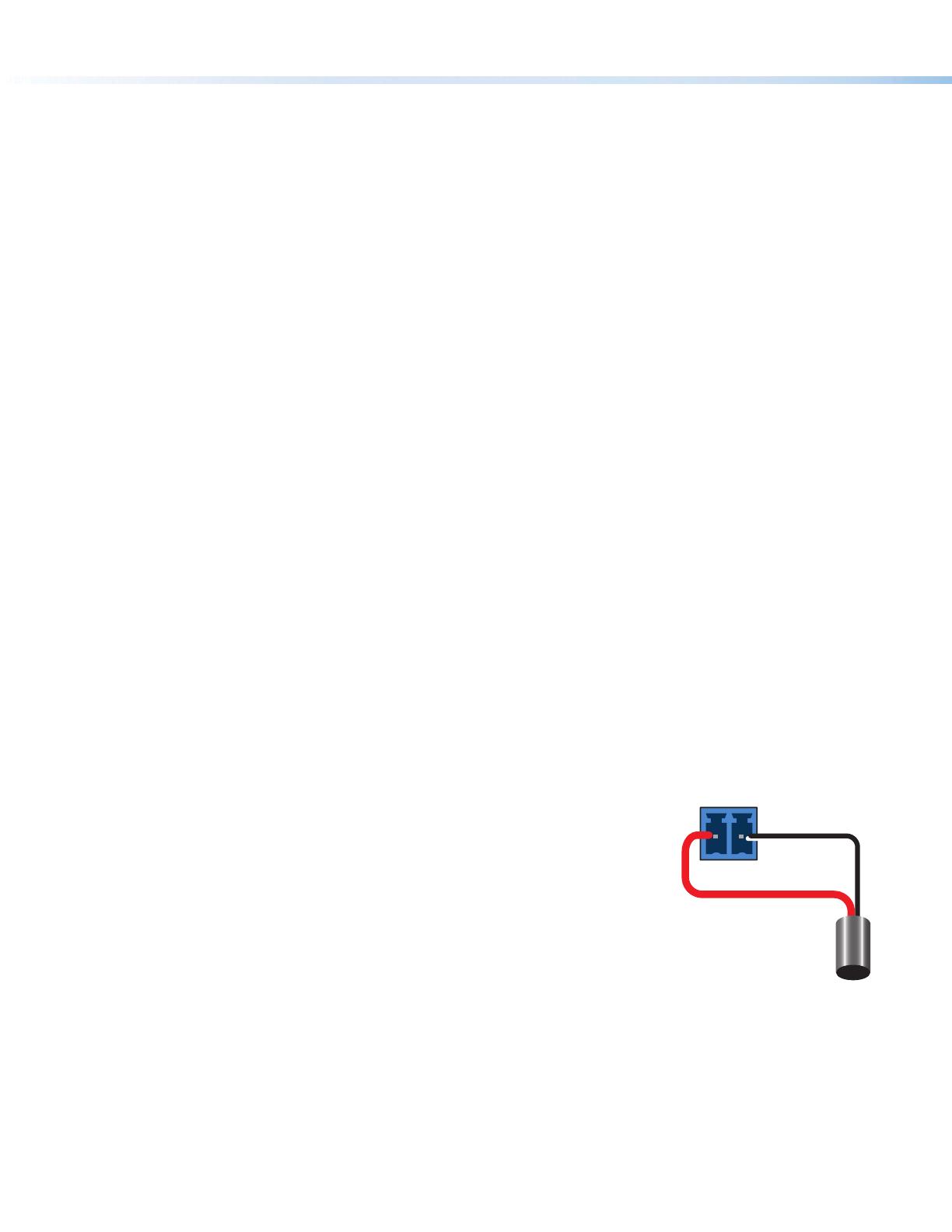
2
IN1804 • Setup Guide (Continued)
• IN1804 DI and DI-DO only: Connect a DTP2 transmitter or XTP matrix switcher to the twisted pair IN connector (
E
). For
cable wiring, see “Twisted Pair Recommendations for the IN and OUT TP Connectors,” below.
