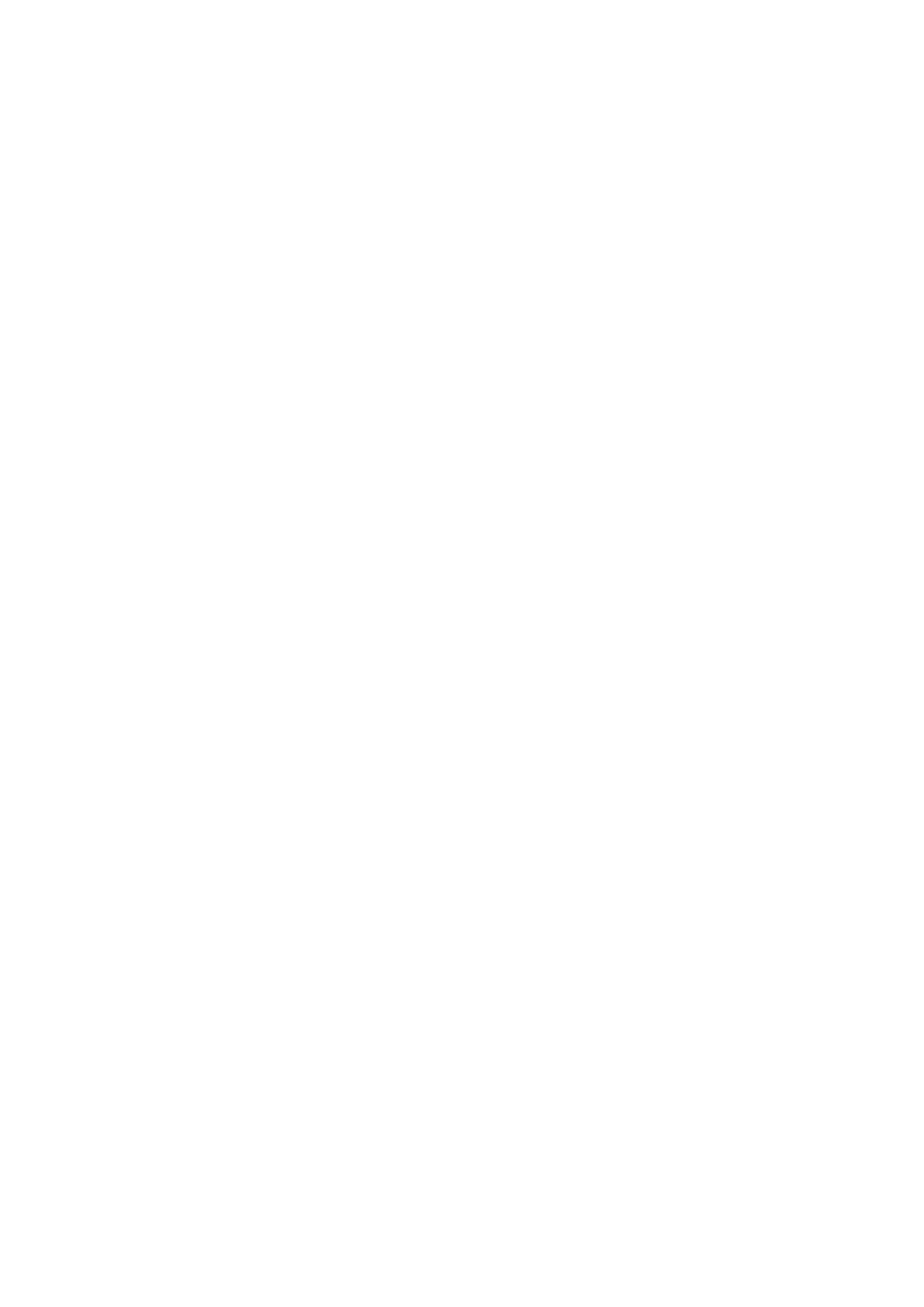
ENGLISH
34
INDEX
1. GENERAL ...........................................................................................................................................................................................37
1.1 Applications .......................................................................................................................................................................................37
1.2 Description of the Integrated Inverter ...............................................................................................................................................38
1.3 Integrated Expansion Vessel ............................................................................................................................................................38
1.4 Technical characteristics ...................................................................................................................................................................39
2. INSTALLATION ..................................................................................................................................................................................39
2.1 - Vertical Configuration ......................................................................................................................................................................40
2.1.1 Hydraulic connections ............................................................................................................................................................... 40
2.1.2. Loading Operation - Installation above head and below head ............................................................................................... 41
2.2 - Horizontal Configuration .................................................................................................................................................................41
2.2.1 Hydraulic connections ............................................................................................................................................................... 41
2.2.2 Orientation of the Interface Panel ............................................................................................................................................. 42
2.2.3 Loading Operation - Installation above head and below head ................................................................................................ 42
3. COMMISSIONING ..............................................................................................................................................................................42
3.1 Electrical Connections .......................................................................................................................................................................42
3.2 Configuration of the Integrated Inverter ..........................................................................................................................................43
3.3 - Priming............................................................................................................................................................................................43
4. THE KEYPAD AND THE DISPLAY ..................................................................................................................................................44
4.1 Direct Access with a Combination of Keys.......................................................................................................................................45
4.2 - Access by name with a drop-down menu ......................................................................................................................................46
4.3 - Structure of the menu pages. (FIRMWARE VERSION ≤ 4.x.x) ...................................................................................................47
4.4 - Structure of the menu pages. (FIRMWARE VERSION ≥ 4.x.x) ...................................................................................................48
4.5 - Blocking parameter setting by Password .......................................................................................................................................49
4.6 - Enabling and disabling the motor ...................................................................................................................................................49
5. MEANING OF THE INDIVIDUAL PARAMETERS ...........................................................................................................................49
5.1 User Menu .........................................................................................................................................................................................49
5.1.1 – Status ...................................................................................................................................................................................... 49
5.1.2 - RS: Rotation speed display ..................................................................................................................................................... 49
5.1.3 - VP: Pressure display ............................................................................................................................................................... 50
5.1.4 - VF: Flow display ...................................................................................................................................................................... 50
5.1.5 - PO: Absorbed power display .................................................................................................................................................. 50
