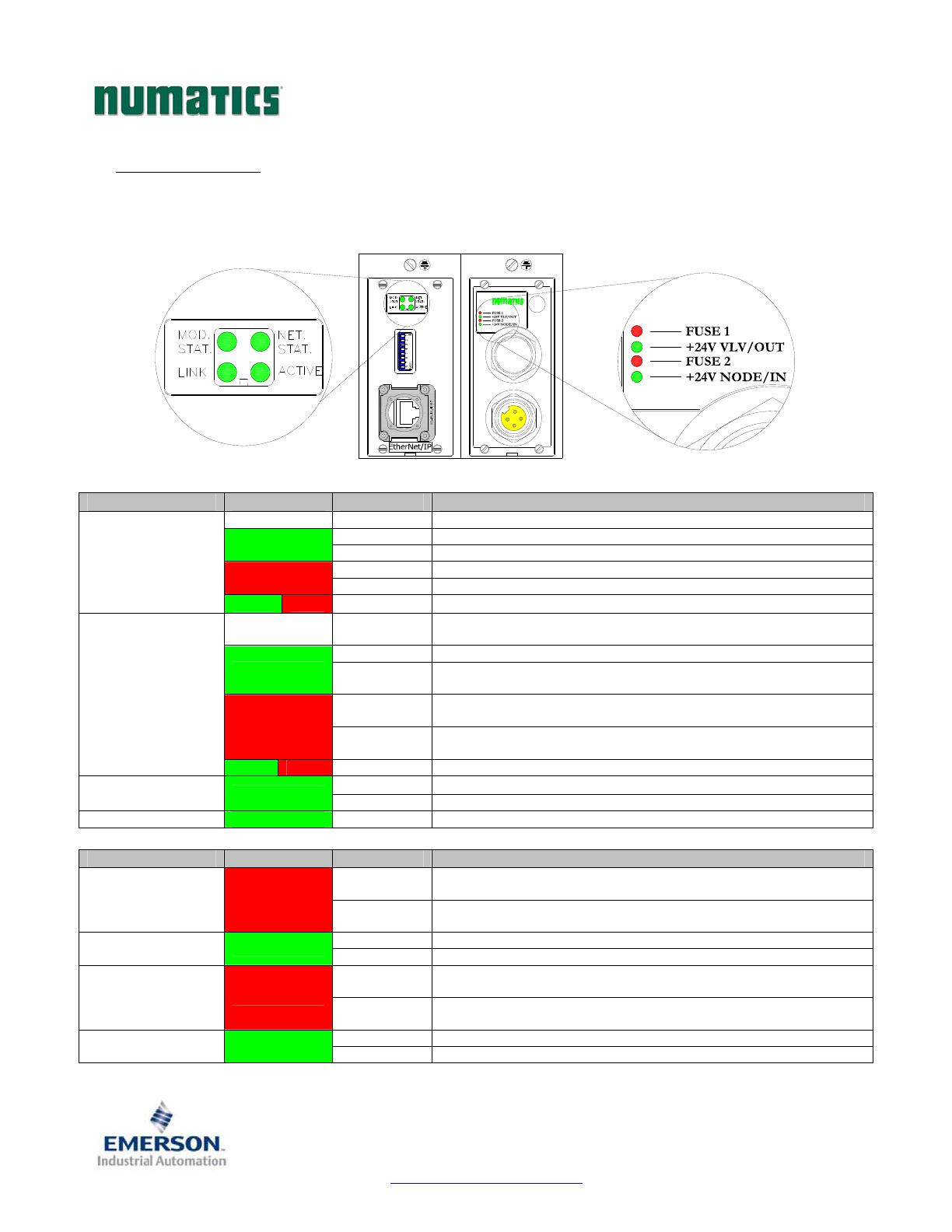
G2-2 Series EtherNet/IP
TM
and Modbus TCP
Quick Start Manual
Page 13
3835056
DG22ENQS2-0 1/07
Subject to change without notice
www.numatics.com/fieldbus
12) LED Functions
Upon power up, the LEDs indicate the status of the unit. The Power Module of the G2-2 EtherNet/IP
TM
and
Modbus TCP node has four LEDs; two for internal fuse integrity and two for Aux. Power status. The
Communication module also has four status LEDs which are described below.
Communication Module
LED Name Color Status Description
Off OFF No power applied to module
ON Device operational. The module is operating correctly.
Green
FLASHING Standby. The module has not been configured.
ON Major fault. A major internal error has been detected.
Red
FLASHING Minor fault. A minor recoverable fault has been detected.
MOD. STAT.
(Module Status)
Green Red FLASHING Self –test. The module is performing a power on self-test.
Off OFF
IP address has been not been assigned to node. Or no power applied to
unit.
ON Connected. The module has established an EtherNet/IP connection.
Green
FLASHING
No connection. There are no EtherNet/IP connections established to
the module.
ON
Duplicate IP address. The module has detected that its IP address is
already being used elsewhere on the network
Red
FLASHING
EtherNet/IP connection has timed out. One or more of the
connections for which this module is the target has timed out.
NET. STAT.
(Network Status)
Green Red FLASHING Self –test. The module is performing a power on self-test.
OFF No Ethernet connection is detected
LINK Green
ON The module is connected to an EtherNet network
ACTIVE Green FLASHING The LED flashes each time a packet is received or transmitted.
Power Module
LED Name Color Status Description
OFF
Internal fuse
F1
is OK (valid only when power is applied to
+24V
VLV / OUT
pin on Aux. Power connector).
FUSE 1 Red
ON
Internal fuse
F1
is open; No power is internally provided to valves or
outputs. Communication NOT affected.
OFF No DC Power present at
+24V
VLV / OUT
pin on Aux. Power connector.
+24V VLV/OUT Green
ON DC Power applied to
+24V
VLV / OUT
pin on Aux. Power Connector.
OFF
Internal fuse
F2
is OK (valid only when power is applied to
+24V
NODE / IN
pin on Aux. Power connector.
FUSE 2 Red
ON
Internal fuse
F2
is open; No power is internally provided to node
electronics or inputs. Communication Node will not function.
OFF No DC Power present at
+24V
NODE / IN
pin on Aux. Power connector.
+24V NODE/IN Green
ON DC Power applied to
+24V
NODE / IN
pin on Aux. Power connector.