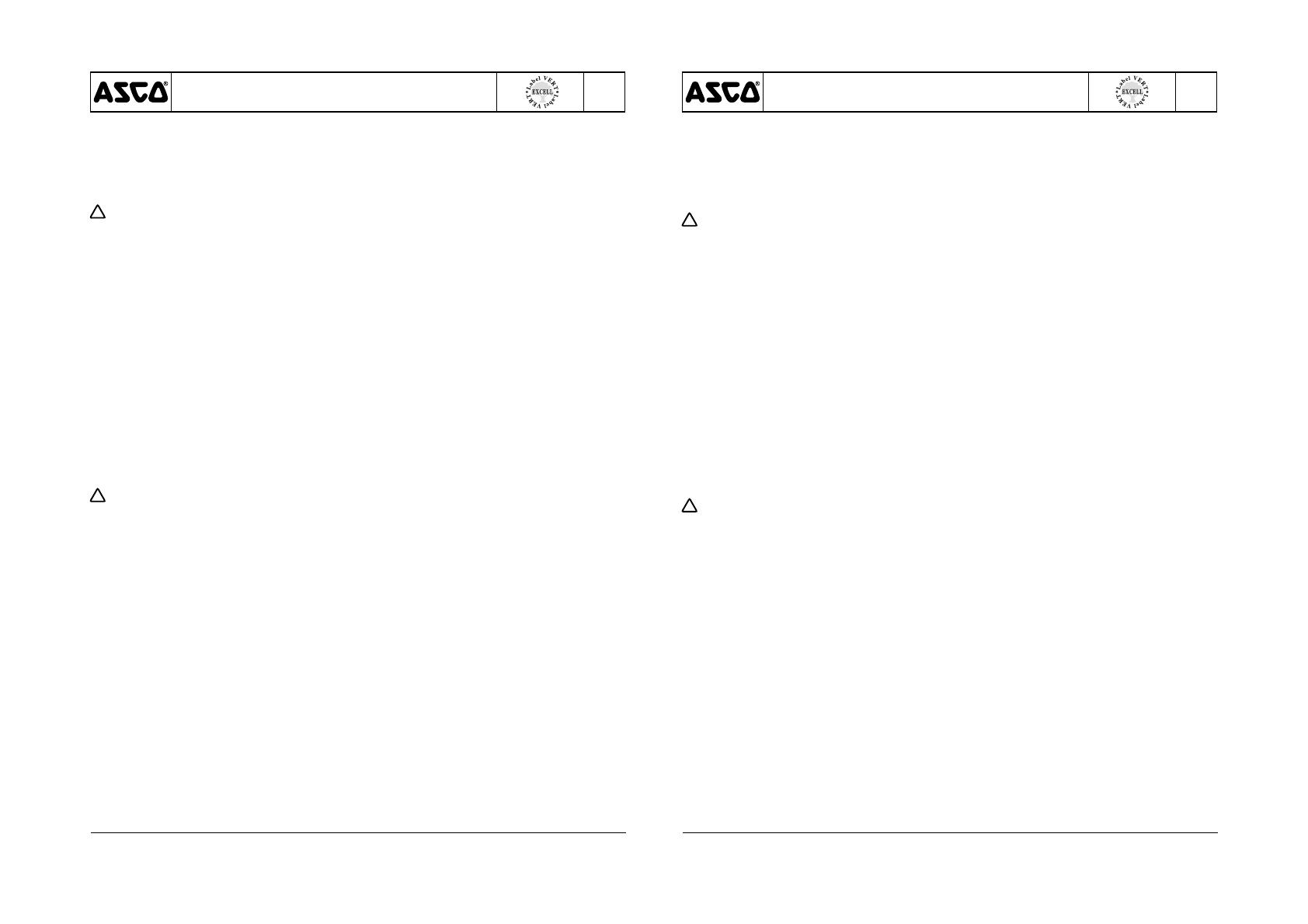
3834827
2
3834827
3
Installation and Maintenance Instructions
VALVES FOR CONTROL IN WINE TANKS
GB
This valve is designed for use in on/off function in a control loop. In
the system, it must be associated to safety equipment normally used
in this kind of process. Its failure can in no way be held responsible
for the effects of any deterioration or interruption of the process.
