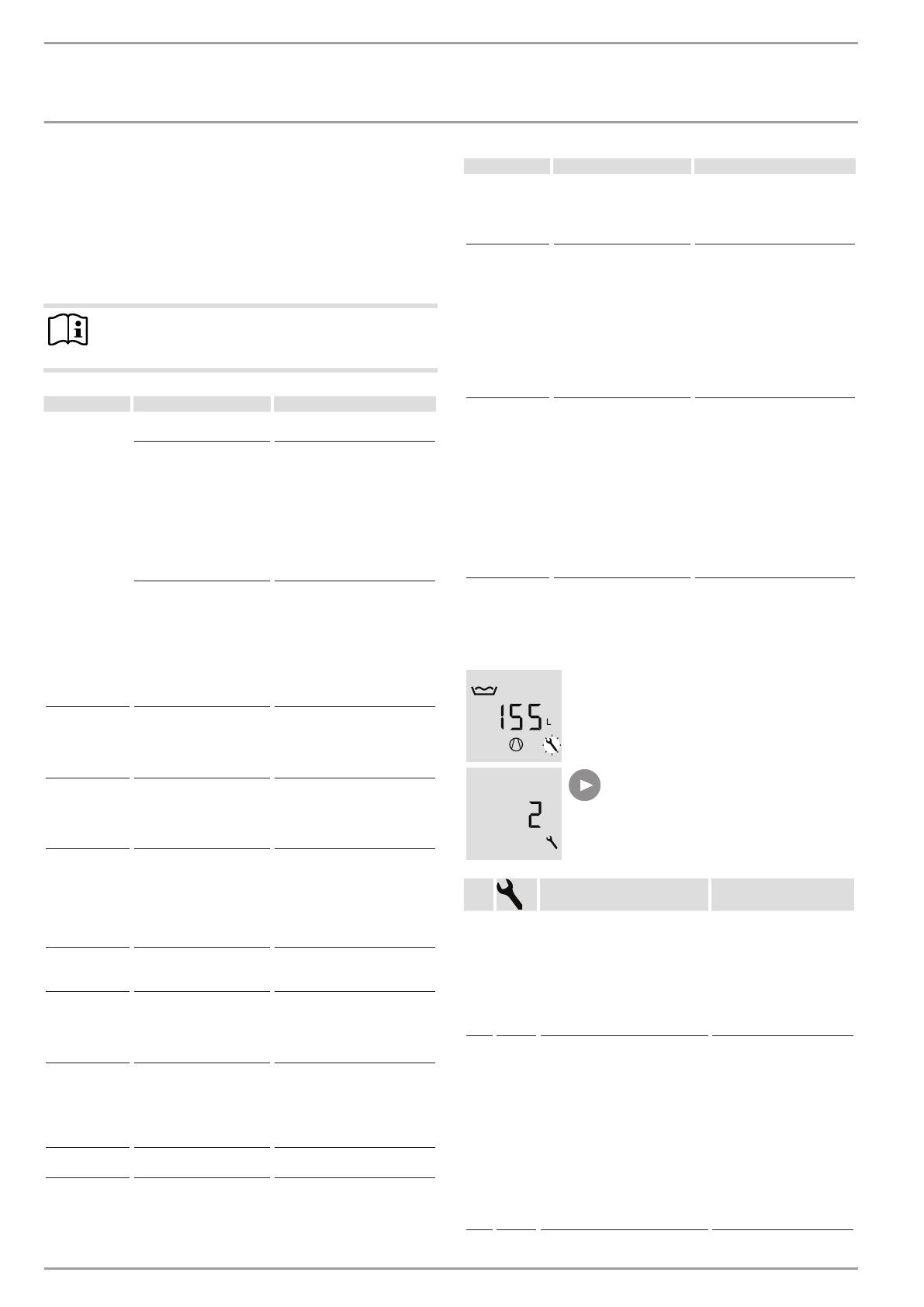
OPERATION
Troubleshooting
12 | SHP-A 220-300 Plus www.stiebel-eltron.com
Check the taps regularly. Limescale deposits at the tap out-
lets can be removed using commercially available descaling
agents.
Regularly activate the safety valve to prevent it from becom-
ing blocked, e.g. by limescale deposits.
6. Troubleshooting
Note
At various points, reference is made to the appliance pa-
rameters. See chapter "Specification".
