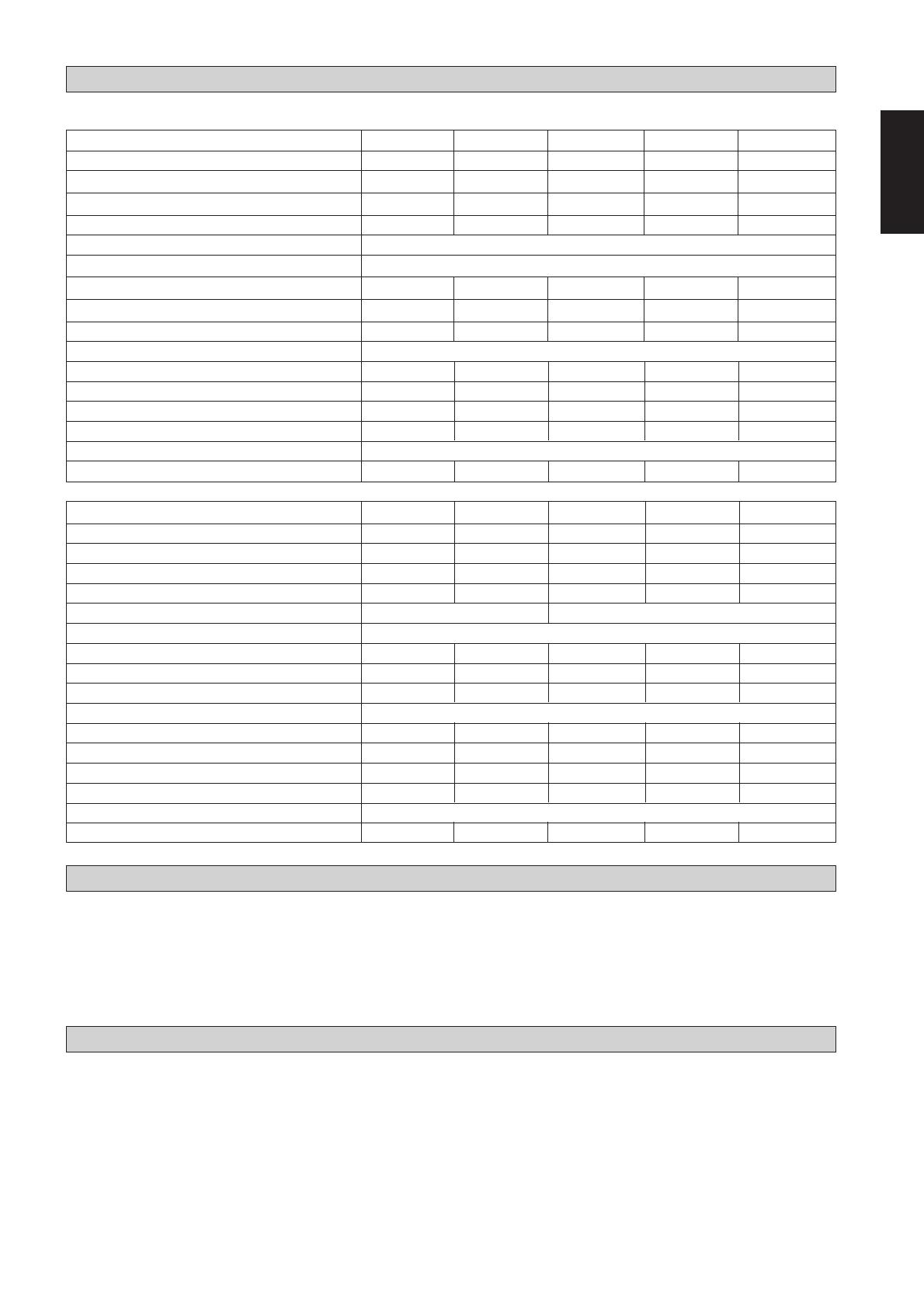
1-2
English
PHYSICAL DATA
R410A - Heat Pump
Model 5WSS07AR 5WSS10AR 5WSS15AR 5WSS16AR 5WSS20AR
Nominal Cooling Capacity kW 2.37 2.93 3.58 4.63 6.01
Nominal Heating Capacity kW 2.58 3.08 3.75 4.63 6.74
Unit Weight kg 32.9 34.9 35.5 39.7 49.1
Refrigerant Charge R410A kg 0.600 0.600 0.700 0.725 0.975
Compressor Rotary Compressor
Refrigerant Circuit
Liquid valve connection inches 1/4 1/4 1/4 1/4 1/4
Gas valve connection inches 3/8 3/8 1/2 1/2 1/2
Service port connection (UNF-20) inches 1/2 1/2 1/2 1/2 1/2
Refrigerant - Water Heat Exchanger Tube In Tube
Water inlet (male) inches 1/2 1/2 1/2 1/2 1/2
Water outlet (male) inches 1/2 1/2 1/2 1/2 1/2
Water pressure drop kPa 5.36 5.88 8.12 10.35 14.54
Water flow rate m
3
/h 0.45 0.51 0.75 0.95 1.25
Drain Pipe Connection
Steel Pipe inches 3/4 3/4 3/4 3/4 3/4
Model 5WSS25AR 5WSS30AR 5WSS40AR 5WSS50AR 5WSS60AR
Nominal Cooling Capacity kW 7.62 2.37 2.93 3.58 4.63
Nominal Heating Capacity kW 7.80 2.58 3.08 3.75 4.63
Unit Weight kg 50.0 64.1 95.7 119.6 123.4
Refrigerant Charge R410A kg 1.000 1.200 1.475 1.950 2.300
Compressor Rotary Compressor Scroll Compressor
Refrigerant Circuit
Liquid valve connection inches 1/4 3/8 3/8 3/8 3/8
Gas valve connection inches 5/8 5/8 5/8 5/8 3/4
Service port connection (UNF-20) inches 1/2 1/2 1/2 1/2 1/2
Refrigerant - Water Heat Exchanger Tube In Tube
Water inlet (BSP)MALE inches 1/2 3/4 3/4 3/4 3/4
Water outlet (BSP)MALE inches 1/2 3/4 3/4 3/4 3/4
Water pressure drop kPa 19.03 30.59 9.49 9.59 18.84
Water flow rate m
3
/h 1.4 1.8 2.1 2.55 3.17
Drain Pipe Connection
Steel Pipe inches 3/4 3/4 3/4 3/4 3/4
WATER PIPING AND FITTING
• Install a 40 – 60 mesh strainer to ensure water quality is good.
• Water pipe materials recommended are black steel pipe and copper pipe.
• All piping connections must be properly and firmly connected. Do not over-tighten the connections.
• Users are recommended to install the pipes as shown in Figure 5 & 6.
• The piping need to be cleaned and flushed prior to operation.
• Air vents must be installed at the highest position while a drainage system at the lowest position of the water circuit.
REFRIGERANT PIPING
• Do not use contaminated, dented or used copper tubing.
• Do not use copper tubes with less than 0.8 mm thickness.
• Use a flare tool specially for R410A.
• Do not use mineral oil on flare part.
• Use proper torque wrench to tight the flare nuts. If the torque strength is weak, gas leakage may occur. If it is too tight, the
flare nut may crack and it may be non-removable.
• Use a vacuum pump with a back flow preventing adapter to prevent the vacuum pump oil mix with R410A which will
create sludge and damage the equipment.
• Vacuum unit thoroughly to -76cmHg.
• Insulate the piping to prevent capacity losses and water condensation.