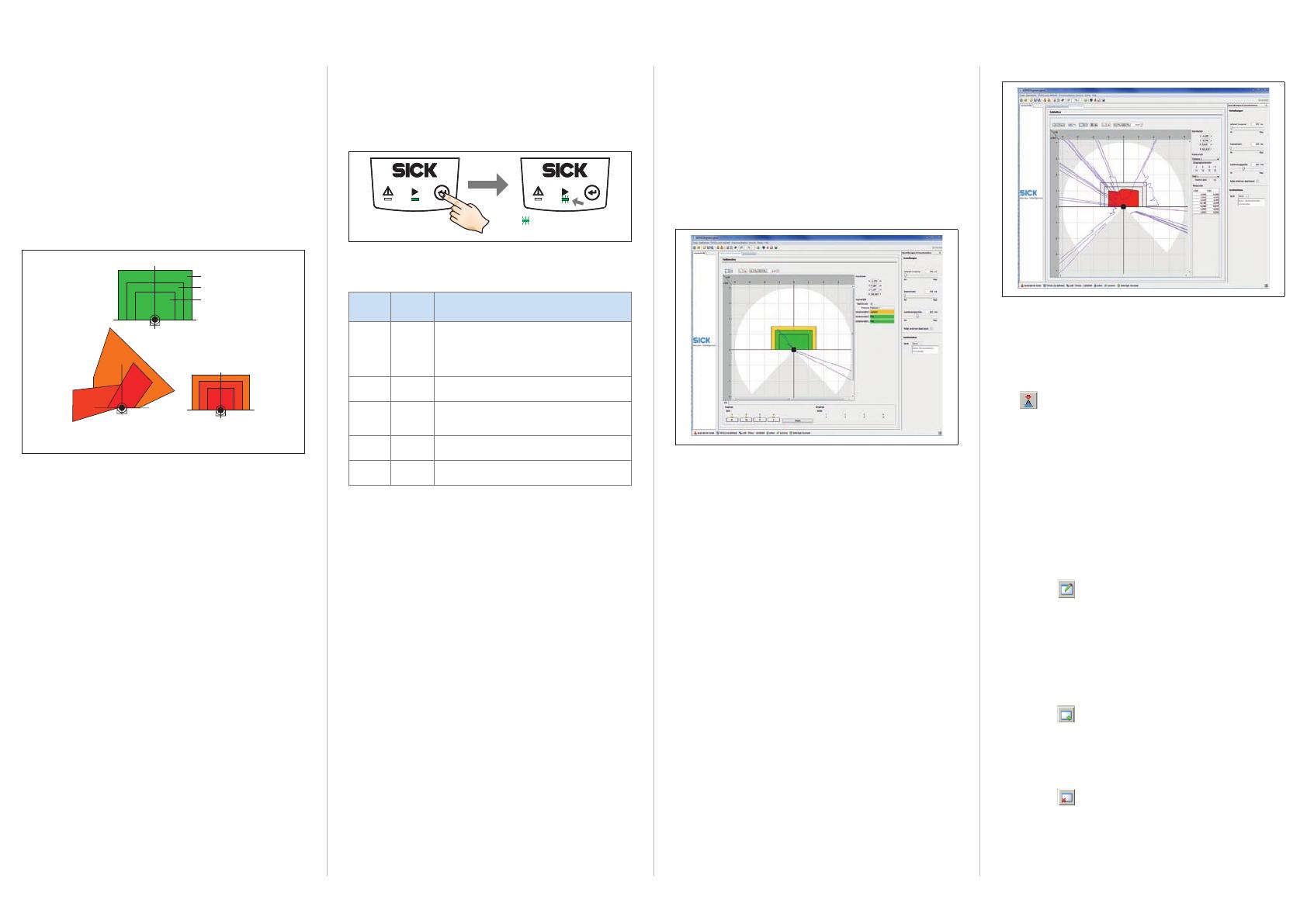
TIM35X/TIM36X | SICK 8016903/ZP97/2017-07-27 • Subject to change without notice • SICK AG • Waldkirch • Germany • www.sick.com2
a. Conguration without PC
Here, the TiM provides two options:
• Using one of 16 default eld sets, each with 3 predened
elds having the same eld shape, but different sizes
• Teach-in of the surrounding contour to automatically gener-
ate the outer eld with any shape, including more complex
shapes, and to deduce the two inner elds.
The eld sets are organized by groups into segmented eld
shapes. The shapes can be modied, with the default being a
rectangle. In the factory setting, the 3 origin-oriented elds of
a set are nested inside one another.
Segmented,
free shape type
Rectangle
Field 1
Field 2
Field 3
0°180°
Structure of the elds of a eld set and possible eld shapes
Dimensions of the respective eld 1 and its shape in the
factory settings, as well as the required wiring of the switching
inputs for eld set selection see “Field set factory settings
– switching inputs, page 4”.
Preparing for teach-in
In general, the function button and both LEDs on the device
are used for teach-in.
• Remove all objects that will not permanently be in the eld
of view in monitoring mode later on.
• Distance yourself sufciently from the TiM during the
advance warning phase of the teach-in, so that you are not
detected as part of the eld contour.