Fault Cause Remedy
No hot water is
available.
No power at the appliance. Check that the appliance is con-
nected to the power supply.
A fuse/MCB in the fuse box
has blown/tripped.
Check whether the fuses/MCBs
in your fuse box have blown/
tripped. If required, disconnect
the appliance from the power
supply and replace the fuses/
reset the MCBs. Contact your
qualified contractor if the fuse/
MCB blows/trips again after the
appliance is re-connected to the
power supply.
The appliance output data
are calculated according to
standard, using the intake
temperature specified in
the data table. Below this
temperature the appliance
efficiency and output de-
crease. The heat-up time is
extended.
No action required.
The safety valve
of the DHW
cylinder is drip-
ping.
The appliance cylinder is
at mains water pressure.
During heat-up, expansion
water may drip from the
safety valve.
Notify a qualified contractor if
water continues to drip when
heat-up has been completed.
The condensate
drain drips.
The surface temperature
of the evaporator is lower
than the dew point tem-
perature of the ambient
air. Condensate forms.
The amount of condensate de-
pends on the humidity level of
the ambient air.
The room tem-
perature drops.
operation of the appliance
can cause the room tem-
perature to fall by 1 to 3°C,
as the appliance extracts
energy from the air.
If the room temperature falls
by more than 5°C, check the
room size (see the "Specifi-
cation/Data table" chapter).
Supplying energy by opening
a door to another room will
remedy this.
High power con-
sumption
The lower the intake tem-
perature, the lower the
heat pump efficiency.
Where possible, avoid high set
temperatures and the use of
rapid heat-up.
Service/fault
symbol is per-
manently on.
See the "Fault codes"
chapter.
Notify a qualified contractor. A
permanently lit "service/fault"
symbol indicates that a fault has
occurred, but the heat pump is
heating nevertheless.
Service/fault
symbol flashes
and the water
does not heat
up.
See the "Fault codes"
chapter.
It is imperative that you notify a
qualified contractor quickly. A
flashing "service/fault" symbol
indicates that a fault has oc-
curred and the heat pump is no
longer heating.
Defrost symbol
is shown.
The appliance is in defrost
mode.
No action required.
Fault Cause Remedy
The heat pump
symbol is flash-
ing.
There is a heat demand,
but the compressor is
locked out.
No action required. The com-
pressor restarts automatically
after the compressor lockout
time has elapsed. The symbol
stops flashing automatically.
The electric
emergency/
booster heater
symbol is flash-
ing.
A temperature controller
has switched off the elec-
tric emergency/booster
heater during rapid heat-
up.
No action required. The ap-
pliance continues the quick
heat-up process using the heat
pump. The symbol stops flash-
ing when the controller re-en-
ables the electric emergency/
booster heater. The symbol
goes out when the temperature
throughout the DHW cylinder
reaches the set rapid heat-up
temperature.
The electric
emergency/
booster heater
symbol is illu-
minated but the
electric emer-
gency/booster
heater is not
operational.
The electric emergency/
booster heater lights up
when there is a demand.
The internal controller of
the electric emergency/
booster heater may have
ended electric heating. A
possible cause may be a
fault in the electric emer-
gency/booster heater. A
possible cause may be that
the high limit safety cut-
out has responded.
Have a qualified contractor
check whether the controller of
the electric emergency/booster
heater is set correctly. The
controller must be turned fully
anti-clockwise. Have a qualified
contractor check the high limit
safety cut-out.
Fault code
You can call up a fault code if the Service/fault symbol is flashing
or continuously lit on the display.
Keep pressing "Menu" until the fault code
appears.
Fault description Remedy
2
perma-
nently
on
The sensor at the cylinder top is
faulty. The actual temperature
display switches from the cyl-
inder top sensor to the integral
sensor. The appliance continues
to heat without any loss of com-
fort. The mixed water volume
cannot be calculated and is dis-
played as "- -".
Notify a qualified contrac-
tor.
4
perma-
nently
on
The integral sensor is faulty.
In the event of a faulty integral
sensor, the integral sensor is
set to the value of the sensor at
the cylinder top, and amount of
mixed water is calculated using
this value. The appliance contin-
ues to heat with a reduced start
hysteresis.
A mixed water volume is still cal-
culated, based on the assumption
that the cylinder top temperature
is reached throughout the DHW
cylinder.
Notify a qualified contrac-
tor.