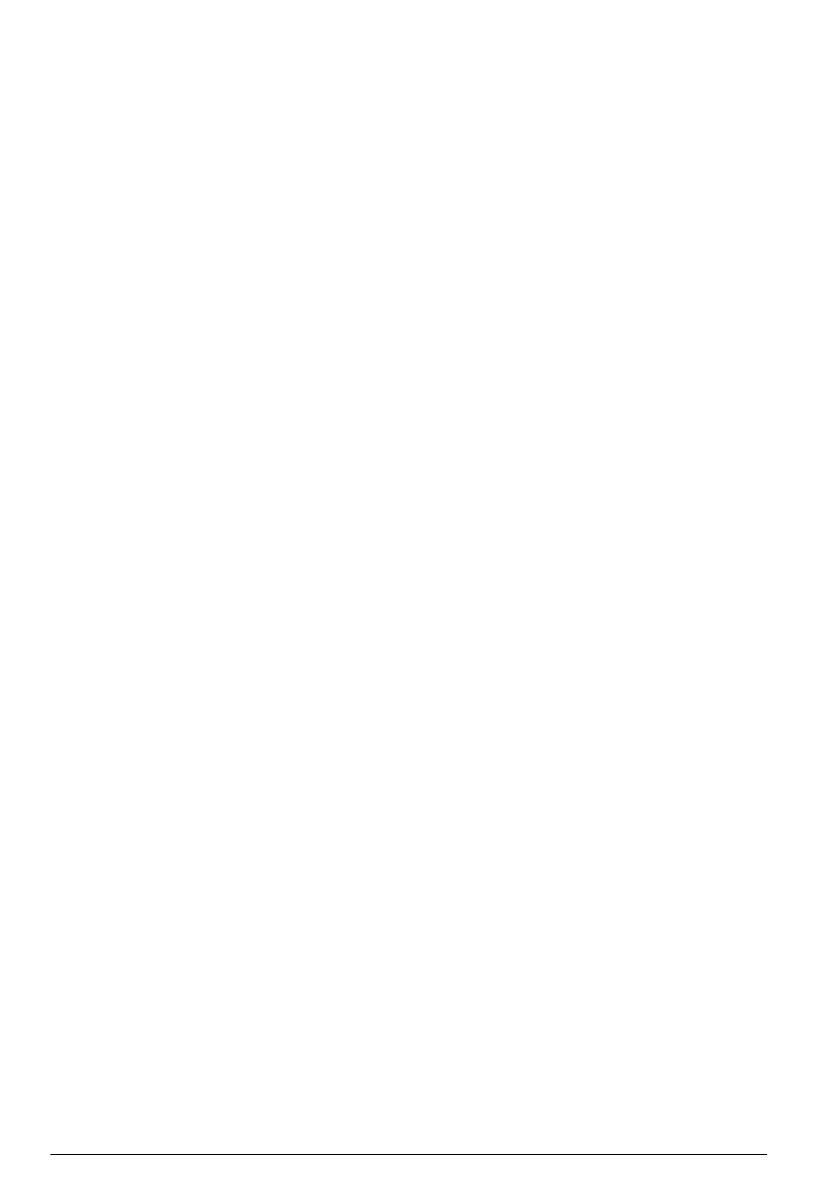
This Class A digital apparatus meets all requirements of the Canadian Interference-Causing
Equipment Regulations.
Cet appareil numérique de classe A répond à toutes les exigences de la réglementation canadienne
sur les équipements provoquant des interférences.
FCC Part 15, Class "A" Limits
Supporting test records reside with the manufacturer. The device complies with Part 15 of the FCC
Rules. Operation is subject to the following conditions:
1. The equipment may not cause harmful interference.
2. The equipment must accept any interference received, including interference that may cause
undesired operation.
Changes or modifications to this equipment not expressly approved by the party responsible for
compliance could void the user's authority to operate the equipment. This equipment has been tested
and found to comply with the limits for a Class A digital device, pursuant to Part 15 of the FCC rules.
These limits are designed to provide reasonable protection against harmful interference when the
equipment is operated in a commercial environment. This equipment generates, uses and can
radiate radio frequency energy and, if not installed and used in accordance with the instruction
manual, may cause harmful interference to radio communications. Operation of this equipment in a
residential area is likely to cause harmful interference, in which case the user will be required to
correct the interference at their expense. The following techniques can be used to reduce
interference problems:
1. Disconnect the equipment from its power source to verify that it is or is not the source of the
interference.
2. If the equipment is connected to the same outlet as the device experiencing interference, connect
the equipment to a different outlet.
3. Move the equipment away from the device receiving the interference.
4. Reposition the receiving antenna for the device receiving the interference.
5. Try combinations of the above.
Product components
Make sure that all components have been received. Refer to Product overview on page 6. If any
items are missing or damaged, contact the manufacturer or a sales representative immediately.
Product overview
The CD300 controller is used with NX7500, NK3300 or NV3300 optical sensors to do photometric
measurements in aqueous solutions (e.g., waste water, drinking water, environmental applications).
The controller has a color touch screen that shows the measurement data, calibration and
configuration information. The controller saves measurement values, calibration files and service
settings on a 2 GB Mirco SD card. The controller can communicate with and export data to a PC with
an M12/RJ-45 Ethernet cable.
The potential-free relay output is used to control external devices (e.g., control devices and alarm
devices). The two 4-20 mA analog outputs are used for analog signaling or to control external
devices. Refer to Figure 1.
6
English