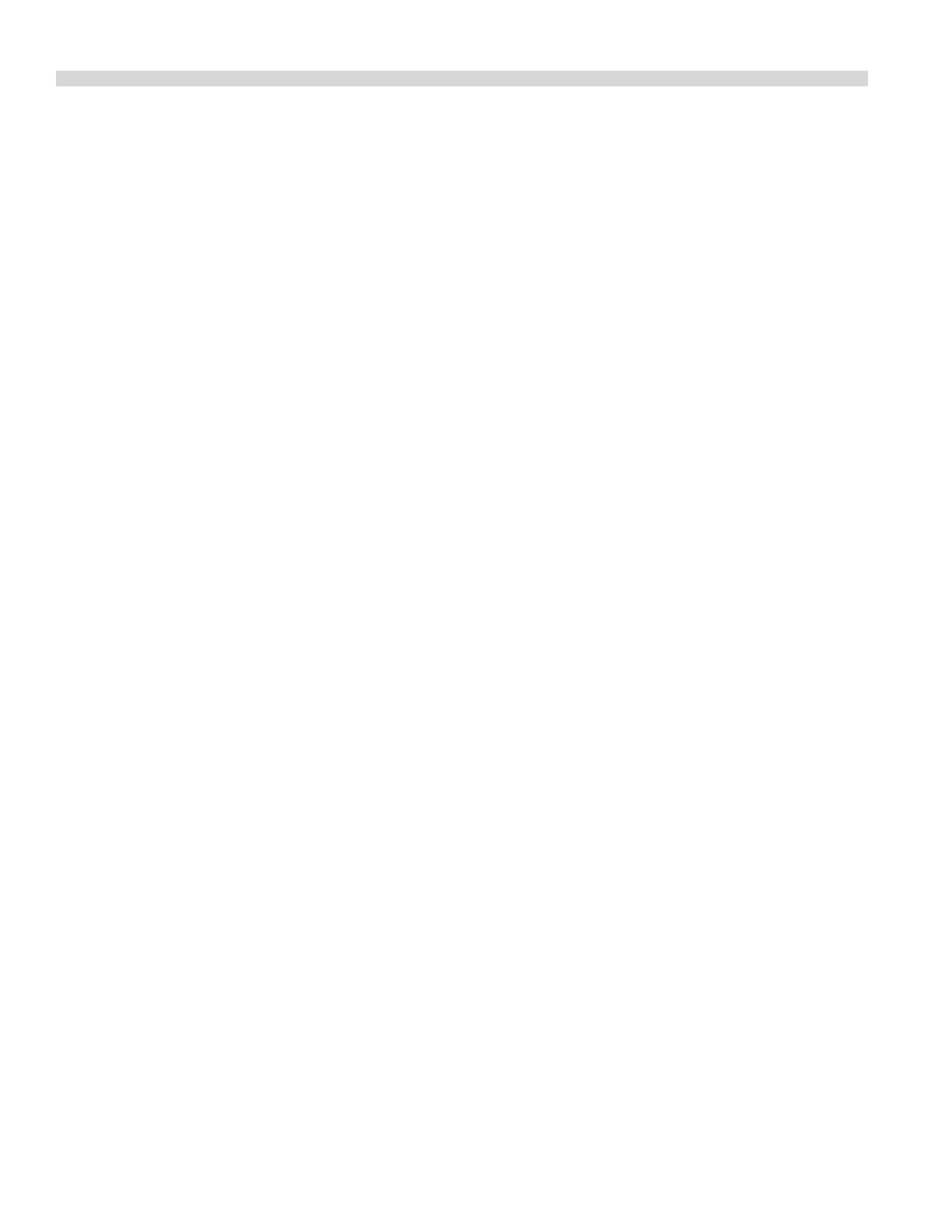
Part # 1382683 (01/08)Page 16
Griddle Tops
Griddle tops are designed to have food cooked directly on
the surface, for example hamburgers, eggs, pancakes, has
browns, etc. Do not put pots or pans on the griddle surface.
This will scratch or nick the surface, resulting in sticking and
scorching of product. Never salt food on a griddle because
this will cause a gummy residue to build up, making the
griddle more dicult to clean. Avoid hitting the griddle plate
with a spatula, as this will also nick the surface. The most
frequently used temperature range for griddles is 325° to
350°F, (163° to 177°C). Check and drain the grease drawer
frequently during heavy use to prevent overowing. Over
a period of time, some discoloration of the steel griddle
plate will occur. This will not aect performance. For best
cooking results, keep the griddle surface as clean and shiny
as possible.
Oven (Standard)
The temperature is automatically controlled by the
thermostat, so satisfactory results can be obtained with
condence again and again.
For best performance, these instructions should be followed:
A. Grid Shelves There are two shelf positions. The correct
shelf position should be decided by the size of the
product to be cooked. When the best position has been
determined, push the shelf fully into the oven until
contact with the back wall stops its movement.
B. Tray Size One cake tray up to 24 x 22 inches,
(610 x 560mm), can be placed on each shelf. Single trays
or dishes should be centered on the shelf. Trays must not
be allowed to overhand the shelf on any side, since this
will inhibit proper heat circulation.
C. Preheat time Allow at least 45 minutes after turning on
the cold oven, with the thermostat set at the desired
temperature before loading with food. Load product
quickly and immediately close the door.
D. Thermostat The thermostat automatically controls the
heat to maintain the selected temperature.
PRODUCT APPLICATION INFORMATION Continued
Range Base Convection Oven
Generally, a temperature 25° to 50°F (-4° to 10°C), lower than
that specied in recipes for standard ovens should be used.
Cooking time may be reduced, depending on the product.
A 2% to 5% reduction in cook time is a general rule. Keep a
close check on any product being prepared for the rst time.
The size of the load, temperature of the product going in,
and moisture content are the major factors that inuence
necessary cook times and temperatures. Successfully
prepared products should be recorded with their times and
temperatures for future reference.
Preheat the oven thoroughly before loading. It will take
approximately 15 minutes for the oven to reach 350ºF, 177ºC.
Best results will be attained when the oven is allowed to
preheat for 30 minutes or more for thorough heat saturation.
Center the load on the oven racks to allow for proper heat
circulation around the sides. The oven will hold three, (3),
18” x 26”, (457mm x 660mm), sheet pans, six, (6), 12” x 20” x
2.5”, (305mm x 508mm x 64mm), steam table pans, or one,
(1) 17.75” x 25.75”, (451mm x 654mm), roast pan. Never place
pans directly on the oven bottom. Always use the lowest rack
position that will allow the heated air to circulate within the
oven cavity. Load and unload food as quickly as possible to
prevent excessive temperature drop. For even baking, avoid
using warped pans.
Do not use a deep pan for shallow cakes, cookies, etc., as heat
circulation across the top of these items is essential for even
browning. To prevent excessive shrinkage, roast meats at a low
temperature; 250°F, (121° to 163° C), When rethermalizing frozen
products, preheat the oven 50°F, (10°C), higher than the cooking
temperature to compensate for heat loss during and after
loading. Return the thermostat to the cooking temperature after
loading.
To conserve energy, turn the oven o when not in use. If you
cover pans with aluminum foil, be sure to crimp it tightly
around the edges to prevent the foil from blowing o in the
oven. Any food or other matter which becomes lodged in the
fan must be removed as soon as the oven is cool.