DESCRIPTION
Series 290 pressure-operated poppet valves, 2/2 NC, have been optimised
for high fl ow rates. The valves are equipped with a piston-type dia. 32
mm operator.The valve body is made of nickel-plated brass. The seals
are made of NBR.
FUNCTION
See the corresponding technical leafl et for min./max.pilot pressures,
the operating pressure differential and the fl uid temperature.
PUTTING INTO OPERATION
The valves are intended to be operated within the technical characteristics
specifi ed on the nameplate. Modifi cations to the equipment may only be
made after consulting the manufacturer or his representative. Before instal-
lation, depressurise the piping system and clean internally.
Read all information on the label: code, port, fl uid (type, pressure, tem-
perature), pilot fl uid, pilot pressure, serial number.
CAUTION: The valves are intended for use with special liquids (hot water
or glycol/water mixtures).
Max. fl uid temperature: +60°C
Dia 32 mm operator, piloting with fi ltered air.
Do not exceed the max. allowable pressure of the valve (8 bar). Instal-
lation and maintenance of the valve must be carried out by qualifi ed
personnel only.
Fitting position
The valves may be mounted in any position. The dia. 32 mm operator can be
rotated by 360° around its axis to enable easy access to the pilot orifi ce.
Boring of supply tubes
• Holes of max. 20 mm must be drilled into the tubes to receive the valves
taking the allowable inclination into account. Max. angle of inclination α
= 15° (fi g. 1)
• In case of a unit with 2 valves, the tube pitch of 120 mm/130 mm/240 mm
(other pitches available on request, min. pitch = 90 mm) and the max.
offset of the 2 bores of A = 12 mm for 20 mm diameter (fi g. 2) must be
observed.
• We recommend the use of a drilling jig to ensure proper hole spacing
for the valves (fi g. 3).
Make sure the holes on the tubes for the valves are not out of
round. The tubes must be drilled with an appropriate tool (cutter, hole
saw etc) and the holes must be deburred.
Use Total CERAN LT grease:
- To mount the connecting hose (no. 6), the plug and circlip (nos. 9
and 10) and a new operator (fi g 7).
Connection
• A centering piece (no. 4) is provided to position the valves on the tubes
drilled beforehand.
• The valves are fastened on the tubes with a mounting kit (no. 1) (for
tube dia. 40 to 44 mm or 50 to 54 mm).An interface seal (no. 2) and a
fastening clamp (no. 3) adapted to the tube diameter (dia. 40 to 44 mm
or 50 to 54 mm) are included in each kit.
• The connection (feed or return line, cooling or heating loop) to the
exchanger (see diagram fi g. 8) is made on the valve body over the
threaded G ¾ port [the unused port must be sealed with a plug (no.
11) (not supplied)].
• The connection of the pilot air supply is made with a right-angle instant
hose fi tting 2,7 x 4 mm) (supplied mounted on the dia. 32 mm opera-
tor).
• Use Total CERAN LT grease for mounting.
Installation of a valve alone (fi gs. 4 and 6)
• This type of installation requires the optionally available kit of plug/circlip
(nos. 9 and 10).
• Put one of the labels (supplied with the valve) on the handle of the
manual isolation valve (red for heating loop, blue for cooling loop).
• Observe the recommended tightening torque to fasten the valve on
the tube with the interface seal (no. 2) and the fastening clamp (no. 3)
included in the mounting kit (no. 1) adapted to the respective tube
diameter. Pre-mount the screw (no. 15a) using the counter-nut. Mount
the valve and make sure to progressively tighten the two screws evenly
(nos. 15a and 15b) and then tighten the counter-nut (no. 16) against
the valve body.
Assembly of a 2-valve module (fi gs. 5 and 6)
• The two valves can be supplied assembled at delivery. But it is also
possible to assemble 2 separate valves to form a feed or return module.
For this purpose, a fastening kit which contains 2 spacers (no. 5), a con-
necting hose (no. 6) and the necessary screws (no. 7) is available.
• The standard tube pitch is 120 mm (other pitches are available on
request, min. pitch = 90 mm).
• Place the labels (no. 12) (supplied with the valves) on the handles of the
manual isolation valves (red for heating loop, blue for cooling loop).
• The unused port G ¾ must be sealed with a plug (no. 11) (not supplied).
Use sealing tape on the thread of the plug before putting it into place
and tightening it to the recommended torque.
• Fasten the 2 assembled valves on the tube with the interface seal (no.
