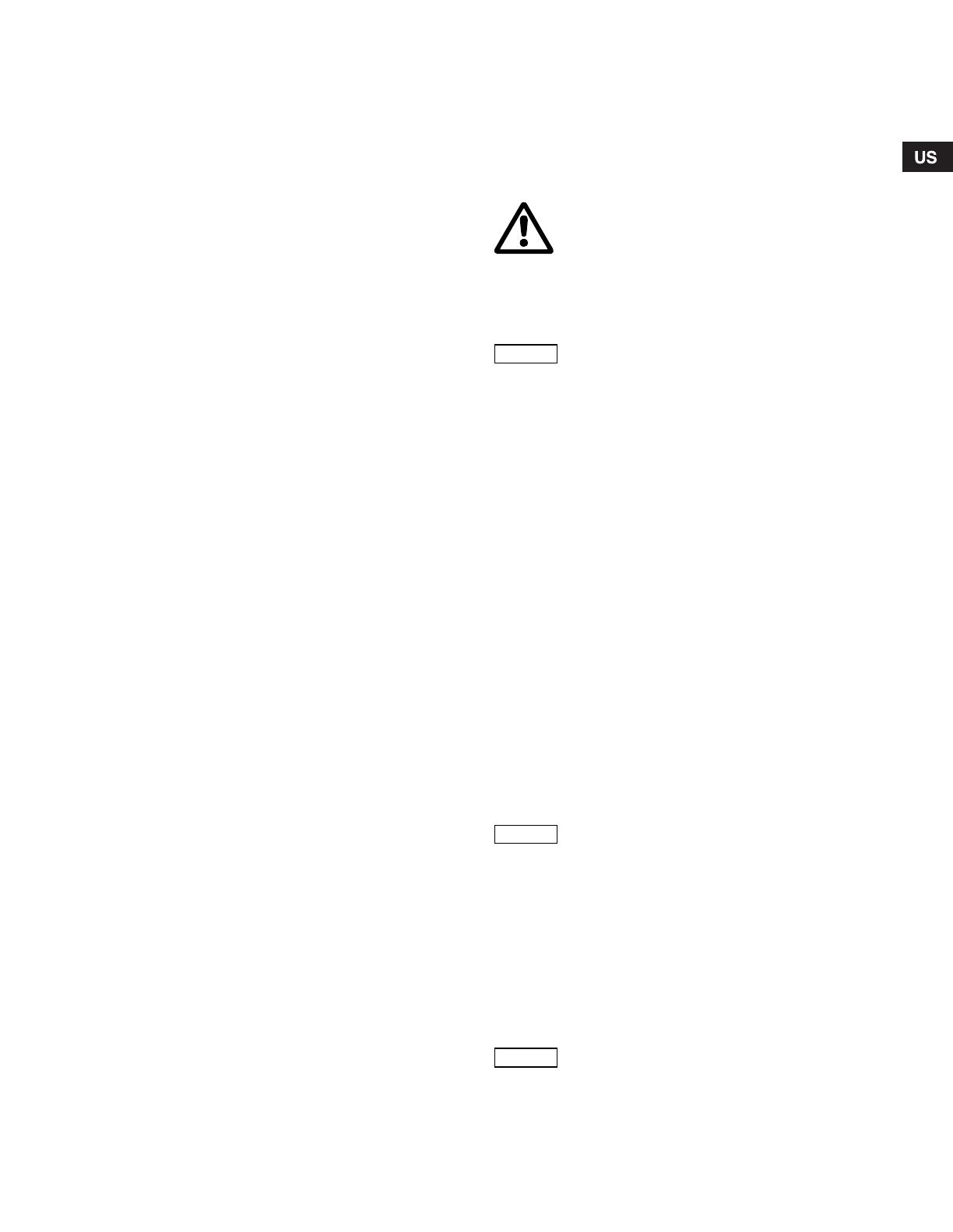
13
Tighten the screws to the correct torque.
Remove the plastic shaft seal spacer, and hang it on the inside
of the coupling guard.
CR, CRN 32, 45, 64 and 90 H
Place the plastic adjustment fork under the cartridge seal
collar.
