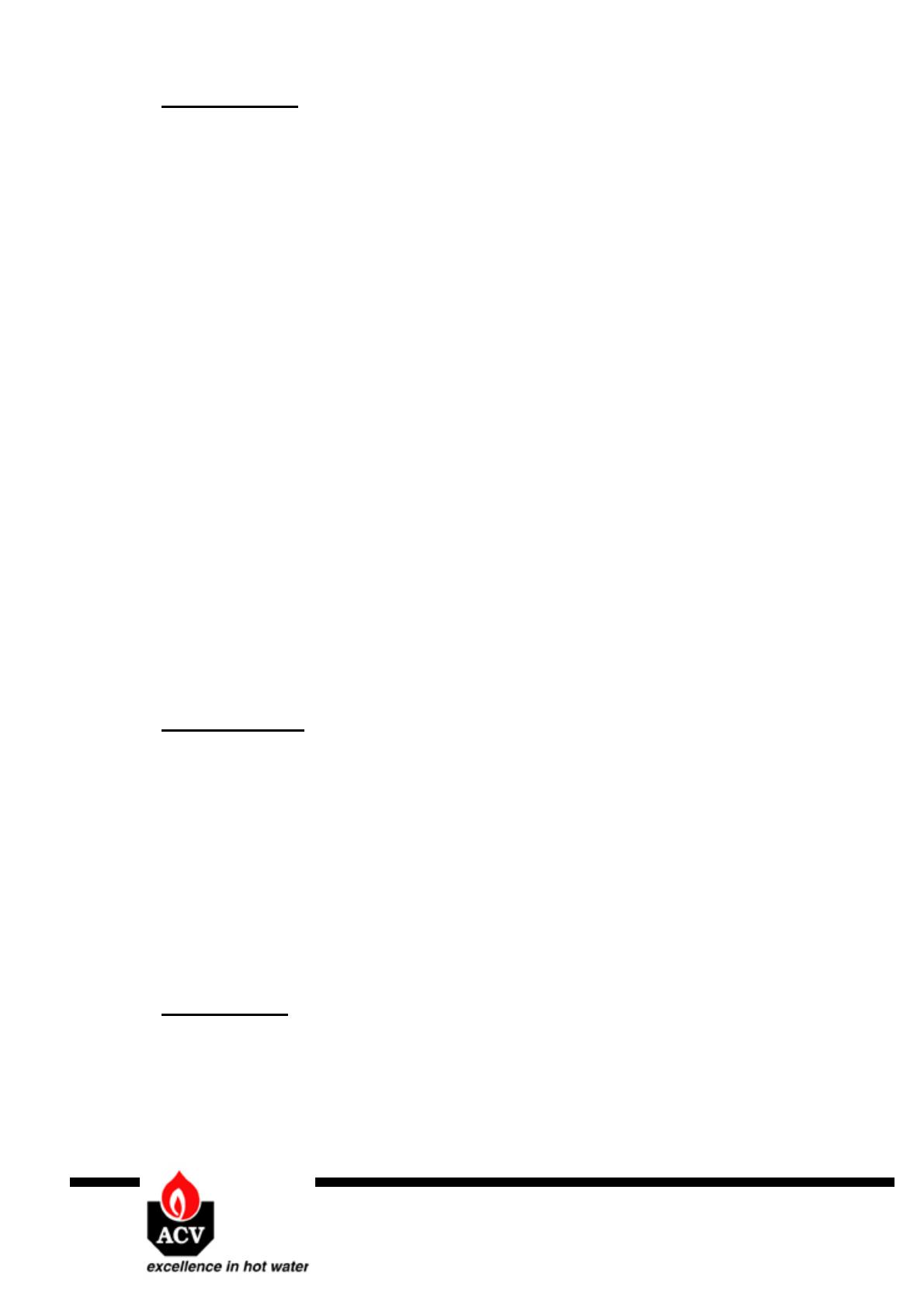
66403100 06/2005 Page 12
11. INSTALLATION
WARNING !!! Size the flowrate in the hydraulic circuit to ensure a 10°C maximum ∆t.
GENERAL SAFETY RULES :
The boiler must be installed by an registered company.
After the installation work, the installer must issue a statement of compliance, declaring that the
installation has been carried out in a workmanlike manner, as defined for by the applicable
regulations.
Make sure that the wiring system and the power input lines are designed and installed by
skilled engineers in compliance with the applicable regulations.
IMPORTANT
As far as the power input to the boiler is concerned, the installation must comply with IEC 364
standards and other provisions concerning installation conditions.
For protection against electrical hazard, it is always recommended to install a differential
cut-out device (Ground Fault Isolator) on the power supply circuit, upstream of the boiler.
For protection against overheating, it is advisable to place a positive safety electric power
cut-out, controlled by the boiler safety thermostat.
BOILER ROOM
Electric boilers must be installed in boiler rooms complying with the technical standards
and applicable regulations.
The appliance should never be installed outdoors, because it has not been designed for
and is not equipped with automatic defrosting systems.
If possible, install the boiler above the ground level, to reduce the risk of flooding the
electrical components.
INSTALLATION ON AN EXISTING HEATING CIRCUIT
If you connect the boiler on an existing heating circuit, please carefully check that:
The pump is powerful enough and in good shape.
The boiler room is clean and ventilated.
The expansion vessel is sized to absorb the heat expansion of the complete heating circuit.
12. COMMISSIONING
PREPARATION BEFORE COMMISSIONING
Before powering up the boiler and performing the functional tests, make sure that:
the hydraulic circuit valves are opened;
the electric power is available;
the pressure of the (cold) hydraulic circuit is higher than 1 bar and lower than the maximum
working pressure of the appliance;
the hydraulic circuits have been througoutly purged: pump the heating fluid through the
hydraulic circuit and purge the air from the installation
the electric connection to the power mains and the external control connection have
been carefully carried out;
the grounding connections have been installed as specified by local regulations
13. MAINTENANCE
Check on a regular base that the heating circuit pressure is higher than 1 bar.
If the pressure drops below 1 bar, please contact your installer
DON'T SWAP THE PHASE / NEUTRAL CONNECTIONS.
GROUNDING CONNECTION IS MANDATORY