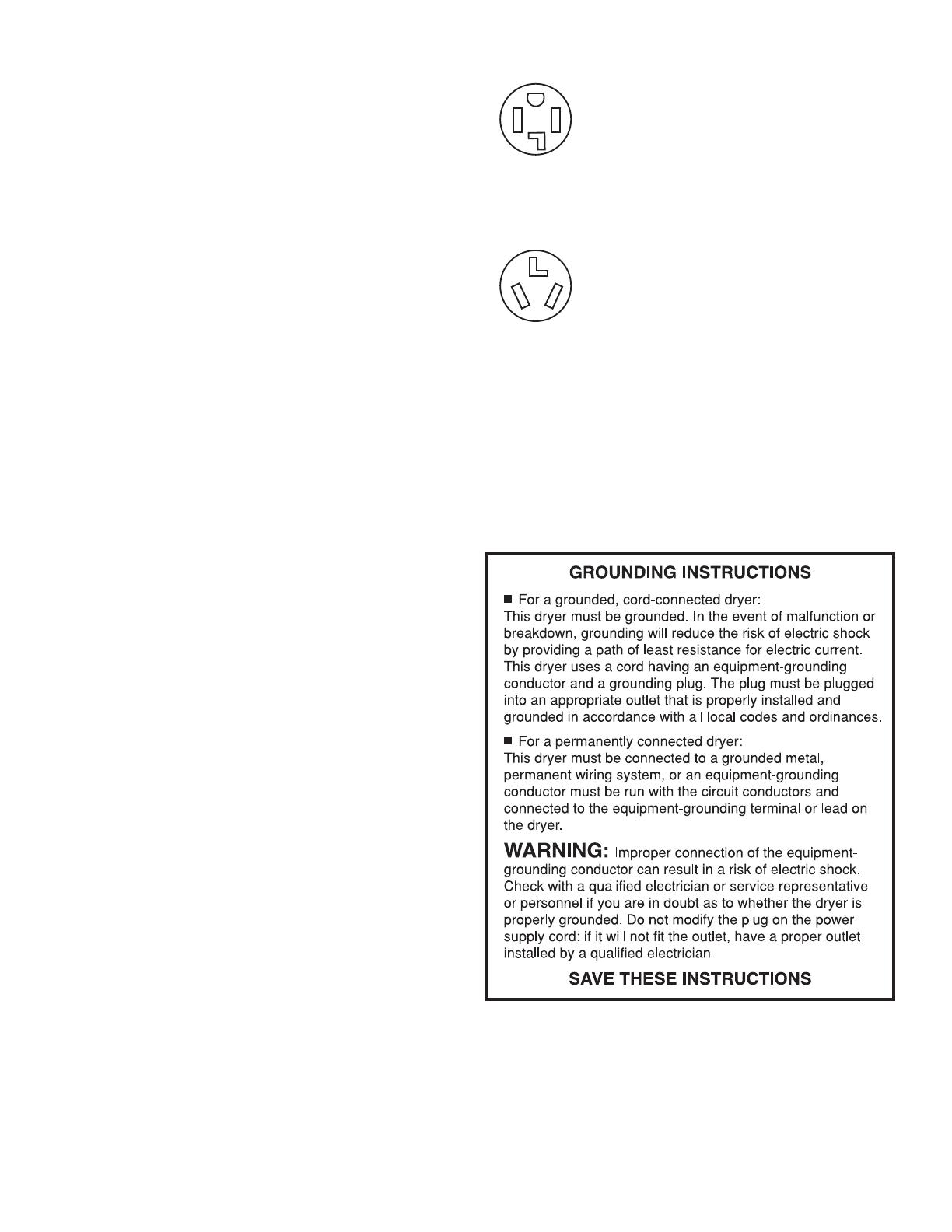
7
ELECTRICAL REQUIREMENTS –
U.S.A. ONLY
It is your responsibility:
■
To contact a qualied electrical installer.
■
To be sure that the electrical connection is adequate and in
conformance with the National Electrical Code, ANSI/NFPA 70
– latest edition and all local codes and ordinances.
The National Electrical Code requires a 4-wire power supply
connection for homes built after 1996, dryer circuits involved
in remodeling after 1996, and all mobile home installations.
A copy of the above code standards can be obtained from:
National Fire Protection Association, One Batterymarch Park,
Quincy, MA 02269.
■
To supply the required 3 or 4 wire, single-phase, 120/240 V,
60 Hz, AC-only electrical supply (or 3 or 4 wire, 120/208 V
electrical supply, if specied on the serial/rating plate) on a
separate 30 A circuit, fused on both sides of the line. Connect
to an individual branch circuit. Do not have a fuse in the
neutral or grounding circuit.
■
Do not use an extension cord.
■
If codes permit and a separate ground wire is used, it is
recommended that a qualied electrician determine that the
ground path is adequate.
Electrical Connection
To properly install your dryer, you must determine the type of
electrical connection you will be using and follow the instructions
provided for it here.
■
This dryer is manufactured ready to install with a 3-wire
electrical supply connection. The neutral ground conductor is
permanently connected to the neutral conductor (white wire)
within the dryer. If the dryer is installed with a 4-wire electrical
supply connection, the neutral ground conductor must be
removed from the external ground connector (green screw),
and secured under the neutral terminal (center or white wire)
of the terminal block. When the neutral ground conductor is
secured under the neutral terminal (center or white wire) of the
terminal block, the dryer cabinet is isolated from the neutral
conductor. The green ground wire of the 4-wire power cord
must be secured to the dryer cabinet with the green ground
screw.
■
If local codes do not permit the connection of a neutral ground
wire to the neutral wire, see “Optional External Ground for
3-Wire Connection” in the “Power Supply Cord Connection”
section.
■
A 4-wire power supply connection must be used when the
appliance is installed in a location where grounding through
the neutral conductor is prohibited. Grounding through the
neutral is prohibited for (1) new branch-circuit installations
after 1996, (2) mobile homes, (3) recreational vehicles, and (4)
areas where local codes prohibit grounding through the neutral
conductors.
If using a power supply cord:
Use a UL Listed power supply cord kit marked for use with
clothes dryers. The kit should contain:
■
A UL Listed 30 A power supply cord, rated 120/240 V
minimum. The cord should be type SRD or SRDT and be at
least 4 ft. (1.22 m) long. The wires that connect to the dryer
must end in ring terminals or spade terminals with upturned
ends.
■
A UL Listed strain relief.
Then choose a 3-wire power supply cord with
ring or spade terminals and UL listed strain
relief. The 3-wire power supply cord, at least
4 ft. (1.22 m) long, must have three 10-gauge
copper wires and match a 3-wire receptacle of
NEMA Type 10-30R.
4-wire receptacle
(14-30R)
3-wire receptacle
(10-30R)
If connecting by direct wire:
Power supply cable must match power supply (4-wire or 3-wire)
and be:
■
Flexible armored cable or nonmetallic sheathed copper cable
(with ground wire), covered with exible metallic conduit. All
current-carrying wires must be insulated.
■
10-gauge solid copper wire (do not use aluminum) at least
5 ft. (1.52 m) long.
If your outlet looks like this:
Then choose a 4-wire power supply cord with
ring or spade terminals and UL Listed strain
relief. The 4-wire power supply cord, at least
4 ft. (1.22 m) long, must have four 10-gauge
copper wires and match a 4-wire receptacle of
NEMA Type 14-30R. The ground wire (ground
conductor) may be either green or bare. The
neutral conductor must be identified by a white
cover.