Fit the coupling on the shaft so that the top of the pump shaft
is flush with the bottom of the clearance chamber in the
coupling.
Lubricate the coupling screws with an anti-seize and
lubricating compound.
Tighten the coupling screws (finger-tight) while keeping the
coupling separation equal on both sides and the motor shaft
keyway centered in the coupling half.
When the screws are tight enough to keep the couplings in
place, then tighten the screws diagonally and evenly.
Tighten the coupling screws to 62 ft-lbs (84 Nm).
Remove the adjustment fork from under the cartridge seal
collar, and replace it to the storage location.
7. Check to see that the gaps between the coupling halves are
equal. Loosen and readjust, if necessary.
8. Be certain the pump shaft can be rotated by hand. If the shaft
cannot be rotated or it binds, disassemble and check for
misalignment.
9. Prime the pump.
10.Follow the wiring diagram on the motor nameplate for the
correct motor wiring combination which matches your supply
voltage. Once this has been confirmed, reconnect the power
supply wiring to the motor.
11.Check the direction of rotation by bump-starting the motor.
Rotation must be left to right (counter-clockwise) when looking
directly at the coupling from the motor end.
12.Switch off the power supply, and refit the coupling guards.
After the coupling guards have been installed, the power
supply can be switched on again.
9. Electrical connection
The electrical connection should be carried out by an authorized
electrician in accordance with local regulations.
Field wiring
Wire sizes should be based on the current-carrying properties of
a conductor as required by the latest edition of the National
Electrical Code or local regulations. Direct on line (DOL) starting
is approved due to the extremely fast run-up time of the motor
and the low moment of inertia of the pump and motor. If DOL
starting is not acceptable and reduced starting current is required,
an autotransformer, resistance starter or soft starter should be
used. It is suggested that a fused disconnect be used for each
pump where service and standby pumps are installed.
Recommendation
We recommend the use of flexible conduit. Flexible conduit
allows movement of the motor on the base plate rails if service is
required.
The operating voltage and frequency are marked on the motor
nameplate. Make sure that the motor is suitable for the power
supply on which it will be used and the motor terminal connection
is correct. You will find a wiring diagram in the terminal box.
9.1 Single-phase motors
With the exception of 10 hp motors which require external
protection, single-phase motors for CR pumps provided by
Grundfos are multi-voltage, squirrel-cage induction motors with
built-in thermal protection.
9.2 Three-phase motors
CR pumps with three-phase motors must be used with the proper
size and type of motor starter to ensure the motor is protected
against damage from low voltage, phase failure, current
imbalance and overloads. A properly sized starter with manual
reset and ambient-compensated extra quick trip in all three legs
should be used. The overload should be sized and adjusted to
the service factor current rating of the motor.
Under no circumstances should the overloads be set to a higher
value than the service factor current shown on the motor
nameplate. This will void the warranty. Overloads for
autotransformers and resistance starters should be sized in
accordance with the recommendations of the manufacturer.
Three-phase MLE motors (CRE-H pumps) require only fuses as a
circuit breaker. They do not require a motor starter. Check for
phase imbalance.
9.3 Frequency converter operation
Motors supplied by Grundfos
All three-phase motors supplied by Grundfos can be connected to
a frequency converter. The frequency converter must be
configured for variable-torque operation.
Depending on the frequency converter type, this may cause
increased acoustic noise from the motor. Furthermore, it may
cause the motor to be exposed to detrimental voltage peaks.
Warning
Before removing the terminal box cover and
before removing/dismantling the pump, make
sure that the power supply has been switched off.
The pump must be connected to the power
supply using a supply disconnecting device.
The safe operation of this pump requires that it
be grounded in accordance with the National
Electrical Code and local governing codes or
regulations. Connect the ground wire to the
grounding screw in the terminal box and then to
the acceptable grounding point.
The need for an emergency stop should be
decided by the user.
Standard allowable phase imbalance difference
is 5 % (voltage and current).
Grundfos motors, types ML 71 and ML 80, for
supply voltages up to and including 460 V are
without phase insulation (see motor nameplate).
They must be protected against voltage peaks
above 650 V (peak value) between the supply
terminals.