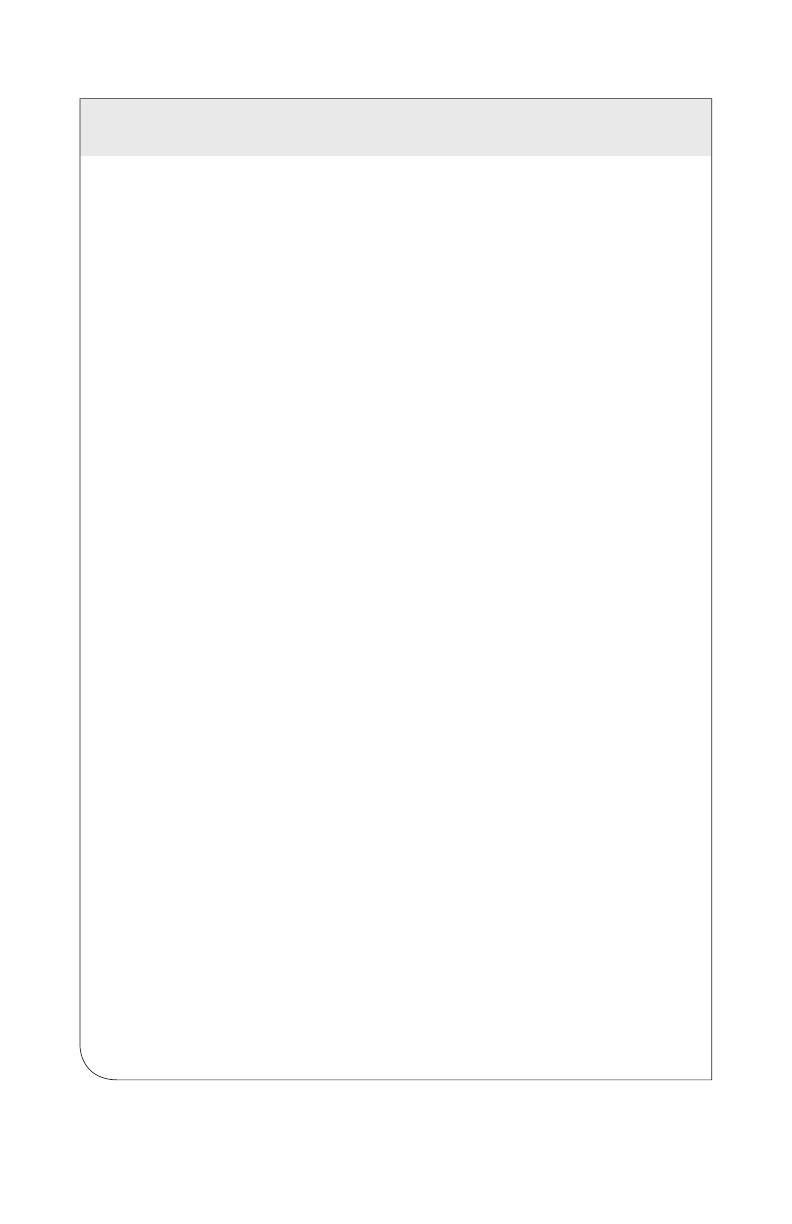
3.3 Preparation
• Verify the model number and electrical specifications of the device being installed
to confirm they are appropriate for the intended electrical service (see Section 2).
• Consult local codes for any possible permits or inspections required before
beginning electrical work.
• Make sure all tools to be used during installation have proper insulation ratings.
• This Mini Meter is only for use in complete equipment or associated equipment
applications where the combination is in accordance with the following Conditions
of Acceptability as determined by Underwriters Laboratories.
• The Mini Meter shall be installed in an UL LISTED enclosure.
• The Mini Meter is suited for applications an overload Category III and only
installed on the load side of branch-circuit protection.
• The counter pins 1 and 2 and +12VDC are not isolated from the mains voltage
sensing circuits and are considered hazardous live voltage. These circuits shall
not be user accessible after final installation in UL LISTED enclosure.
• The Isolated Outputs, as noted on the label, are isolated from the power mains
and are derived from low voltage circuits. These Isolated Outputs and CT circuits
shall maintain a 3mm clearance/creepage and 3000Vac dielectric strength.
Suitability of this isolation must be verified if these output circuits are accessible
in the end use application.
• Only CT's as specified in this manual and UL 2808 LISTED - Energy-monitoring
Current Transformer (XOBA/7) with a 0.1 amp rated secondary shall be used with
this Mini Meter.
• Intended for use with a 15 A Branch Circuit Overcurrent Protection device.
• Class 1 wiring methods shall be used for the voltage input/measurement circuits,
current sensing CT secondary circuit, +12Vdc, and counter connections.
• The isolated outputs may use Class 2 wiring methods if supplied by a separate
Class 2 source and the wiring is routed minimum 6mm (1/4 in.) from all
other wiring connected to the device and in the end use enclosure. If not so
segregated, Class 1 wiring methods shall be used.
• CT shall not be installed in equipment where they exceed 75 percent of the wiring
space of any cross-sectional area within the equipment.
• The current transformers shall not be installed where they can block any
ventilation openings within the main panel.
• Secure CT and route the wires so that they do not directly contact live terminals,
uninsulated bus of low voltage, mains circuits or conductors of other circuits.
• Associated leads of the CT and the Mini Meter shall be installed within the same
overall enclosure.
• The end-use equipment shall be marked with the following the word "Warning
- To reduce risk of electric shock, always open or disconnect the monitored
circuit from power-distribution system (or service) of building before installing or
servicing current-sensing transformers."
• When any critical markings are provided in the meter instructions instead of in
the end product documentation, the end product documentation shall include a
reference to the meter instructions.
• The isolated outputs shall be supplied by a SELV or other low voltage supply
providing double or reinforced insulation unless the isolated outputs do not
extend outside the overall enclosure and do not connect to user accessible
circuits.
• This Mini Meter unit is not intended for use as a retrofit application within
panelboards and switchgear. Additional evaluation for use inside the panelboard
or switchgear is required.
• Pollution Degree 2: Normally only non-conductive pollution occurs. Occasionally,
however, a temporary conductivity caused by condensation must be expected.
3 INSTALLATION INSTRUCTIONS
4