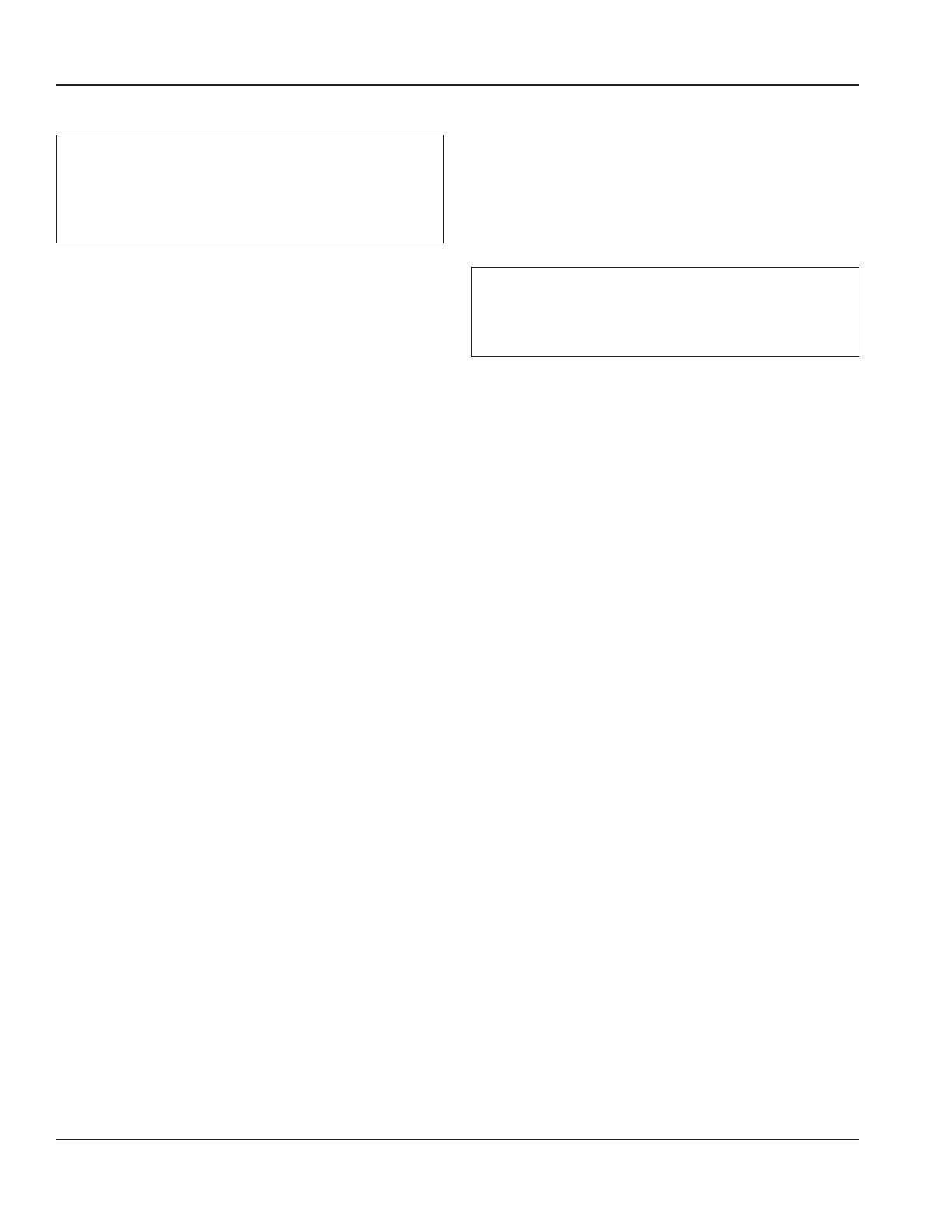
14 Part Number 11020000487 Rev A (2/16)
Installation Section 2
SPACING REQUIREMENTS
n
Warning
To avoid instability the installation area must be capable
of supporting the combined weight of the equipment
and product. Additionally the equipment must be level
side to side and front to back.
The oven must have 6inches (152mm) of clearance from
combustible surfaces. In case other equipment is located
on the right side of oven, a minimum clearance of 24inches
(609mm) is required from that equipment.
FOR ALL OVENS: A 24‑inch (609mm) clearance at the rear of
the oven must be obtainable for service access.
FOR PERMANENTLY INSTALLED OVENS: A permanently
installed (unmovable) oven requires a minimum of 13feet
clearance on the right hand side to allow for conveyor
removal, cleaning, and servicing.
NOTE: Do not install this (these) oven(s) in any area with an
ambient temperature in excess of 95°F/35°C. Doing so will
cause damage to the unit.
VENTILATION REQUIREMENTS
A VENT IS REQUIRED: Local codes prevail. These are the
“authority having jurisdiction” as stated by the NATIONAL
FIRE PROTECTION ASSOCIATION, INC. in NFPA96 latest
edition. In addition, to be in compliance with the NFPA 54
Section10.3.5.2, this unit must be installed with a
ventilation hood interlock that prevents the unit from
operating when the ventilation hood is off. For further
ventilation information, see below.
Ventilation Guidelines
A ventilation hood is required to remove heat and cooking
odors. For gas ovens, a ventilation hood is also required to
remove the products of combustion. The hood and HVAC
installation must meet local codes to gain approval by
the authority having jurisdiction. Requirements may vary
throughout the country depending on the location by city,
county, and state. Obtain information from the authority
having jurisdiction to determine the requirements for your
installation. (NOTE: This oven is considered as “Light Duty
for Baking” when evaluated for code vent requirements.)
Obtain information and review copies of codes or
documents that will be used to inspect and approve your
installation. Your ventilation hood supplier and HVAC
contractor should be contacted to provide guidance. A
properly engineered and installed ventilation hood and
HVAC system will expedite approval and reduce oven
maintenance costs. Proper ventilation is the oven owner’s
responsibility.
The ventilation hood must operate in harmony with
the building HVAC system. It typically requires between
1600 and 2800CFM exhaust or more with 70% make‑
up air. (The “Efficiency” of various hood designs makes it
necessary to specify such a wide range of ventilator CFM.)
Make up air must be supplied by either a hood design or
the HVAC system. This will vary with hoods from various
manufacturers.
,
Caution
Prevent airflow through the cooking tunnel. Air must
NOT be directed onto the oven front or at side of cooking
area or rear of oven.
Ventilation System
NOTE: These ovens are considered “Light Duty for Baking”
when evaluated for code vent requirements.
This information is shown as a guideline for ventilation.
1. Dimensions shown are for ovens without extension
shelves. The outside end of the conveyor frame must be
a minimum of 8inches inside the canopy as shown.
2. The capture velocity across the lower edge of the
canopy is to be 50FPM at sides and front.
3. Use filters at rear exhaust area of hood, as shown.
4. At start‑up, the CO level must be checked around the
oven space under the canopy.
5. This level must be <10ppm.
6. The ovens are to be centered in the canopy space left‑
to‑right and front‑to‑back if possible.
7. A 6‑inch space at rear of oven is recommended for
utilities.
8. Recommend 70% make‑up air provided outside of the
canopy through perf metal diffusers directed straight
down — not at the oven; located at front, sides or both.
9. Room air diffusers must not be directed onto the oven
and should be positioned a minimum of 3feet from the
perimeter of the hood to keep them from affecting the
oven.