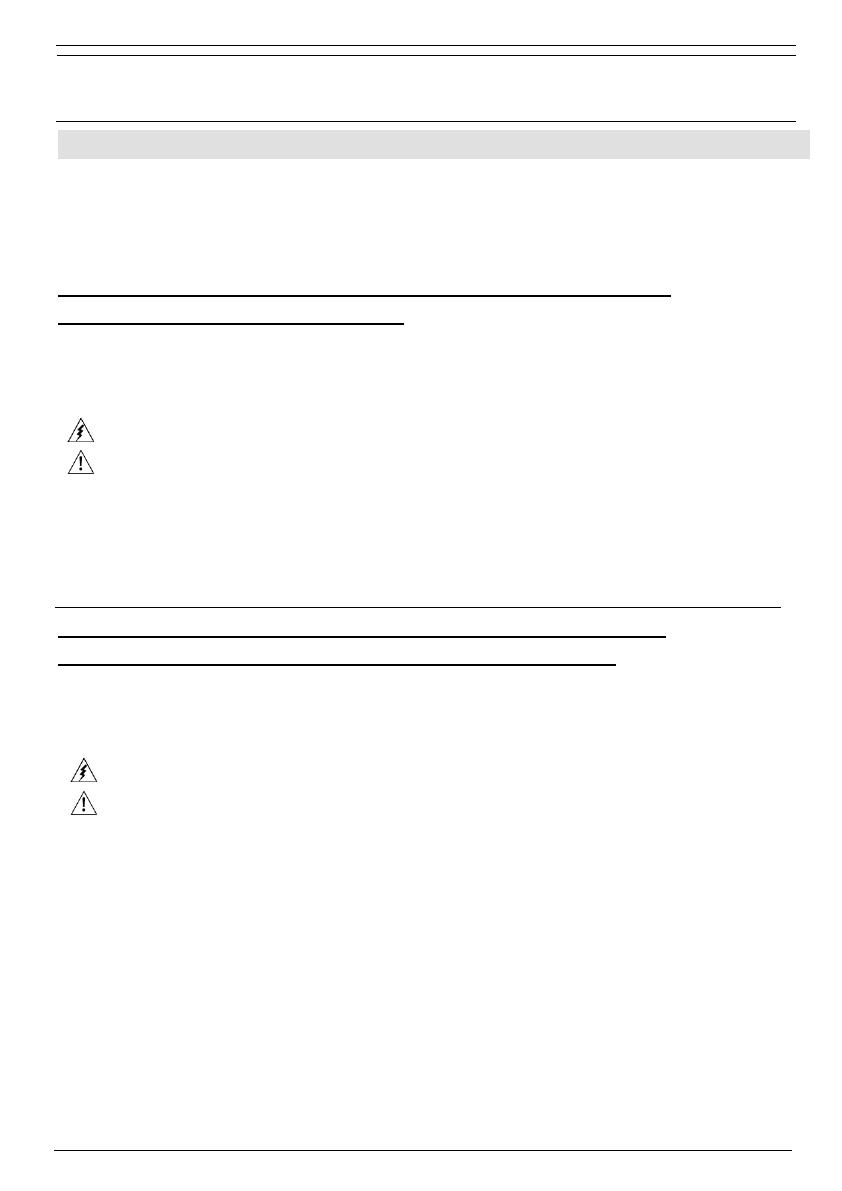
Communication Modules Installation Guide
▪ Installing modules also requires you to remove and replace PCB boards already installed
in the controller.
▪ Make certain that the pins fit correctly into their matching receptacle.
The following section is relevant to Unitronics’ products that are listed with the UL.
The following models: V100-17-CAN, V100-17-ET2, V100-17-RS4, V100-17-RS4X are UL listed for
Hazardous Locations.
The following models: V100-17-CAN, V100-17-ET2, V100-17-PB1, V100-17-RS4, V100-17-RS4X are
UL listed for Ordinary Location.
UL Ratings, Programmable Controllers for Use in Hazardous Locations,
Class I, Division 2, Groups A, B, C and D
These Release Notes relate to all Unitronics products that bear the UL symbols used to mark products
that have been approved for use in hazardous locations, Class I, Division 2, Groups A, B, C and D.
▪ This equipment is suitable for use in Class I, Division 2, Groups A, B, C and D, or Non-
hazardous locations only.
▪ Input and output wiring must be in accordance with Class I, Division 2 wiring methods and
in accordance with the authority having jurisdiction.
▪ WARNING—Explosion Hazard—substitution of components may impair suitability for
Class I, Division 2.
▪ WARNING – EXPLOSION HAZARD – Do not connect or disconnect equipment unless
power has been switched off or the area is known to be non-hazardous.
▪ WARNING – Exposure to some chemicals may degrade the sealing properties of material
used in Relays.
▪ This equipment must be installed using wiring methods as required for Class I, Division 2
as per the NEC and/or CEC.
Certification UL des automates programmables, pour une utilisation en
environnement à risques, Class I, Division 2, Groups A, B, C et D.
Cette note fait référence à tous les produits Unitronics portant le symbole UL - produits qui ont été
certifiés pour une utilisation dans des endroits dangereux, Classe I, Division 2, Groupes A, B, C et D.
▪ Cet équipement est adapté pour une utilisation en Classe I, Division 2, Groupes A, B, C et
D, ou dans Non-dangereux endroits seulement.
▪ Le câblage des entrées/sorties doit être en accord avec les méthodes
de câblage selon la Classe I, Division 2 et en accord avec l’autorité compétente.
▪ AVERTISSEMENT: Risque d’Explosion – Le remplacement de certains composants rend
caduque la certification du produit selon la Classe I, Division 2.
▪ AVERTISSEMENT - DANGER D'EXPLOSION - Ne connecter pas ou ne débranche pas
l'équipement sans avoir préalablement coupé l'alimentation électrique ou la zone est
reconnue pour être non dangereuse.
▪ AVERTISSEMENT - L'exposition à certains produits chimiques peut dégrader les propriétés
des matériaux utilisés pour l'étanchéité dans les relais.
▪ Cet équipement doit être installé utilisant des méthodes de câblage suivant la norme Class I,
Division 2 NEC et /ou CEC.