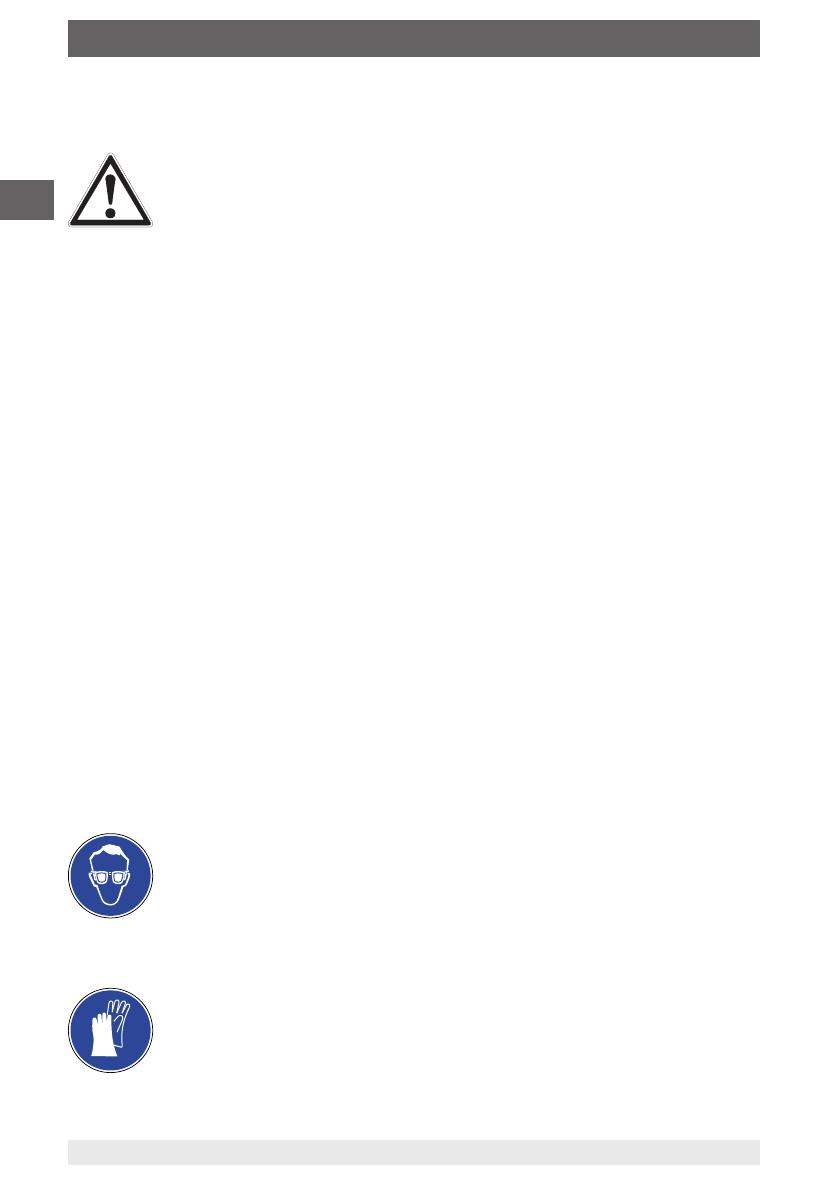
8
WIKA operating instructions, model GDM-RC-100
EN
14385258.02 06/2020 EN/DE/FR/ES
3.5 Personnel qualification
WARNING!
Risk of injury should qualification be insufficient
Improper handling can result in considerable injury and damage to property.
▶
The activities described in these operating instructions may only be
carried out by skilled personnel who have the qualifications described
below.
Skilled personnel
Skilled personnel, authorised by the operator, are understood to be personnel
who, based on their technical training, knowledge of measurement and control
technology and on their experience and knowledge of country-specific regulations,
current standards and directives, are capable of carrying out the work described and
independently recognising potential hazards.
Specically when using SF₆ gas
The plant operator must ensure that the handling of SF
6
gas is only carried out by a
qualied company or by qualied persons who have been specially trained in accord-
ance with IEC 61634, section 4.3.1 or IEC 60480, section 10.3.1.
3.6 Personal protective equipment
The personal protective equipment is designed to protect the skilled personnel from
hazards that could impair their safety or health during work. When carrying out the
various tasks on and with the instrument, the skilled personnel must wear personal
protective equipment.
Follow the instructions displayed in the work area regarding personal protective
equipment!
The requisite personal protective equipment must be provided by the operating
company.
Safety goggles in accordance with EN 166, class 2, mechanical
strength class S
Safety goggles must be worn during the entire period when working on
hoses or gas containers (e.g. gas cylinders, tanks).
The safety goggles protect the eyes from any flying particles, escaping
gas and liquid splashes.
Protective gloves against heat in accordance with EN ISO 13732-1
and against cold in accordance with EN ISO 13732-3
The protective gloves must be worn over the entire period when working
on hoses, gas containers (e.g. gas cylinders, tanks) or components which
heat up to over 60 °C.
3. Safety