5.1.6 - C1: Phase current display ....................................................................................................................................................... 50
5.1.7 - SV: Supply voltage .................................................................................................................................................................. 50
5.1.8 - SR: Supply range .................................................................................................................................................................... 50
5.1.9 - TE: Dissipator temperature display ........................................................................................................................................ 50
5.1.10- PKm: Pressure measured at intake ....................................................................................................................................... 50
5.1.11 - Operating hours and number of starts.................................................................................................................................. 50
5.1.12 - PI: Power histogram .............................................................................................................................................................. 50
5.1.13 - Output flow meter .................................................................................................................................................................. 50
5.1.14 - NT: Display of network configuration (2) ................................................................................................................................ 50
5.1.15 - VE: Version Display............................................................................................................................................................... 50
5.1.16 - FF: Fault & Warning display (Log) ........................................................................................................................................ 50
5.2 - Monitor Menu ..................................................................................................................................................................................51
5.2.1 - CT: Display contrast ................................................................................................................................................................ 51
5.2.2 - BK: Display brightness ............................................................................................................................................................ 51
5.2.3 - TK: Backlight switch-on time ................................................................................................................................................... 51
5.2.4 - LA: Language .......................................................................................................................................................................... 51
5.2.5 - TE: Dissipator temperature display ........................................................................................................................................ 51
5.3 - Setpoint Menu .................................................................................................................................................................................51
5.3.1 - SP: Setting the setpoint pressure ........................................................................................................................................... 51
5.4 - Manual Menu ...................................................................................................................................................................................51
5.4.1 - Status ....................................................................................................................................................................................... 52
5.4.2 - RI: Speed setting ..................................................................................................................................................................... 52
5.4.3 - VP: Pressure display ............................................................................................................................................................... 52
5.4.4 - VF: Flow display ...................................................................................................................................................................... 52
5.4.5 - PO: Absorbed power display .................................................................................................................................................. 52
5.4.6 - C1: Phase current display ....................................................................................................................................................... 52
5.4.7 - RS: Rotation speed display ..................................................................................................................................................... 52
5.4.8 - SV: Supply voltage .................................................................................................................................................................. 52
5.4.9 - SR: Supply range .................................................................................................................................................................... 52
5.4.10 - TE: Dissipator temperature display ...................................................................................................................................... 52
5.5 - Installer Menu ..................................................................................................................................................................................52