL, el operador controla el apagado de la
herramienta. Después de detener manualmente la
herramienta, mida el par de torsión aplicado con un método
estándar aprobado por su empresa. Si el par medido no es
correcto, ajuste el valor SIG con las teclas de flecha y
vuelva a intentarlo hasta conseguir el par deseado.
Una vez que el nivel de par sea correcto, oprima la tecla Enter
(intro). Introduzca el valor medido en la pantalla SET PARAM-
ETER TgTq (PROGRAMAR PARÁMETRO PAR FINAL).
LEARN FREERUN - RUN TOOL - (APRENDER CICLO LIBRE
- OPERAR HERRAMIENTA)
Haga funcionar la herramienta en el aire hasta que el
controlador la detenga.
LEARN PREVAIL - RUN TOOL - (APRENDER
PREDOMINANTE - OPERAR HERRAMIENTA)
Ponga en marcha la herramienta en la aplicación para que el
controlador "aprenda" las características de la junta durante el
apriete de los pernos.
LEARN REHIT - RUN TOOL - (APRENDER REPETIDO -
OPERAR HERRAMIENTA)
Vuelva a pasar la herramienta sobre el perno que acaba de
apretar en el paso LEARN TGTQ (APRENDER PAR FINAL).
Mantenga apretado el gatillo hasta que el sistema apague la
herramienta.
SET JOINT TYPE- (PROGRAMAR TIPO DE JUNTA)
Esta selección se hace de acuerdo a la rigidez de la junta. Si va
a usar un perno de rosca uniforme y las juntas son duras (por
ejemplo, de metal contra metal, sin arandelas ni empaques o si
se trata de una aplicación de bujías), seleccione el parámetro
HARD (DURO).
La mayoría de las aplicaciones con herramientas de impulsión
usan el parámetro MEDIUM (MEDIO) a no ser que las juntas
sean demasiado blandas. En dicho caso, se puede seleccionar
SOFT (BLANDO) o escoger la opción MANUAL. En la opción
MANUAL, el operador detendrá la herramienta cuando el
casquillo/perno haya dejado de girar. Seleccione una de estas
cuatro opciones con las teclas de flecha hacia ARRIBA/ABAJO.
NOTA: seleccione SIEMPRE el parámetro HARD (DURO)
para las herramientas de transmisión directa. Esto
garantizará el mejor apagado posible y la mejor condición
ergonómica.
• JOINT TYPE: HARD (TIPO DE JUNTA: DURO)
Este es el parámetro predeterminado. Si se obtiene un par bajo
cuando se usa este parámetro, ensaye el parámetro MEDIUM
(MEDIO) o SOFT (BLANDO) antes de aumentar el valor SIG.
En el parámetro "HARD" la herramienta se detendrá
automáticamente.
• JOINT TYPE: MEDIUM (TIPO DE JUNTA: MEDIO)
El parámetro MEDIUM (MEDIO) es usualmente el más común
para herramientas de impulsión y para aprieta tuercas
neumáticos de percusión, a no ser que la junta sea demasiado
blanda o tenga un paso de apriete muy largo. En este
parámetro, la herramienta se detendrá automáticamente.
• JOINT TYPE: SOFT (TIPO DE JUNTA: BLANDO)
Use el parámetro "SOFT" (BLANDO) si la junta es demasiado
blanda como para que la herramienta alcance su par completo
en el parámetro MEDIUM (MEDIO). Este parámetro detendrá
automáticamente la herramienta.
• JOINT TYPE: MANUAL (TIPO DE JUNTA: MANUAL)
En este parámetro (con el transductor todavía en la
herramienta si se está usando uno), ponga en marcha la
herramienta sobre la aplicación.
En la modalidad MANUAL LEARN (APRENDER MANUAL), el
operador debe detener la herramienta manualmente tan
pronto como el casquillo/perno deja de girar. De esta forma
se establece el tiempo de funcionamiento del ciclo.
CONSULTE LOS DIAGRAMAS CON LA SECUENCIA DE
PROGRAMACIÓN AL FINAL DE ESTE MANUAL SI NECESITA
AYUDA DURANTE LA PROGRAMACIÓN
— PROGRAMACIÓN CON EL CÓDIGO DE
TRANSMISIÓN DIRECTO (10041) —
La programación del controlador con el código eprom 10041 es
similar al modo de programación MANUAL del código para
herramientas de impulsión (10039). Siga el diagrama que
aparece al final de este manual si necesita ayuda. La diferencia
principal es determinar la señal de flujo apropiada cuando
aparece la indicación correspondiente durante la secuencia de
programación del Pset.
Durante el paso "CHECK FLOW" (COMPROBAR FLUJO) de la
programación, la pantalla indicará al usuario que haga
funcionar la herramienta a una velocidad libre (RUN
FREESPEED). Simplemente ponga en marcha la herramienta a
cualquier velocidad al tiempo que ajusta el tornillo de flujo
(ubicado a través del agujero de acceso en la cubierta poste-
rior) para obtener una lectura adecuada (GOOD).
VI. ERROR PROOFING "OK / NOK" (CORRECCIÓN
DE ERRORES "SIN PROBLEMAS / PROBLEMA")
La corrección de errores es una de las funciones más
importantes del controlador TC50A. Una vez que se ha
preparado una aplicación, TC50A controla el par de torsión