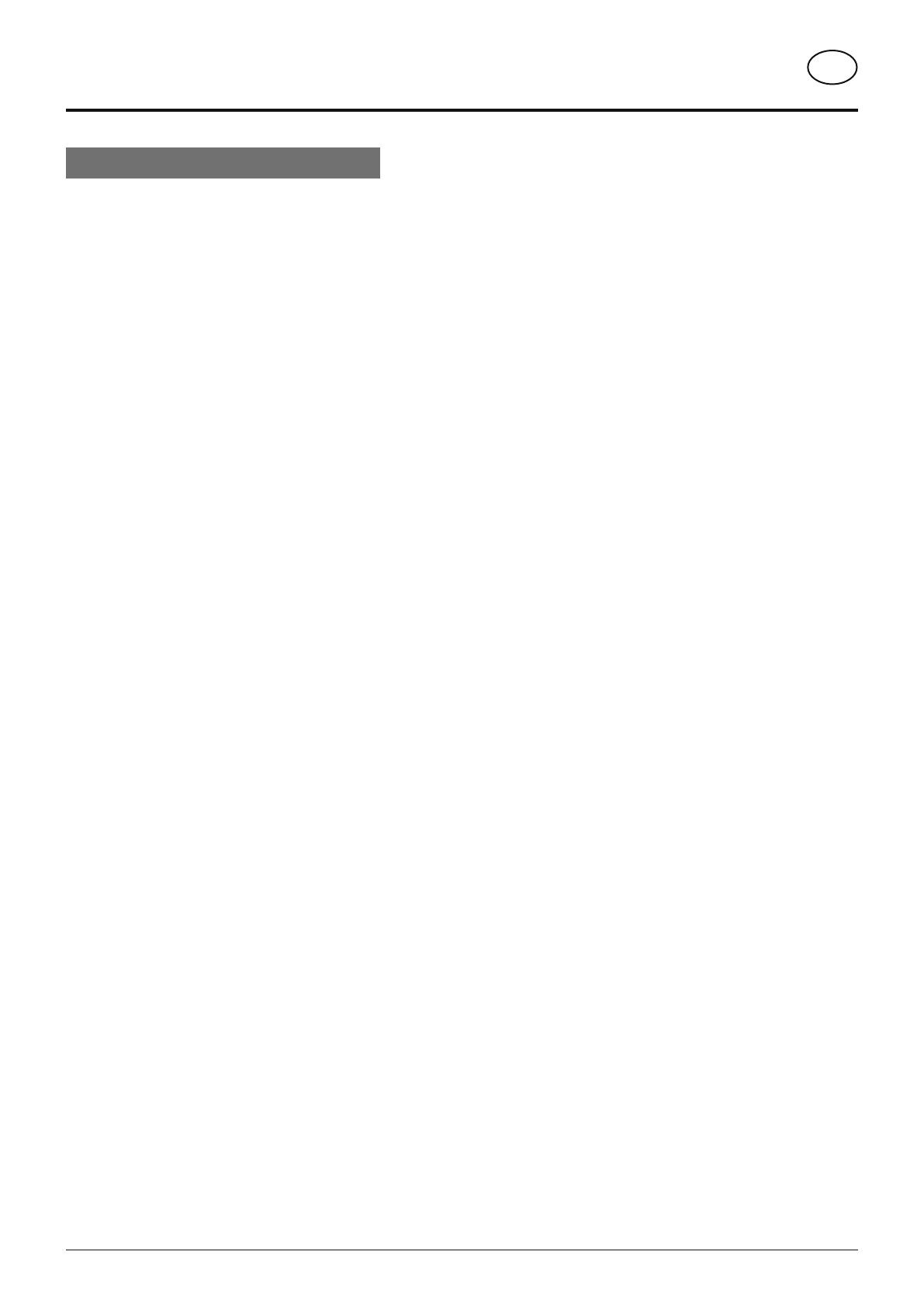
- 2 -
0700_GB-INHALT-KA_549
¼ÈÇ;ÇÍ
GB
ÍÚÛåÞèßÜèçíÞçíì
INTRODUCTION
1. Introduction .................................................................3
2. Product liability and .....................................................3
information obligation ......................................................3
3. Type label ....................................................................3
4. Guarantee ....................................................................3
5. Warning labels .............................................................4
6. Advices for working and driving safety .......................4
6.1 Driving off-the-road and on the clamp silo ................5
6.2. Driving on the road ...................................................5
TECHNICAL DATA
7. Technical data and equipment ....................................6
7.1 Technical data ...........................................................6
7.2 Special equipment .....................................................6
HITCHING EUROPROFI / FARO / PRIMO
8. Connection of the trailer (Europrofi / Faro / Primo) to
the tractor ........................................................................7
8.1 Coupling of the hydraulic hoses ................................7
8.2 Coupling of the braking system ................................7
8.3 Electric System ..........................................................7
HITCHING JUMBO / TORRO
8. Connection of the trailer (JUMBO / TORRO to the
tractor ..............................................................................8
8.1 Coupling of the hydraulic hoses ................................8
8.2 Coupling of the braking system ................................8
8.3 Electric System ..........................................................8
START-UP
9. Start-up .......................................................................9
9.1 Checks before each start ..........................................9
9.2 Checks before departure ...........................................9
10. Operation .................................................................10
10.1 Hydraulic suspension with automatic height control
10
10.2 Trailing axle ............................................................10
10.3 Load adaptation valve of the brake system ..........10
11. Parking of the trailer ................................................10
MAINTENANCE
12. Maintenance ............................................................11
12.1 Tires .......................................................................12
12.2 Hydraulic system ...................................................13
12.3. Brake system ........................................................14
Maintenance EUROPROFI / FARO / PRIMO .................15
12.4 Axles and brakes ...................................................15
12.5 Supporting structure and connections ..................15
12.6 Lubrication plan .....................................................15
Maintenance JUMBO / TORRO ....................................16
12.4 Axles and brakes ...................................................16
12.5 Supporting structure and connections ..................16
12.6 Lubrication plan .....................................................16
TECHNIQUE
13. Technique ................................................................17
13.1 Pendulum equalizer ...............................................17
13.2 Hydraulic suspension with automatic height control
(option) ..........................................................................17
13.3 Trailing axle ............................................................18
REPAIR WORK
14. Maintenance and repair work ..................................19
14.1 Change of tires ......................................................19
14.2 Height control ........................................................23
14.3 Brake lever EUROPROFI / FARO / PRIMO ............25
14.3 Brake lever JUMBO / TORRO ...............................26
15. Cleaning ..................................................................26
SWITCH DIAGRAM
16. Switch diagram........................................................27
HYDRAULIC DIAGRAM
17. Hydraulic diagram ...................................................28