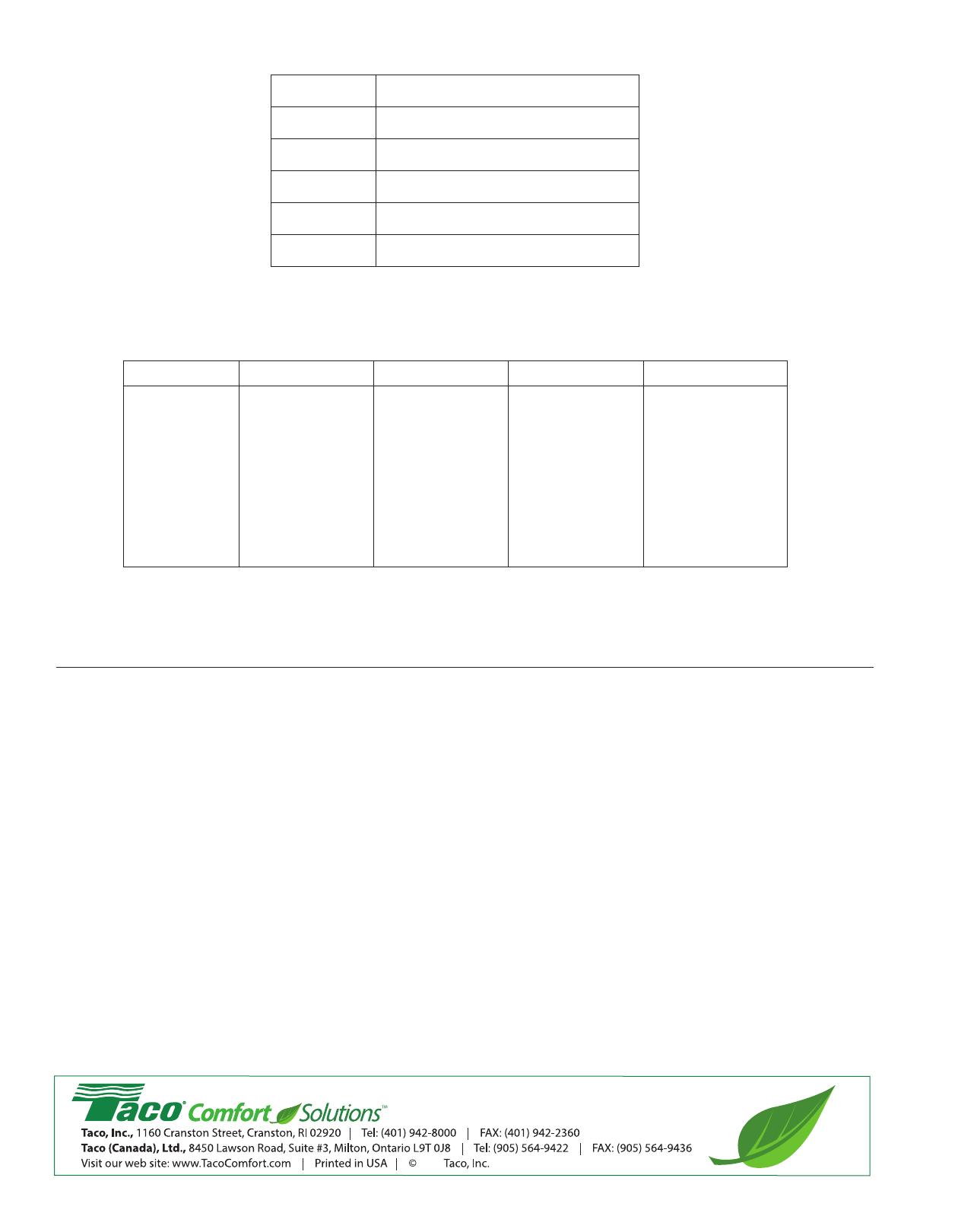
LIMITED WARRANTY STATEMENT
Taco, Inc. will repair or replace without charge (at
the company’s option) any Taco High-Efficiency
circulator or circulator part which is proven defec-
tive under normal use within three (3) years from
the date of manufacture.
