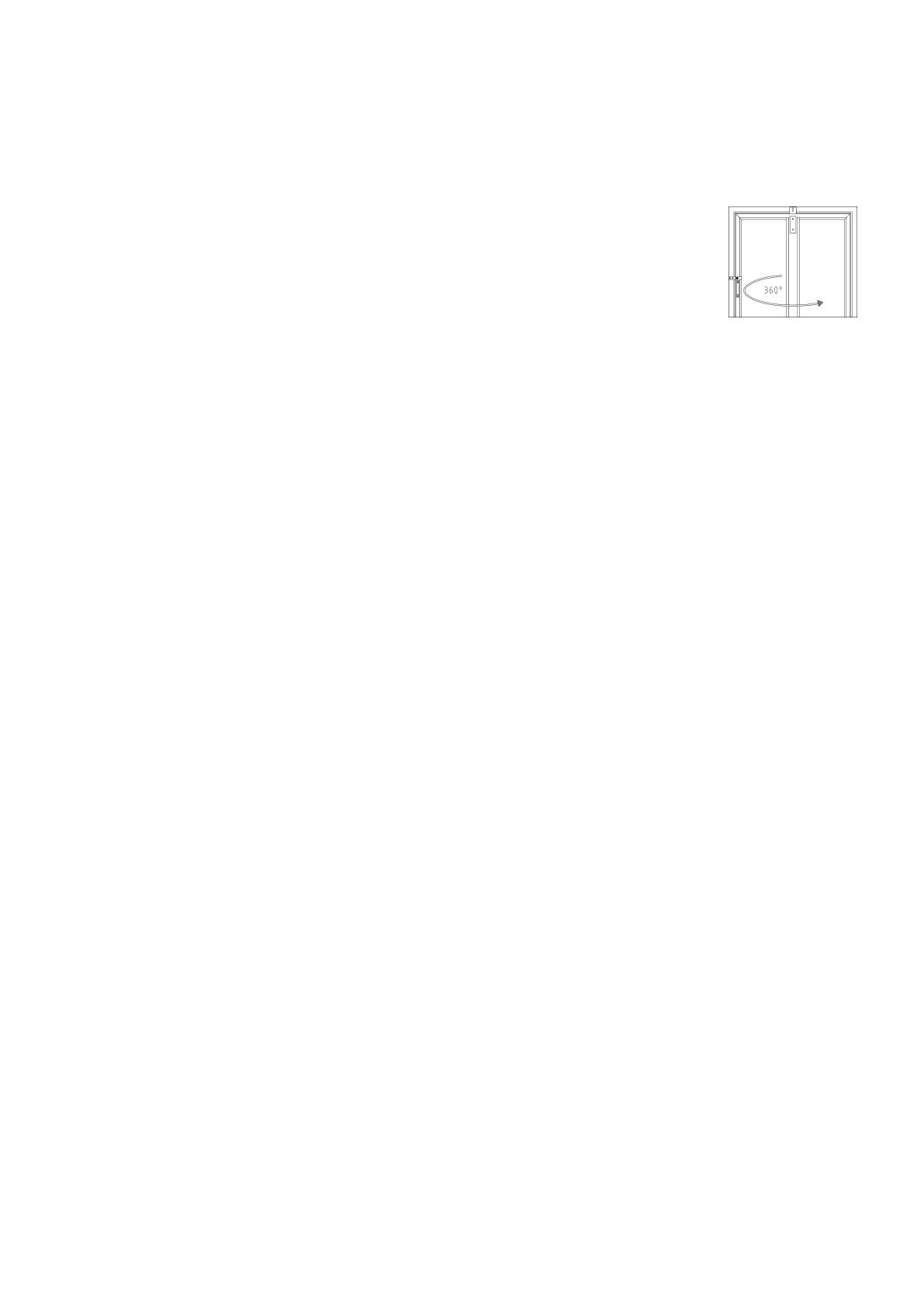
• Lubricate the moving parts of the devices, the shoulders and waistband of the dummy, the exterior gasket
and the rotation pins of the glass parts by means of the spray can the machine is supplied with, containing
“liquid silicone”.
