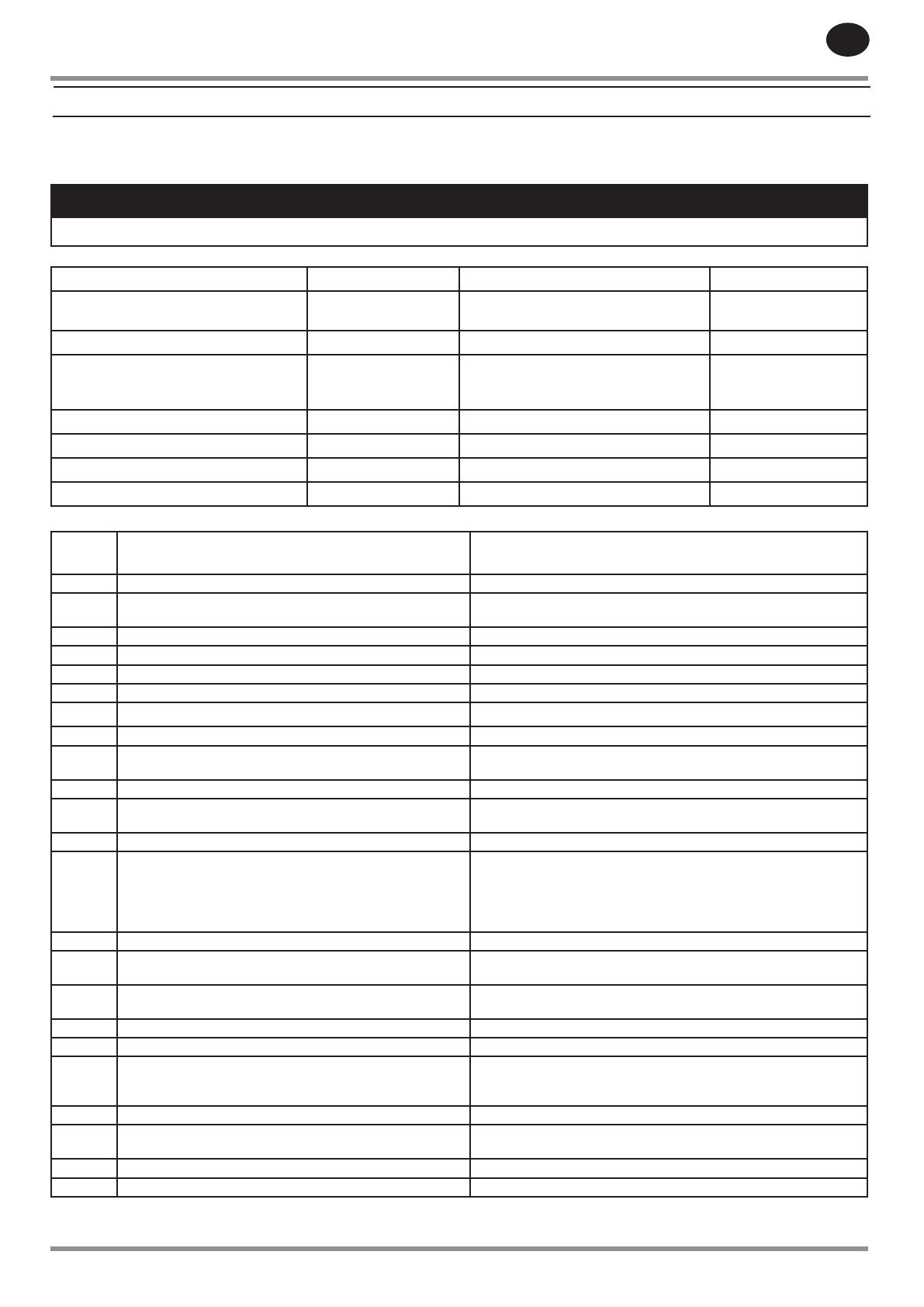
22204911 Rev. D EN-11
EN
This section provides a list of the more frequently encountered malfunctions, their causes and corrective actions. Some
corrective actions can be performed by the operator or maintenance personnel, and others may require the assistance of a
qualied Ingersoll Rand technician or your dealer.
NOTICE
Please see engine owner’s manual for additional engine troubleshooting.
PROBLEM CHECK POINT PROBLEM CHECK POINT
Abnormal piston, ring or cylinder
wear 4, 7, 8, 14, 19, 26 High oil consumption 1, 4, 8, 13, 14, 15, 17, 22
Air delivery drops 1, 5, 6, 11, 13, 14, 20 Knocking or rattling 2, 11, 12, 14, 15, 16
Unit does not come up to speed 2, 6, 11, 16 Moisture in crankcase or “milky”
appearance in petroleum lubricant
or rusting in cylinders 8, 9
Unit is slow to come up to speed 6, 18, 21 Oil in discharge air (oil pumping) 4, 8, 13, 14, 22, 23
Unit runs excessively hot 3, 10, 11 Oil leakage from shaft seal 17
Excessive noise during operation 2, 6, 7, 11, 12, 16, 18 Safety/relief valve “pops” 1, 11, 20
Excessive starting and stopping 5, 18, 23
CHECK
POINTS POSSIBLE CAUSE POSSIBLE SOLUTION
1 Clogged or dirty inlet and/or discharge line lter. Clean or replace.
2Loose beltwheel or engine pulley, excessive end play
in engine shaft or loose drive belts. Check beltwheel, engine pulley, crankshaft, drive belt
tension and alignment. Repair or replace as required.
3 Inadequate ventilation around beltwheel. Relocate unit for better air ow.
4 Lubricant viscosity too low. Drain existing lubricant and rell with proper lubricant.
5 Air leaks in air discharge piping. Check tubing and connections.
6 Lubricant viscosity too high. Drain existing lubricant and rell with proper lubricant.
7 Lubricant level too low Add lubricant to crankcase to proper level.
8 Detergent type lubricant being used. Drain existing lubricant and rell with proper lubricant.
9Extremely light duty cycles.
Unit located in damp or humid location. Run unit for longer duty cycles.
Relocate unit.
10 Drive belts too tight or misaligned. Adjust belts to proper tension and alignment.
11 Compressor valves leaky, broken, carbonized or
loose. Inspect valves. Clean or replace as required.
12 Carbon build-up on top of piston(s). Clean piston(s). Repair or replace as required.
13
Piston rings damaged or worn (broken, rough or
scratched).
Excessive end gap or side clearance.
Piston rings not seated, are stuck in grooves or end
gaps not staggered.
Adjust piston rings.
14 Cylinder(s) or piston(s) scratched, worn or scored. Repair or replace as required.
15 Connecting rod, piston pin or crank pin bearings
worn or scored. Inspect all. Repair or replace as required.
16 Defective ball bearing on crankshaft or motor shaft. Inspect bearings and replace crankshaft assembly if
required.
17 Crankshaft seal worn or crankshaft scored. Replace seal or crankshaft assembly.
18 Leaking check valve or check valve seat blown down. Replace check valve.
19 Extremely dusty atmosphere. Install remote air inlet piping and route to source of cleaner
air.
Install more eective ltration.
20 Defective safety/relief valve. Replace safety/relief valve.
21 Ambient temperature too low. Relocate to warmer environment.
Convert to synthetic lubricant.
22 Worn cylinder nish. Deglaze cylinder with 180 grit ex-hone.
23 Excessive condensate in receiver tank. Drain receiver tank with manual drain valve.
TROUBLESHOOTING
RELEASED 16/Apr/2018 18:50:16 GMT