In order to obtain service under this warranty, it
is the responsibility of the purchaser to promptly
notify the local Taco stocking distributor or Taco
in writing and promptly deliver the subject product
or part, delivery prepaid, to the stocking distribu-
tor. For assistance on warranty returns, the pur-
chaser may either contact the local Taco stock-
ing distributor or Taco. If the subject product or
part contains no defect as covered in this war-
ranty, the purchaser will be billed for parts and
labor charges in effect at time of factory exami-
nation and repair.
Any Taco product or part not installed or operated
in conformity with Taco instructions or which has
been subject to misuse, misapplication, the addi-
tion of petroleum-based fluids or certain chemi-
cal additives to the systems, or other abuse, will
not be covered by this warranty.
If in doubt as to whether a particular substance
is suitable for use with a Taco product or part, or
for any application restrictions, consult the
applicable Taco instruction sheets or contact
Taco at (401-942-8000).
Taco reserves the right to provide replacement
products and parts which are substantially similar
in design and functionally equivalent to the
defective product or part. Taco reserves the right
to make changes in details of design, construc-
tion, or arrangement of materials of its products
without notification.
TACO OFFERS THIS WARRANTY IN LIEU OF
ALL OTHER EXPRESS WARRANTIES. ANY
WARRANTY IMPLIED BY LAW INCLUDING
WARRANTIES OF MERCHANTABILITY OR
FITNESS IS IN EFFECT ONLY FOR THE DURA-
TION OF THE EXPRESS WARRANTY SET
FORTH IN THE FIRST PARAGRAPH ABOVE.
THE ABOVE WARRANTIES ARE IN LIEU OF
ALL OTHER WARRANTIES, EXPRESS OR
STATUTORY, OR ANY OTHER WARRANTY
OBLIGATION ON THE PART OF TACO.
TACO WILL NOT BE LIABLE FOR ANY SPE-
CIAL, INCIDENTAL, INDIRECT OR CONSE-
QUENTIAL DAMAGES RESULTING FROM THE
USE OF ITS PRODUCTS OR ANY INCIDENTAL
COSTS OF REMOVING OR REPLACING
DEFECTIVE PRODUCTS.
This warranty gives the purchaser specific rights,
and the purchaser may have other rights which
vary from state to state. Some states do not
allow limitations on how long an implied warranty
lasts or on the exclusion of incidental or conse-
quential damages, so these limitations or exclu-
sions may not apply to you.
A Taco Family Company
2016
Taco Grundfos Armstrong Xylem/B & G Wilo
005
006
007
008
00R
00R 3-speed
0015 3-speed
UP 15-10 F
UP 15-10 FR
UP 15-42 F
UP 15-42 FR
UPS 15-42 F
UPS 15-58 FC
UPS 15-58 FRC
ALPHA 15-55F
ALPHA 15-55FR
Astro 230CI
Astro 230CI-R
Astro 250CI
Astro 250CI-R
Astro 20
Astro 25
Astro 30
Astro 30-3
Astro 50-3
Compass 20-20
ecocirc 19-14 auto
ecocirc 19-14 vario
NRF-22
NRF-25
NRF-9F/LW
Star S 16F
Star S 16FX
Star S 21RFC
Star S 21FX
Star S 21F
Stratos ECO 16 RFC
0
0
1
5
e
3
™
Pu
m
p Re
pl
a
c
e
m
e
n
t C
r
os
s
Re
f
e
r
e
n
c
e
198-213 RP Casing O-ring
198-214 RP Wiring plug connector (green)
198-215 RP Terminal box cover (black)
198-217 RP Terminal box cover screws (5 per bag)
0010-025 RP Integral Flow Check (IFC®)
007-007 RP Flange gasket set
Replacement Parts List