2) and the fastening clamp (no. 3) included in the mounting kit (no. 1)
adapted to the respective tube diameter. Pre-mount the screw (no.
15a) and tighten the counter-nut (no. 16) to fi x the clamp against the
valve body. Mount the valve and make sure to progressively tighten the
screw (no. 15b). Observe the recommended tightening torque.
Mounting of a drain for the isolation valve (no. 8)
• Remove the plug mounted on the valve and insert the drain. Use seal-
ing tape on the thread of the drain when mounting and tighten it to the
recommended torque.
MAINTENANCE
Prolonged downtimes
For systems exposed to outdoor climatic conditions (frost), a drain (no. 8)
is available as an option to allow draining the ball valve.
Cleaning
Maintenance of the valves depends on the operating conditions. They
should be cleaned at regular intervals. The intervals between two clean-
ing operations may vary according to the nature of the fl uid, the working
conditions and the environment in which it is operated. During servicing,
the components must be checked for excessive wear. The components
must be cleaned when a slowing down of the cycle is noticed even though
the pilot pressure is correct or if any unusual noise or a leak is detected.
At worst, this may lead to a malfunction of the valve and it may not open
and close correctly any more.
Sound emission
The exact determination of the sound level can only be carried out by the
user having the valve installed in his system.
The emission of sound depends on the application, medium and type of
equipment used.
Preventive maintenance
● Operate the valve at least once prior to putting the system into operation
to check it opens and closes.
● The complete dia. 32 mm operator is available as a spare part (see
replacement procedure described below).
● The fastening clamps need to be replaced every 3 years.
● If problems arise during maintenance or in case of doubt, please contact
ASCO or one of its authorised representatives.
Troubleshooting
● Incorrect outlet pressure: Check the pressure on the supply side of the
valve; it must correspond to the values indicated on the nameplate.
Caution: observe the minimum pilot pressure values (see the corre-
sponding technical specifi cations).
● Leaks: Disassemble the valve body and clean the internal parts. Re-
place, if necessary, the dia. 32 mm operator.
Replacement of the dia. 32 mm operator (fi g. 7)
1. Close all manual valves on the temperature control loop.
2. Drain the loop on the exchanger side.
3. Pilot the operator (NC) to facilitate its disassembly.
4. Unscrew the operator unit using a 5 mm key.
5. Clean all accessible parts.
6. Cut the supply to the operator, disconnect the pilot feed pipe and
reconnect it to the new dia. 32 mm operator.
7. Pilot the operator once again to facilitate its reassembly.
8. Lightly grease the O-ring placed on the valve body, no 14 (grease
type Total CERAN LT).
9. Remount the operator unit using a 5 mm key to torque b.
10. Cut the supply to the operator.
11. Reopen all manual valves on the temperature control loop.
Reassemble all parts to the indicated tightening torques.
Make sure no foreign matter enters the valve and piping in the proc-
ess.
3834827 - A (R2 = A)
Availability, design and specifi cations are subject to change without notice. All rights reserved.
Instructions de mise en service et d'entretien
VANNES POUR LA REGULATION CUVES VINICOLE
FR
Cette vanne est destinée à être utilisée dans un circuit de régulation
pour un fonctionnement tout ou rien. A ce titre, elle doit être associée,
dans l'installation, aux équipements de sécurité habituellement uti-
lisés dans ce type de process. En aucun cas, sa défaillance ne peut
être rendu responsable des conséquences liées à la dégradation ou
à l'interruption du procédé.
DESCRIPTION
Les vannes télécommandées 2/2, NF , à clapet de la série 290 sont optimi-
sées pour obtenir un débit élevé. Ces vannes sont équipées d'une tête de
commande par piston Ø 32 mm. Les corps de vanne sont en laiton nickelé.
Les garnitures sont en NBR.
FONCTIONNEMENT
Se reporter à la notice correspondante pour obtenir les pressions
mini/maxi de pilotage, ainsi que pour la pression différentielle admissible
et la température du fl uide.
MISE EN SERVICE
Les vannes sont conçues pour les domaines de fonctionnement indiqués
sur la plaque signalétique. Aucune modifi cation ne peut être réalisée sur le
matériel sans l’accord préalable du fabricant ou de son représentant. Avant
de procéder au montage, dépressuriser les canalisations et effectuer un
nettoyage interne des dites canalisations.