IN1804 DI and DI-DO only: To transmit or receive infrared data to and from a source connected to the DTP2 transmitter
or XTP matrix switcher, connect a control device (such as an Extron IPCP Pro Control Processor) to the 3-pole IR Over TP
captive screw port (
D
).
Step 3 — Connect outputs
a. Connect an HDMI output device (or DVI, with an appropriate adapter) to the rear panel HDMI output (
H
). For the IN1804
standard and DI models, two HDMI or DVI output devices can be connected. Secure the HDMI cables with the provided
LockIt brackets (see the IN1804 Series User Guide for instructions).
b. IN1804 DO and DI-DO only: Connect a DTP2, XTP matrix, or HDBaseT-compatible device to the twisted pair OUT
connector (
F
). For cable wiring and recommendations, see “Twisted Pair Recommendations.”
IN1804 DO and DI-DO only: To transmit or receive infrared data to and from a sink connected to the DTP2 receiver, XTP
matrix switcher, or HDBaseT receiver, connect a control device (such as an Extron IPCP Pro Control Processor) to the 3-pole
IR Over TP captive screw port (
G
).
c. Connect a balanced or unbalanced audio output device to the 5-pole captive screw AUDIO OUT connector (
M
). See Audio
Wiring on the next page for more information.
Step 4 — Connect control devices
a. To control the IN1804 device through Ethernet, connect a LAN to the RJ-45 LAN connector (
I
). The default IP address of
the scaler is 192.168.254.254, the default subnet mask is 255.255.255.0, and the default gateway address is 0.0.0.0.
b. For bidirectional RS-232 control, connect a host to the 3-pole captive screw connector (
L
). The baud rate is 9600.
c. For control through USB, connect a host device to the front panel USB mini-B port (see figure 2,
A
, on the next page).
Step 5 — (Optional) Connect contact closure and tally indicator devices
The CONTACT/TALLY panel contains seven 2-pole captive screw connectors, each with two pins labeled C and T (see figure 1,
Q
). Wire contact closure and tally devices to the connectors of each desired port as follows:
• Ports 1 through 4 (for input switching) — Each CONTACT/TALLY connector is labeled with the number of the video input
associated with it. Wire a push button or other contact closure switch to pin C (Contact) and to the shared pin G (Ground,
P
). If using a tally indicator, connect the shared +V pin (5 VDC, required for tally devices without a power supply,
O
) to the
T (Tally) pin. If using an SM Series Show Me
®
cable, see “Using an SM Series Show Me Cable,” below.
• Ports 5 through 7 (configurable via PCS) — Wire a push button or other contact closure switch to pin C (Contact) and to
the shared pin G (Ground,
P
). If using a tally indicator, connect the shared +V pin (5 VDC, required for tally devices without
a power supply,
O
) to the T (Tally) pin.
Using an SM Series Show Me cable:
The Contact and Tally connectors can also be used with Extron Show Me cables. The diagram
at right shows how to wire a Show Me cable to a contact input port (ports 1-4). For each Show
Me cable:
• Connect the red pigtail to the C pin corresponding to the input being used.
• Connect the black pigtail to the T pin of the same port.
Step 6 — Connect power
Connect a 100 to 240 VAC, 50-60 Hz power source to the AC power connector (
A
).
Twisted Pair Recommendations for the IN and OUT TP Connectors
Extron recommends using the following practices to achieve full transmission distances and
reduce transmission errors when connecting to a remote DTP2 endpoint, XTP matrix switcher, or HDBaseT receiver:
• Use Extron XTP DTP 24 SF/UTP cable for the best performance. At a minimum, Extron recommends 24 AWG, solid
conductor, STP cable with a minimum bandwidth of 400 MHz.
• Terminate cables with shielded connectors to the TIA/EIA-T568B standard (see the IN1804 Series User Guide for more
information).
• Limit the use of more than two pass-through points, which may include patch points, punch down connectors, couplers, and
power injectors. If these pass-through points are required, use shielded couplers and punch down connectors.
Black
Red
CT