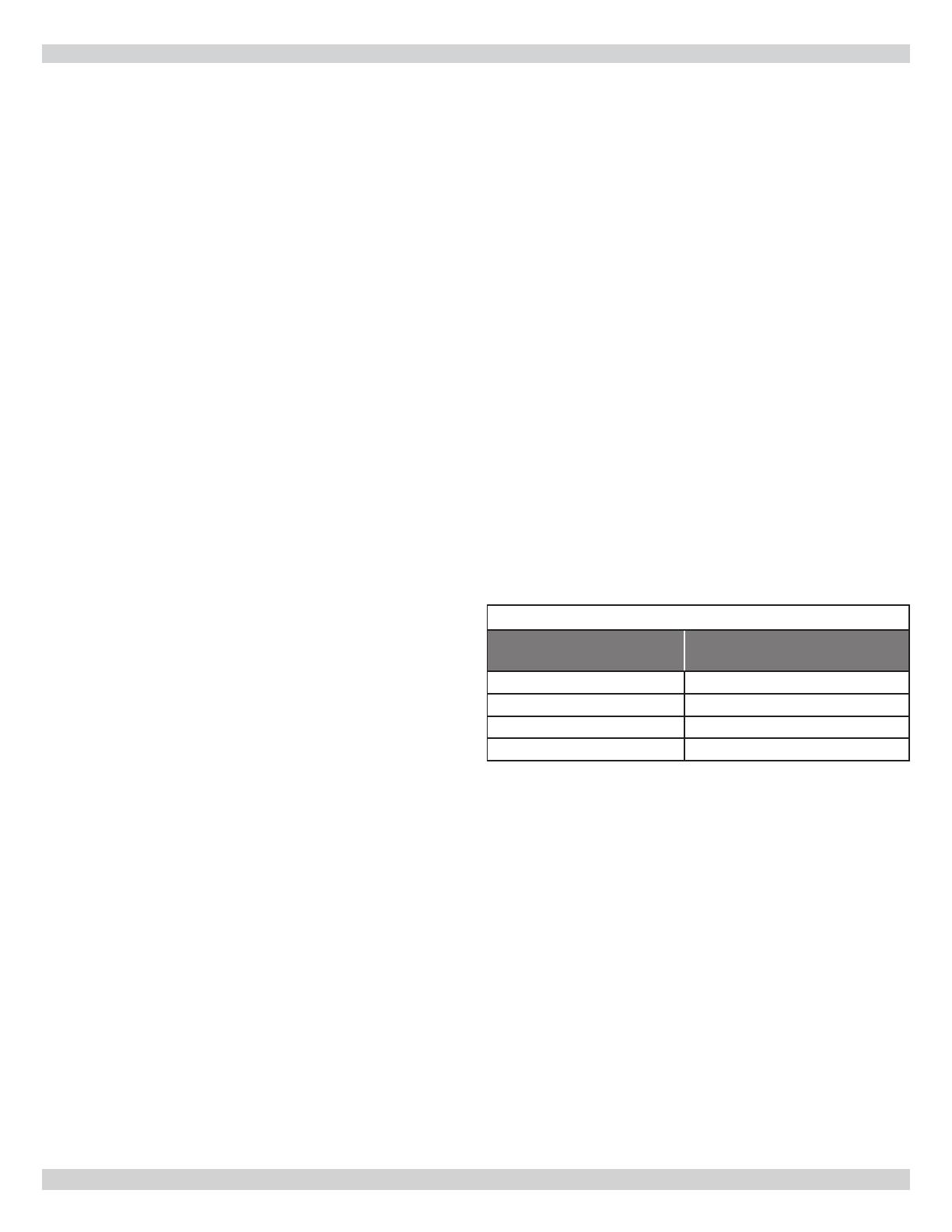
10
conTroL informATion Continued
Degrees Fahrenheit
90°F - 180°F
(Factory Setting: 180°F)
+/- 4°F - +/- 20°F
(Factory Setting: 12°F)
200°F
Internal temperature potentiometer
on control.
Control switch "On"
position and safety end switches are closed, "Safety
Switch" LED is lit. Once in operating mode, control
uses well-mounted (RTD) sensor to continuously
monitor water temperature.
Thermostat calls for heat ("TT" LED is lit), control will
energize circulator ("Circ" LED is lit) for 30 seconds
to establish ow. Control will then measure water
temperature and differential setting, perform check
for "open" or "shorted" RTD sensor, verify all safety
end switches are "closed," check for stuck or welded
element relay contacts. Next, control will energize
only one element ("Element" LED is lit) and monitor
water temperature for 60 seconds. Control will
energize additional elements at 30 second intervals
to bring system up to set point temperature in 5
minutes.
Once system reaches set point temperature and
there is still call for heat, control will modulate
number of elements on and off in order to maintain
set point temperature. Required number of elements
energized is determined by heating demand, which
is difference between actual boiler water temperature
and set point temperature.
After call for heat has been satised, elements will
de-energize ("Element" LEDs turn off) by control and
. After 3 minutes control
will de-energize circulator ("Circ" LED turns off).
If during start-up or during operation safety end
switch opens its respective contact, control de-
energizes all elements, continues to energize
circulator, and ashes visible fault code ("Fault" LED
ashes) along with audible fault code. (See fault
codes (below)) Control has built-in reset function.
Water "Set point"
temperature adjustment dial on control should be set
at designed boiler water temperature.
Control mounted using
1/2" tall plastic standoffs. Indicator LEDs are visible
through clear polycarbonate viewing window on front
cover.
Control and other
components located within control panel are sensitive
to water and other liquids. Protect components on
panel from contact with liquids.
1 Safety switch fault
2 Stuck/welded element relay contact
3 RTD short
4 RTD open
Verify RTD sensor is functioning properly, follow steps
below.
Remove both RTD leads from terminal block control
1.
board.
Use multimeter to take ohm reading across RTD leads.
2.
Properly functioning RTD will produce reading of ap-
proximately 1000 ohms at 70°F. Faulty RTD will read
either 0 or 1 on multimeter.
Replace RTD if necessary.
3.
5-7/8"(W) x 9-3/8" (L) x 1-5/8" (H)
90°F - 180°F (adjustable)
200°F (xed)
120V ac
120V ac, 5A max. (circulator
terminal)
120V ac pump output is switched by
onboard circulator relay. Load current limited must not
exceed 5A.