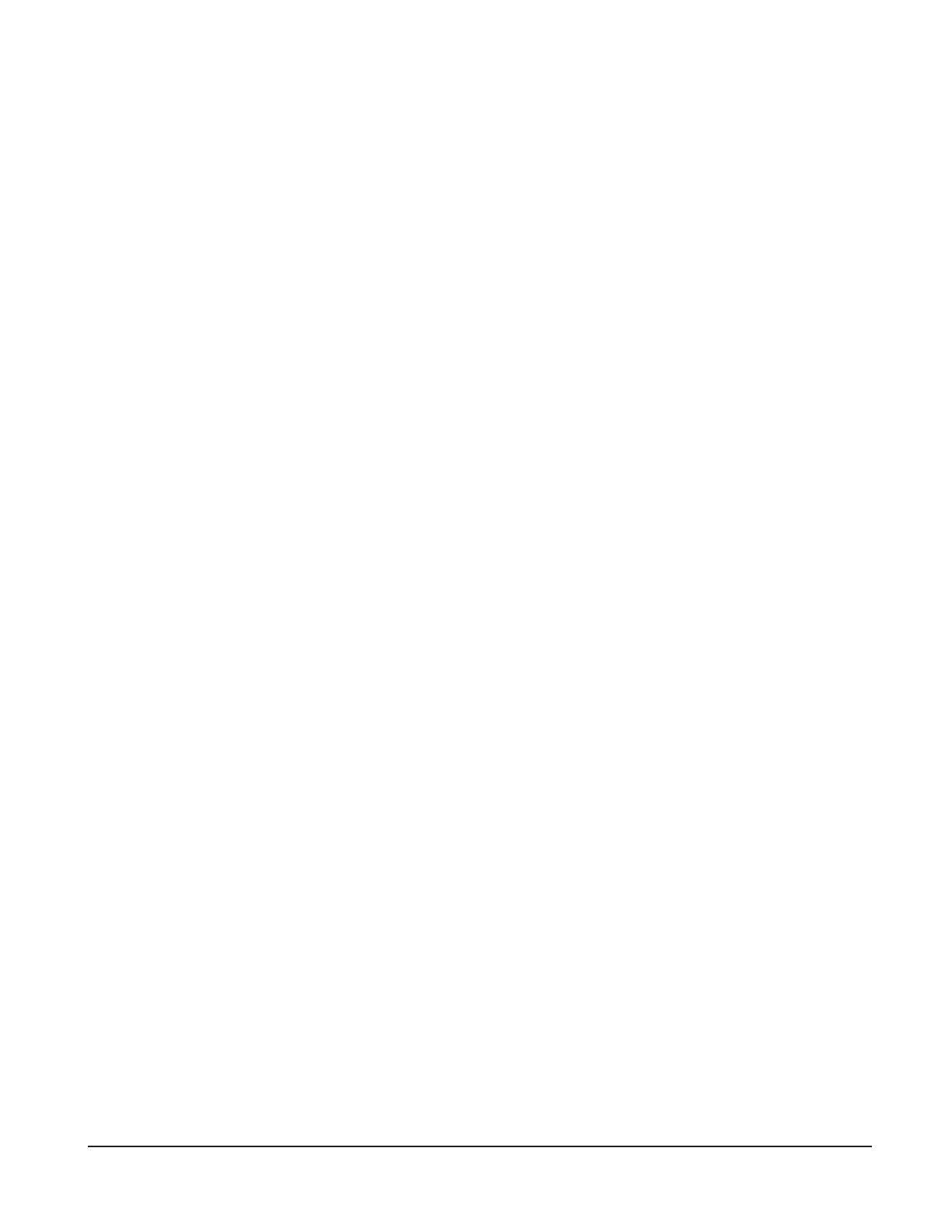
– 3 –
TABLE OF CONTENTS
NOTES FOR THE INSTALLERS ....................................................................4
HOW TO REDUCE THE CLEARANCE HEIGHT OF THE CONTROL BOX DURING MOVE-IN ...................4
HOW TO REMOVE ENERGY RECOVERY/VENT HOUSING FOR LOW CLEARANCE .........................6
UNPACKING ...................................................................................7
Removing Each Section From Its Skid ............................................................7
LOCATION .....................................................................................8
Positioning the Center Section ..................................................................8
Leveling the Center Section ....................................................................8
ASSEMBLY ....................................................................................9
Rotating Control Box 90 Degrees ................................................................9
Installing Foam Tape on Chamber Flanges & Control Box Mounting Surface ..............................9
Attaching Control Box to Unload Section .........................................................10
Positioning the Adjacent Load or Unload Sections ..................................................12
Leveling the Load and Unload Sections ..........................................................12
Joining the Sections Together ..................................................................12
InstallingtheCurtainHangersandUnloadAirBafe ................................................13
Installing the Saddle Joint – Bottom of Chamber Flanges ............................................14
Installing the Flowback Pipe (Wash to Prewash Tanks) ..............................................15
Installing the Drain Pipe ......................................................................15
Relocating Master Drain to Load End (Only Machines Equipped with Auto Clean,
Auto Delime, & the ASR Section) .............................................................16
Drain Back Pan Installation ....................................................................20
Blower Dryer Assembly .......................................................................21
Advansys Module Installation ..................................................................23
Control Box Connections .....................................................................23
Elecric Booster Heater Wiring ..................................................................24
Door and Drain Interlock Switches (Prewash to Wash Tank) ..........................................24
PLUMBING CONNECTIONS ......................................................................25
Water Supply ...............................................................................25
Fill .......................................................................................25
Final Rinse ................................................................................25
Drain .....................................................................................26
Line Strainers ..............................................................................26
Steam Supply (When Equipped) ................................................................26
Steam Tank Heaters – Condensate Return Lines ...................................................27
Steam Booster Heater – Condensate Return Line & Relief Valves .....................................27
Steam Blower Dryer (When Equipped) – Condensate Return Line .....................................27
Fill & Auto Clean (When Equipped) Hose Connections ..............................................27
ELECTRICAL CONNECTIONS ....................................................................30
Motor Overloads ............................................................................30
Checking Motor Rotation (Three-Phase Motors) ...................................................31
Separate Electrical Connections ................................................................31
Voltage Adjustment ..........................................................................31
Electrical Connection – Detergent & Rinse Aid Dispensers ...........................................32
External Vent Fan Control .....................................................................32
CONVEYOR ASSEMBLY .........................................................................33
Loading and Joining the Conveyor Sections .......................................................33
Conveyor Offset Side Bar .....................................................................36
Adjusting the Conveyor Take-Up Unit (Load Section) ................................................37
FT1000eConveyorJamSwitchSettingVerication/Adjustment .......................................38
MISCELLANEOUS ..............................................................................40
Vent ......................................................................................40
AirBafeSettings ...........................................................................40
CurtainCongurations .......................................................................44
Prewash, Wash, and Power Rinse Arms .........................................................53
Dual Rinse/Final Rinse Arms ..................................................................53
Automatic Soil Removal (ASR) Arms (When Equipped) ..............................................54
Lower Trim Panels (Front) and Rear Panels .......................................................54
Calibrating the Electric Booster Thermostat .......................................................55
Conveyor Gear Motor ........................................................................55
Delime Indicator Setup .......................................................................55
SERVICE .....................................................................................55