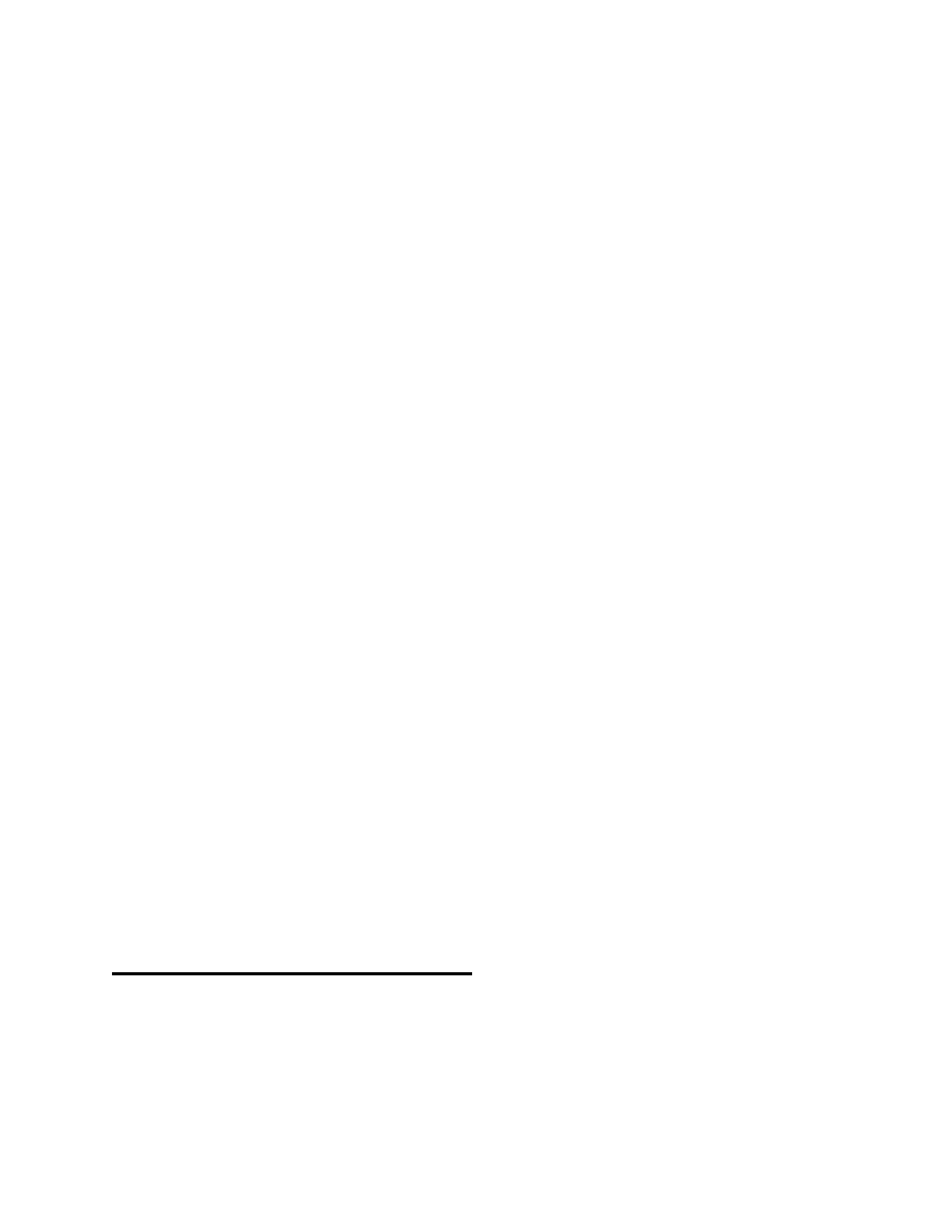
10
Cold Water Electric • Rev. 17/10/2016
3. Attach water source to water inlet located on pump. The water source must be attached with
a good quality standard garden type hose (1/2” minimum is required). Connect male fitting into
the female pump inlet fitting. Make sure that the inlet screen/filter is intact and fitted correctly.
Turn on water source. WATER MUST BE IN SUFFICIENT SUPPLY, AND PRESSURE
MUST BE BETWEEN 20 –60 PSI TO ENSURE PROPER AND SAFE OPERATION. Specific
attention should be given if using a well water supply. Ensure water is flowing from end nozzle
with trigger gun pulled. Deplete system of all air.
4. Start electric motor. Turn PUMP switch to ‘ON’. PUMP switch is located on the frame
beside the motor, or for auto stop/start systems, PUMP switch is located on the electrical box.
5. Pressure adjustment - The pressure regulator (unloader) is located on the pump (see
diagram). It controls pressure being generated by the pressure washer. This regulator may be
adjusted to the desired pressure by turning the adjustment knob. Turning the adjustment knob
clockwise will increase the pressure. NEVER OPERATE SYSTEM AT A HIGHER PSI
THAN THE MAXIMUM RATING. This machine has been adjusted to operate at a specific
maximum pressure as per the machine specifications. Pressure may be reduced for lighter use by
turning the Pressure Regulator/Unloader counter clockwise. If continuing to turn the unloader
clockwise does not increase the pressure, then this implies the maximum has been reached for
the system. Any further turning of the unloader will cause the pressure to spike when the wand
trigger is released, resulting in possible damage to the machine. To avoid this effect, loosen the
unloader (counter-clockwise) until the pressure just starts to drop (see pump head pressure
gauge) and until it no longer exceeds the maximum pressure rating for the machine.
6. You are now ready to start the cleaning operation - Pull trigger on the pressure wand
assembly to start cleaning. To stop the pressurized water, release the trigger. DO NOT
LEAVE UNIT RUNNING WHEN NOT IN USE.
7. To stop Operation. Turn PUMP switch to ‘OFF’. Squeeze and release trigger after shutting
off to relieve system of pressure.
8. Prior to storage – Inspect pressure washer for any damage or required maintenance. If your
machine is to be exposed to cold weather, please refer to winter pump instructions found in this
manual. If possible, do not allow unit to remain outside in the elements.
9. Warning – If unit is left running while not in use, pump damage may occur. Do not leave unit
running while not in use!
CHEMICAL APPLICATION
Downstream Chemical Injection: Standard (Direct Drive Units)
High Pressure Soap (Belt and Flange Driven Units) (Optional)