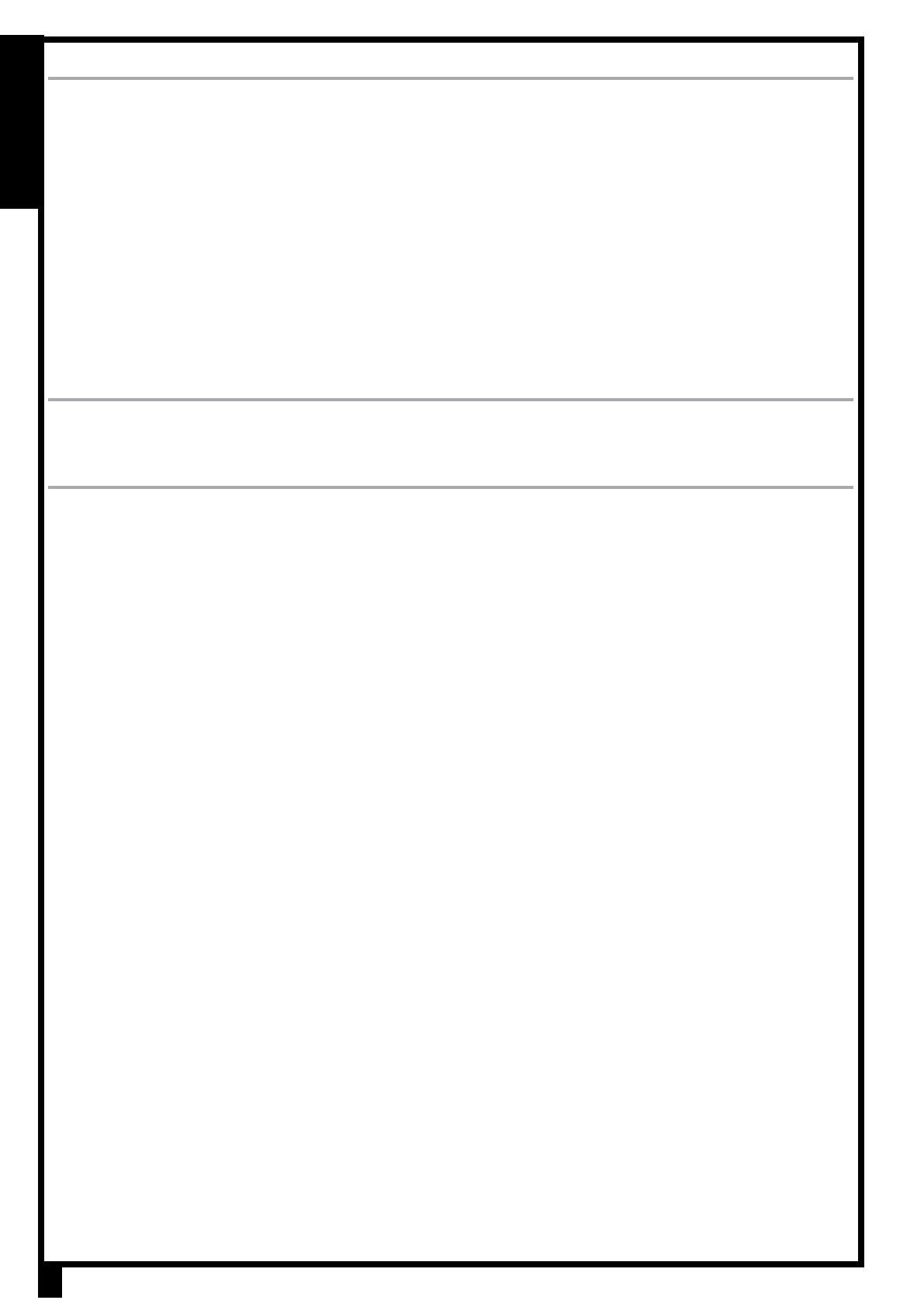
ENGLISH
2
THANK YOU
for choosing this General International machine. This tool has been
carefully tested and inspected before shipment and if properly used and
maintained, will provide you with years of reliable service. To ensure
optimum performance and trouble-free operation, and to get the most
from your investment, please take the time to read this manual before
assembling, installing and operating the unit.
The manual’s purpose is to familiarize you with the safe operation, basic
function, and features of this tool as well as the set-up, maintenance and
identication of its parts and components. This manual is not intended
as a substitute for formal woodworking instruction, nor to oer the user
instruction in the craft of woodworking. If you are not sure about the safety
of performing a certain operation or procedure, do not proceed until you
can conrm, from knowledgeable and qualied sources, that it is safe to do so.
Once you’ve read through these instructions, keep this manual handy for
future reference.
GENERAL
®
INTERNATIONAL
WARRANTY
All component parts of General
®
International products are carefully
inspected during all stages of production and each unit is thoroughly
inspected upon completion of assembly.
2
-
YEAR LIMITED WARRANTY
All products are warranted for a period of 2 years (24 months) from the
date of purchase. General
®
International agrees to repair or replace any
part or component which upon examination, proves to be defective in
either workmanship or material to the original purchaser during this 2-year
warranty period, subject to the “conditions and exceptions” as listed below.
Repairs made without the written consent of General International will void
the warranty.
DISCLAIMER
The information and specications in this manual pertain to the unit as
it was supplied from the factory at the time of printing. Because we are
committed to making constant improvements, General International
reserves the right to make changes to components, parts or features of
this unit as deemed necessary, without prior notice and without obligation
to install any such changes on previously delivered units. Reasonable care
is taken at the factory to ensure that the specications and information in
this manual corresponds with that of the unit with which it was supplied.
However, special orders and “after factory” modications may render some
or all information in this manual inapplicable to your machine. Further, as
several generations of this tool model and several versions of this manual
may be in circulation, if you own an earlier or later version of this unit, this
manual may not depict your machine exactly. If you have any doubts or
questions contact your retailer or our support line with the model and serial
number of your unit for clarication.
TO FILE A CLAIM
To le a claim under our Standard 2-year Limited Warranty, all defective
parts, components or machinery must be returned freight or postage
prepaid to General
®
International, or to a nearby distributor, repair center
or other location designated by General
®
International. For further details
contact our service department: USA toll-free (844) 877-5234 or (419)
877-5234 / Canada toll-free (888) 949-1161 or (604) 420-2299 or through
our website: www.gipowerproducts.com.
Along with the return of the product being claimed for warranty, a copy of
the original proof of purchase and a “letter of claim” must be included (a
warranty claim form can also be used and can be obtained, upon request,
from General
®
International or an authorized distributor) clearly stating
the model and serial number of the unit (if applicable) and including
an explanation of the complaint or presumed defect in material or
workmanship.
CONDITIONS AND EXCEPTIONS
This coverage is extended to the original purchaser only. Prior warranty
registration is not required but documented proof of purchase, i.e. a copy
of original sales invoice or receipt showing the date and location of the
purchase as well as the purchase price paid, must be provided at the time
of claim.