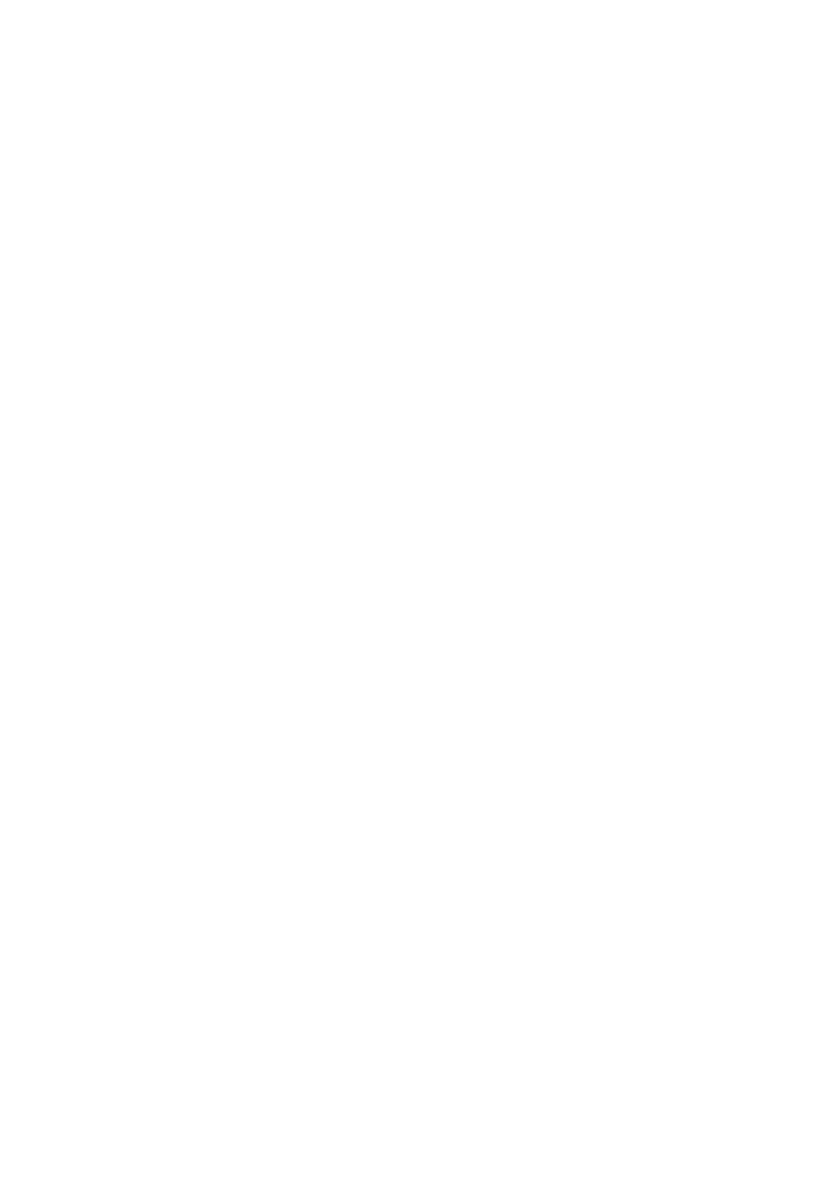
8
Recirculation with point-of-distribution thermostatic mixing valves
For domestic recirculating water systems, , that include a single ASSE 1017 point-
of-distribution thermostatic mixing valve, such as the Caleffi MixCal 521 series, the
piping installation in the application drawing on page 7 is recommended.
In any recirculating hot water distribution system there will be times when the circulator is
operating, but no hot water is being drawn at the fixtures. Under this condition, heat continually
dissipates from the piping forming the recirculation loop. If the loop is relatively short, and well
insulated, the rate of heat loss should be very small. If the loop is long, and uninsulated, the
rate of heat loss could be substantially greater.
To maintain the recirculating water at the desired delivery temperature the heat lost from the
loop must be replaced. This requires some water flow between the loop and the hot water
source. Ideally, this flow is adjusted so that the rate of heat transfer from the hot water source
to the loop exactly balances the rate of heat loss from the loop’s piping.
The figure (below) shows a “bypass valve” (1), and “return valve” (2), which regulate how
much warm water from the return side of the recirculating loop flows back to the storage tank.
When there is no demand for hot water at the fixtures, the flow of return water to the tank
will equal the rate of hot water flow from the tank to the inlet port of the mixing valve. Ideally,
this flow should be adjusted so that the rate of heat transfer from the tank to the recirculating
loop exactly balances the rate of heat loss from the recirculating loop. This allows the water
temperature leaving themixing valve to remain stable.
The bypass valve (1) and possibly the return valve (2) must be adjusted when there is no
domestic water draw on the recirculating loop (when all the fixtures are off). Begin with the
bypass valve (1) fully closed, and the return valve (2) fully open. Turn on the recirculating
circulator and let it run for several minutes. The supply water temperature leaving the mixing
valve will likely be lower than the setting of the valve, since there is no return flow to the tank
thus, no hot water to the hot port of the mixing valve.
Slowly open the bypass valve (1) and monitor the temperature leaving the mixing valve. It will
likely begin rising as some water returns to the tank, and an equal flow of hot water moves
from the tank to the hot port of the mixing valve. When the temperature leaving the mixing valve
remains stable, and is at or very close to the temperature set on the mixing valve, the bypass
valve is correctly set.
The return valve (2) can remain fully open unless a situation occurs where the bypass valve (1)
is fully open, but the temperature leaving the mixing valve is still too low. If this occurs, partially
close the return valve (2) to add flow resistance. This forces more flow through the bypass valve
(1). Repeat the previously described procedure of slowly opening the bypass valve (1) until the
water temperature leaving the mixing valve is stable.