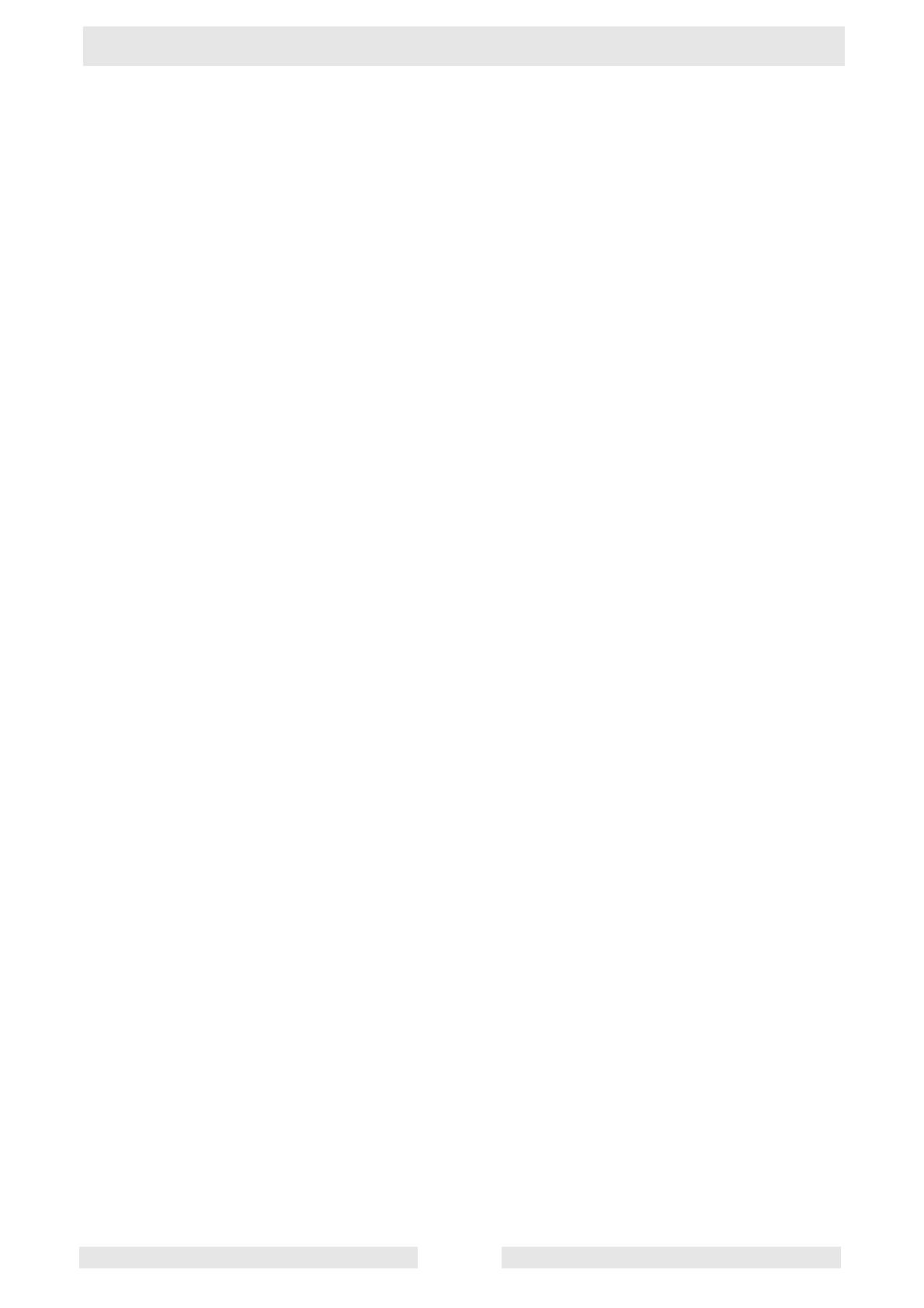
SV00059GB.fm
43
SAFETY INSTRUCTIONS
15. Always wear protective goggles, hearing protection, work gloves, protective helmet, tight-fitting clothing
and safety shoes during operations with the equipment. Shoes and pants must be closed to offer pro-
tection against flying sparks. Wear approved respiratory protection (e.g. a mask) if there is a lot of dust
in the air.
16. Avoid lateral twisting or bending of the machine during the cutting process as well as avoiding impacts,
blows or even dropping the machine as this will lead to damages of the cutting blade. Only subject the
cutting blade to radial burdens (loads).
17. Fix protective hood in lowest position before starting engine.
18. No persons are to be in the vicinity of the floor saw, i.e in front of the floor saw during operation.
19. The operator must stop the blade from turning before relocating the machine.
20. Work calmly and cautiously so as not to endanger others.
Safety checks
1. Floor power saws may only be operated if all operating and safety devices are correctly mounted. This
also includes the water tank.
2. Before starting operation, the operator has to check that all control and safety devices function properly.
3. Before starting the cutting applications check daily as follows:
* proper conditions of cutting blade.
* correct tightening of the cutting blade.
4. In case of defects of the safety devices or other defects reducing the operational safety of thefloor saw,
the supervisor has to be informed immediately.
5. In case of defects jeopardizing the operational safety of the saw, the machine has to be switched off ime
diately.
Maintenance
1. Only use original spare parts. Modifications to this machine including the adjustment of the maximum
speed set by the manufacturer are subject to the express approval of Wacker. In case of nonobservance
all liabilities shall be refused.
2. Switch off the motor and remone spark plug cap from spark plug before carrying out maintenance jobs
to avoid unintentional operation of the machine. Deviations from this are only allowed if the maintenance
jobs require a running motor.
3. Caution when checking the ignition system. The electronic ignitio system produces a very hight voltage.
4. As soon as maintenance and repair jobs have been completed all safety devices have to be reinstalled.
5. Tilting the machine for maintenance works is not allowed.
6. Wash down the floor saw with fresh water after each use to avoid malfunctions.
Transport
1. Disassemble and remove the cutting blade and then place the floor saw in the lowest cutting position
before transporting the machine.
2. During transport, loading and unloading of floor saws by means of lifting devices, appropriate slinging
means or hooks have to be used on the lifting points provided for this purpose on the machine.
3. The load - carrying capacity of the loading ramps has to be sufficient and the ramps have to be secure
such that they cannot turn over. Make sure that no one be endangered by machines turning over or slip-
ping or by moving machine parts.
4. When being transported on vehicles floor saws have to be secured against rolling, slipping or overturn-
ing.
Maintenance checks
According to the conditions and frequency of use, floor saws have to be checked for safe operation at least
once a year by skilled technicians, such as those found at Wacker-Service-Centers and have to be repaired if
necessary.
Please also observe the corresponding rules and regulations valid in your country.