Lire les informations portées sur l'étiquette : code, orifi ce, fl uide (type, pres-
sion, température), fl uide et pression de pilotage, et numéro de série.
ATTENTION : Ces vannes sont prévues pour fonctionner avec certains
fl uides (eau chaude ou eau glycolée).
Température maxi. du fl uide : +60°C
Tête de commande Ø 32 mm, pilotage avec de l’air fi ltré.
Ne pas dépasser la limite de pression maximale admissible de la vanne
(8 bar). La mise en service et l'entretien de la vanne doivent être réalisées
par du personnel compétent.
Installation
Ces vannes peuvent être montées dans n'importe quelle position. La tête
de commande Ø 32 mm, est orientable sur 360° autour de son axe afi n de
faciliter l'accès à l'orifi ce de pilotage.
Perçage des tubes d'alimentation
• Les tubes recevant les vannes devront être percés au diamètre de
20 mm maximum, en respectant les défaults d'inclinaison admissibles.
Angle α d'inclinaison maxi. = 15°(fi g. 1)
• Dans le cas d'un ensemble de 2 vannes, l'entraxe des tubes de
120 mm/130 mm/240 mm (ou autre sur demande, 90 mm mini.) devra
être respecté ainsi que les défauts d'alignement maximum des 2 trous
A = 12 mm si diamètre 20 mm (fi g. 2).
• Un gabarit de perçage est recommandé pour une bonne mise en place
des vannes (fi g. 3).
Les tubes recevant les vannes ne devront pas présenter de défaut
d'ovalisation. Le perçage des tubes sera réalisé avec un outil adapté
(fraise, scie cloche, ...)
et les orifi ces seront ébavurés.
Utiliser de la graisse type Total CERAN LT pour :
- Montage du tube de liaison (rep. 6), ensemble obturateur /circlip (rep.
9 et 10) et adaptation d'une nouvelle tête de commande (fi g. 7).
Raccordement
• Un pion de centrage (rep. 4) permet de positionner les vannes sur les
tubes préalablement percés.
• La fi xation sur les tubes est réalisée à l'aide d'un kit de fi xation (rep.1)
(pour tube Ø 40 à 44 ou 50 à 54 mm); Ces kits comprennent un joint
interface (rep. 2) et un collier de fi xation (rep.3) adaptés au Ø du tube
(Ø 40 à 44 ou 50 à 54 mm).
• Le raccordement (départ ou retour, circuit froid ou chaud) avec l'échan-
geur (voir schéma fi g. 8) s'effectue sur le corps de la vanne par un
orifi ce taraudé G 3/4 (Un bouchon non fourni rep. 11 obture l'orifi ce
non utilisé).
• Le raccordement de l'alimentation de pilotage est réalisé par un rac-
cord rapide coudé pour tube de 2,7 x 4 mm (livré monté sur la tête
Ø 32 mm).
• Utiliser de la graisse type Total CERAN LT pour adaptation.
Montage d'une vanne seule (fi g. 4, 6)
• Dans ce type de montage, il faut prévoir un deuxième ensemble obtu-
rateur/circlips (rep. 9 et 10) disponible en option.
• Mettre en place une des étiquettes (livrées avec la vanne) sur la poignée
de la vanne d'isolement manuelle (rouge, circuit chaud, ou bleue circuit
froid).
• Fixer la vanne sur le tube en utilisant le kit de fi xation (rep 1), compre-
nant un joint interface (rep.2) et un collier de serrage (rep. 3), adapté au
Ø du tube, en respectant le couple de serrage préconisé. Pré-monter
la vis (rep. 15a) à l'aide du contre-écrou. Monter la vanne en veillant à
serrer progressivement les 2 vis (rep. 15a et 15b) d'une façon équilibrée,
puis resserrer si nécessaire le contre écrou (rep. 16) contre le corps de
vanne.
Assemblage de 2 vannes (fi g. 5, 6)
• Les deux vannes peuvent être livrées assemblées. Néanmoins, il est
possible d'assembler deux vannes séparées afi n de former un bloc
aller ou un bloc retour. Il est proposé un kit d'assemblage comprenant
2 entretoises (rep.5), un tube de liaison (rep.6), la visserie nécessaire
(rep. 7).
• L'entraxe standard des tubes est de 120 mm (autre entraxe réalisable
sur demande, 90 mm mini.)