• If the machine is new or left unused for a long time it is advisable to carry out some ironing cycles without
garments.
Warning: Never start the ironing cycle when the machine is still cold. Even in case of short intervals it is advisable
to switch on the hot air for a few seconds in order to heat up the cabin before continuing to work.
7.3 OPERATION
The BOX-1 features in the front a special glass door called “Securit Saint Gobain” hinged on
two central pins and swiveling at 360°. The glass door has to swivel always in the same
direction: the external handles on the door’s left side have always to be PULLED and never be
pushed. Hence, seen from the outside, the door’s rotation is from left to right.
7.4 DEVICES
The BOX-1 features sleeve stretchers and a series of pliers, which are used in different ways and completing the
shoulder and waistband devices.
• SHOULDER device
It has to be fit onto the lower pin of the support, by centering the reference pegs in the relevant grooves of the
column. The shoulder device is used for jackets, coats, blousons and trench coats. It consists of a dummy trestle
with a cloth of a particular shape suitable for any size. The cloth of the shoulder device can be extended up to
the base of the same: during the steaming and the air blowing it inflates, taking a perfect trunk-conical shape. In
this way the garment hems are kept firm, making an additional finishing unnecessary. The shoulder device can
be shifted towards the operator, by rotating it from the right to the left, thus making the application of the pliers
on the back side, as well as the control of the garment before and after the ironing cycle easier.
• TROUSER device
It consists of two parts: an upper one (waistband stretcher) which has to be connected to the specially designed
fixed pins situated on top of the door and to be fixed by means of the hand wheel. The lower one consists of a
trolley with pliers for fixing the two trouser legs. The waistband device is used for the ironing of trousers.
• MULTIPLE device
It is installed like the upper part of the waistband-stretcher. The multiple device is used for the ironing of garments
not requiring a particular tension: dresses, blouses, jerseys, jumpers, as well as curtains and blankets. It is
possible to place several garments on the multiple device during the same ironing cycle (up to 5), by using wire,
wooden or plastic hangers, according to the delicacy of the garments, type of fabric, etc.
7.5 GARMENT PLACING
• Jackets – Coats – Raincoats
Turn the device outwards, then put the garment on the same, button it up and adjust the shoulder width by turning
the hand wheel. Apply the two sleeve stretchers, grip with the pliers the front hems and rotate the garment
towards the door, then grip the back part with the second pliers (or with two vertical pliers in case of jackets with
vents). Please be reminded that if the device is not turned towards the door it is not possible to introduce it into
the cabin as it would hit against the external edge.
• Skirts
These can be placed on the same device as the one for trousers, by applying the pliers on the lower hem. For
silk or jersey skirts the use of pliers can be unnecessary or unadvisable: these skirts can also be ironed by putting
them on a normal wire hanger and by using the multiple device.
• Dresses (princesses)
For this kind of garment it is possible to use either the shoulder or the multiple device. The first is suitable for
smooth or heavy fabrics. For light and delicate garments it is advisable to use the multiple device. In this case
the dress is placed on a wire hanger which has to be hanged on the device. If the wire hanger should leave
marks on the shoulder, you can use common wooden and rounded hangers of the same size of the garment’s
shoulders width.
• Jerseys – Blouses – Jumpers
These are placed on metal hangers and then on the multiple device. In some cases the ironing result is complete,
in others only partial. However, in view of the fact that the ironing operation is simple and quick, it is worthwhile
to use it for any garment, paying attention to use wire or wooden hangers according to the garment’s delicacy,
in order to avoid any possible marks on the shoulders.
• Curtains – Blankets
The steam eliminates the creases, giving the same ironing result to curtains and blankets as obtained with an
ironing table. Considering the easy and quick operation it is worthwhile to carry it out: you will only have to touch
up the hems. Fold the curtains, and put them onto the hanger of the multiple device before starting the ironing
cycle.