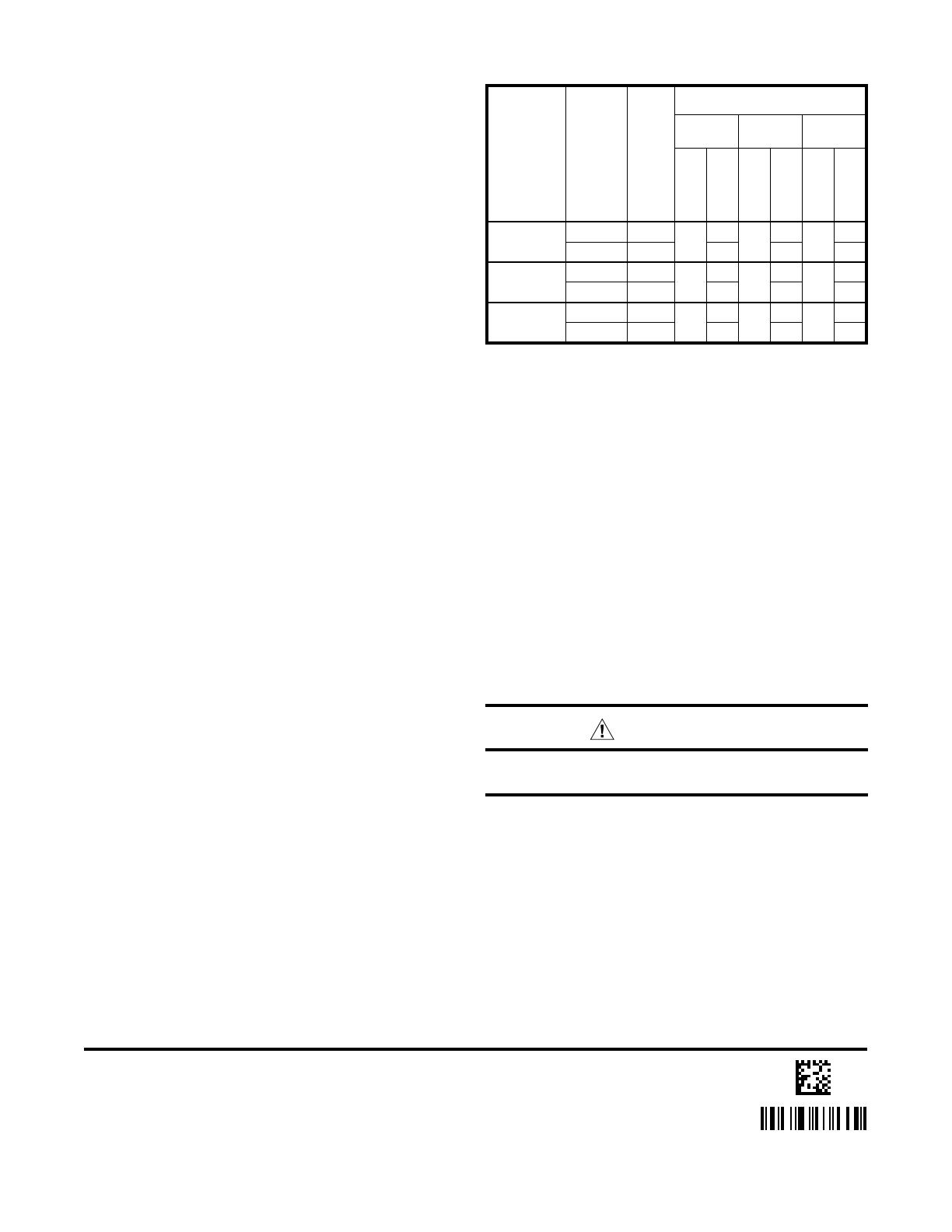
6. Check that the furnace ignites and operates properly. Refer
to the installation instructions provided with the unit for the
normal operating sequence.
7. After ignition, visually inspect the burner assembly to
ensure that the flame is drawn directly into the center of
the heat exchanger tube. In a properly adjusted burner
assembly, the flame color should be blue with some light
yellow streaks near the outer portions of the flame.