• Mettre en place les étiquettes (rep.12) (livrées avec les vannes) sur les
poignées des vannes d'isolement manuelles (rouge, circuit chaud, ou
bleue circuit froid)
• Un bouchon non fourni (rep.11) doit être mis en place sur l'orifi ce G 3/4
non utilisé. Utiliser un ruban d'étanchéité sur le fi letage du bouchon avant
sa mise en place, le serrer au couple préconisé.
• Fixer les 2 vannes assemblées sur les tubes en utilisant les kits de
fi xation (rep.1), comprenant un joint interface (rep.2) et un collier de
serrage (rep. 3), adaptés au Ø du tube. Pré-monter la vis (rep. 15a) et
serrer le contre-écrou (rep. 16) pour maintenir le collier contre le corps
de vanne. Monter la vanne et serrer progressivement la vis (rep. 15b).
Respecter le couple de serrage préconisé.
Adaptation d'un purgeur de vanne d'isolation (rep. 8)
• Retirer le bouchon monté sur la vanne et adapter le purgeur. Utiliser un
ruban d'étanchéité sur le fi letage lors du montage, le serrer au couple
préconisé
ENTRETIEN
Mise en arrêt prolongé
Pour les installations extérieures soumises aux conditions climatiques
(gel),il est proposé en option une purge (rep.8) permettant la vidange de
la vanne à boule.
Nettoyage
L’entretien des vannes varie avec leurs conditions d’utilisation. Procéder à
un nettoyage périodique des vannes. L'intervalle entre deux nettoyages
peut varier suivant la nature du fl uide, les conditions de fonctionnement
et le milieu ambiant. Lors de l’intervention, les composants doivent être
examinés pour détecter toute usure excessive. Un nettoyage est nécessaire
lorsqu'on observe un ralentissement de la cadence alors que la pression
de pilotage est correcte ou lorqu'un bruit anormal ou une fuite est constaté.
Au pire, un fonctionnement défectueux peut survenir et la vanne ne plus
s'ouvrir ou se fermer correctement.
Bruit de fonctionnement
L’utilisateur ne pourra déterminer avec précision le niveau sonore émis
qu'après avoir monté le composant sur l'installation.
Le bruit de fonctionnement varie selon l’utilisation, le fl uide et le type de
matériel employé.
Entretien préventif
● Faire fonctionner la vanne au moins une fois avant la mise en service
de l'installation pour vérifi er son ouverture et sa fermeture.
● La tête de commande complète Ø 32 mm est proposée en pièces de
rechange (voir procédure de remplacement ci-dessous).
● Remplacer les colliers de serrage tous les 3 ans.
● En cas de problème lors du montage/entretien ou en cas de doute,
contacter ASCO ou ses représentants offi ciels.
Conseils en dépannage :
● Pression de sortie incorrecte : Vérifi er la pression à l'entrée de la vanne,
elle doit correspondre aux valeurs admises sur l'étiquette d'identifi cation
ASCO.
Attention, respecter les valeurs minimales de pression de pilotage (se
reporter aux notices correspondantes).
● Fuites : Démonter le corps de vanne et nettoyer ses parties internes.
Changer si nécessaire la tête de commande Ø 32 mm.
Remplacement de la tête de commande Ø 32 mm (fi g. 7)
1. Fermer les vannes manuelles du circuit de thermorégulation.
2. Purger le circuit coté échangeur.
3. Piloter la tête de commande (NF) pour faciliter son démontage.
4. Dévisser l'ensemble tête de commande à l'aide d'une clé de 5 mm.
5. Nettoyer toutes les parties rendues accessibles.
6. Couper l'alimentation de la tête de commande, déconnecter le tuyau
d'alimentation du pilote et le connecter sur la nouvelle tête Ø 32 mm
à adapter.
7. Piloter la nouvelle tête de commande pour faciliter son remontage.
8. Graisser légèrement le joint torique placé sur le corps de vanne, rep. 14
(graisse type Total CERAN LT)
9. Remonter l'ensemble tête de commande à l'aide d'une clé de
5 mm, couple b.
10. Couper l'alimentation de la tête de commande.
11. Réouvrir les vannes manuelles du circuit de thermorégulation.
Remonter les pièces en respectant les couples de serrage indiqués.
Veillez à ne pas introduire de corps étrangers dans la vanne et tuyauterie
pendant cette intervention.