Teaching-in the eld contour
The TiM uses eld set 1 (segmented, initial shape: rectangle)
to adjust the eld shape and size to the surrounding contour
that was detected. The switching inputs may not be supplied
with current during this process.
The TiM forms the outer eld 3 from the surrounding contour
with a negative offset of 100 mm, and deduces the limits
of the two inner elds from this, so that eld 2 = eld 1 plus
25% and eld 3 = eld 1 plus 52%.
• The eld shape to be formed can be dened by pacing out
the limits during the teach-in phase. Do not wear black
clothing during this process!
• The TiM stores the shortest value measured during the
teach-in phase as a eld limit for each angle.
• Note: A parameter upload is required in order to display
the newly taught-in eld contour in SOPAS.
> Start the eld contour teach-in.
3 seconds
= flashes slowly
The behavior of the two LEDs indicates the progress of the
eld contour teach-in:
LED a
(red)
LED b
(green)
Status
–
Field contour teach-in – Start
LED ashes slowly (0.5 Hz)
Field contour teach-in – Advance warning
phase
LED ashes increasingly rapidly within 15 s
O O
Field contour teach-in – Teach-in phase
60 seconds
–
Field contour teach-in – Completion of
advance warning phase
LED ashes increasingly rapidly within 15 s
–
O
Automatic return to monitoring mode
All elds free
O O
Monitoring mode
In the event of eld infringement
O = illuminated, = ashing
The TiM stores the new eld set 1 permanently.
b. Conguration with PC
The SOPAS conguration software is used by default to adjust
the 3 elds of a eld set and other TiM parameters to the ap-
plication and to perform diagnostics in the event of an error.
If the eld shape of the eld set 1 has been taught in without
a PC using the function button, SOPAS is generally used to
continue the conguration.
This includes setting the eld shapes/sizes and any other
non-teachable eld sets based on the default setting, the
response time of the elds, the blanking size, and the holding
time of the assigned switching outputs OUT 1 ... OUT 3.
The blanking size is the smallest size from which an object
can be detected in a eld by the TiM and lead to a eld
infringement. All objects that are smaller than the minimum
size are blanked out. Like the response time and the holding
time, the blanking size applies to all eld sets and their elds.
Installing and launching the SOPAS conguration software
1. Download and install on the PC the software from the
website "www.sick.com/SOPAS_ET“. In this case, select
the "Complete" option as suggested by the install wizard.
Administrator rights may be required on the PC to install
the software.
2. Start the "Single Device" program option after completing
the installation.
Path: Start > Programs > SICK > SOPAS Engineering Tool >
SOPAS (Single Device).
SOPAS will automatically install the necessary USB driver
the rst time it detects a connected TiM. It may then be
necessary to restart the PC.
3. Establish a connection between SOPAS and TiM via the
wizard which opens automatically. Select the TiM from the
list of available devices.
SOPAS program window (single device)
Field monitor display window
• In the Field monitor window, SOPAS displays the eld
contour (scan line) currently seen by the device through
ambient reection in blue. If the 4 switching inputs are
not supplied with current, SOPAS also displays the three
evaluation elds (segmented rectangles) for the eld set
1 according to the TiM's default setting, or the eld shape
generated using the teach-in function along with its dimen-
sions, the status of the switching inputs/outputs, and the
position of the mouse pointer.
• SOPAS displays the elds as green if no eld infringement
is present. If objects of a certain size ( see “Default set-
tings TiM, page 3”) are located for a certain duration
in the part of the visual range that is covered by elds,
the TiM will recognize this as a eld infringement. SOPAS
displays this separately in yellow for the individual elds.
> Try changing the orientation of the TiM in the room and ob-
serve the effects this has on detection in the eld monitor.
Click the
reset button to cause SOPAS to reset the switch-
ing output counters.
Continuing the conguration process
Field editor display window
The user can change parameters in the right part of the pro-
gram window under
settinGs & deviCe status. SOPAS immedi-
ately transfers these changes to the TiM (default setting).
However, evaluation elds that have been changed in size and
shape must always be manually transferred to the TiM using
the
button. All changed parameters are only temporarily
stored in the device for the time being and are not stored in
the computer at all.
In order to optimize the dimensions of the monitoring elds:
1. Click the
evaluation Fields tab at the top of the program
window.
2. Under
Field seleCtion on the right side of the window,
select, for example, eld set 1.
3. Select the eld to be congured.
> You can optionally perform the following actions:
Shifting eld positions
1. Click the
button.
2. Click on the green marking rectangle of the desired eld
position in the outer eld.
The color of the marking rectangle changes to blue.
3. Re-click the rectangle and drag it to the desired position,
then release the pushbutton. SOPAS controls the available
positioning area during shifting.
Inserting additional eld positions
1. Click the
button.
2. Click on the desired position on the limits of the outer eld.
SOPAS inserts a new, green marking rectangle. This can
now also be shifted as already described.
Deleting eld positions
1. Click the
button.
2. Click on the green marking rectangle of the eld position to
be deleted in the outer eld.
The color of the marking rectangle changes to red.
3. Re-click the marking rectangle.