NOTE: The ignitor may not ignite the gas until all air is bled
from the gas line. If the ignition control locks out, turn the
thermostat to its lowest setting and wait one minute then
turn the thermostat above room temperature and the ignitor
will try again to ignite the main burners. This process may
have to be repeated several times before the burners will
ignite. After the burners are lit, check all gas connections
for leaks again with the soap and water solution.
Measuring the Manifold Pressure
The manifold pressure must be measured by installing a
pressure gauge (Manometer, Magnehelic Meter, etc.) to the
outlet end of the gas valve as follows:
1. Turn off all electrical power to the appliance.
2. Shut OFF the gas supply at the manual shutoff valve
located outside of the appliance.
3. Using a 3/16” Allen wrench, remove the manifold pressure
tap plug located on the outlet side of the gas valve. See
Figure 2.
4. Install an 1/8” NPT pipe thread fitting, that is compatible
with a Manometer or similar pressure gauge.
5. Connect the Manometer or pressure gauge to the manifold
pressure tap.
6. Set the room thermostat above room temperature to start
the furnace.
7. Allow the furnace to operate for 3 minutes and then check
the manifold pressure. Compare the measured value with
the value shown in Table 2. If the manifold pressure is not
set to the appropriate pressure, then it must be adjusted.
Adjusting the Manifold Pressure
NOTE: Adjustments must be made to both LOW & HIGH
fire settings when converting two-stage gas valves. Refer
to Table 2 for manifold pressures.
1. Remove the cap screw (Figure 2, page 3).
2. Using a screwdriver or Allen wrench (where appropriate),
slowly turn the adjustment screw till the appropriate manifold
pressure listed in Table 2 is achieved.
NOTE: Turning the screw clockwise increases the pressure,
turning the screw counter-clockwise decreases the
pressure. To prevent the screw from backing all the way
out from the valve, turn the screw slowly.
3. Replace and tighten the cap screw or the plastic cap over
the adjustment screw.
Removing the Manometer / Pressure Gauge
After the manifold pressure is properly adjusted, the
Manometer or pressure gauge must be removed from the
gas valve.
1. Turn the thermostat to its lowest setting.
2. Turn OFF the main gas supply to the unit at the manual
shut-off valve, which is located outside of the unit.
3. Turn OFF all of the electrical power supplies to the unit.
4. Remove the pressure gauge adapter from the gas valve
and replace it with the 1/8” NPT manifold pressure plug
that had been removed earlier. NOTE: Make sure the plug
is tight and not cross-threaded.
5. Turn ON the electrical power to the unit.
6. Turn ON the main gas supply to the unit at the manual
shut-off valve.
COMPLETING THE CONVERSION
WARNING:
Do not alter or remove the original rating plate
from the furnace.
1. Attach the following labels:
• Theconversionwarninglabel(P/N703935)shouldbe
afxedtotheoutsideoftheunitdoor.
• Theconversioninformationlabel(P/N703942)should
beafxedon the inside of thecontrolarea or the
louveredaccesspanel.
• Verifytheyellowlabelfromthespringconversionkit
isafxedtothegasvalve.
NOTE: Each label should be prominently visible after
installation.
2. Reinstall the appliance door.
3. Run the appliance through 3 complete cycles to assure
proper operation.
7096360(NEW)
Table2.LiquidPropaneConversionChart
(2-StageModels)
MODEL
NUMBER
R8HE
PPG3HE
GAS
VALVE
SETTING
INPUT
ALTITUDE ABOVE SEA LEVEL
0 to
1,999 FT
2,000 to
2,999 FT
3,000 to
4,500 FT
ORIFICE
SIZE
MANIFOLD
PRESSURE
ORIFICE
SIZE
MANIFOLD
PRESSURE
ORIFICE
SIZE
MANIFOLD
PRESSURE
-X24K060X
-X30K060X
High 60,000
55
10.0
55
9.0
55
8.0
Low 39,000 4.2 3.8 3.6
-X36K080X
-X42K080X
High 80,000
55
10.0
55
9.0
55
8.0
Low 52,000 4.2 3.8 3.6
-X48K100X
-X60K100X
High 100,000
55
10.0
55
9.0
55
8.0
Low 65,000 4.2 3.8 3.6
Specifications & illustrations subject to change without notice or incurring obligations (07/15).
O’Fallon, MO, © Nortek Global HVAC LLC 2015. All Rights Reserved.