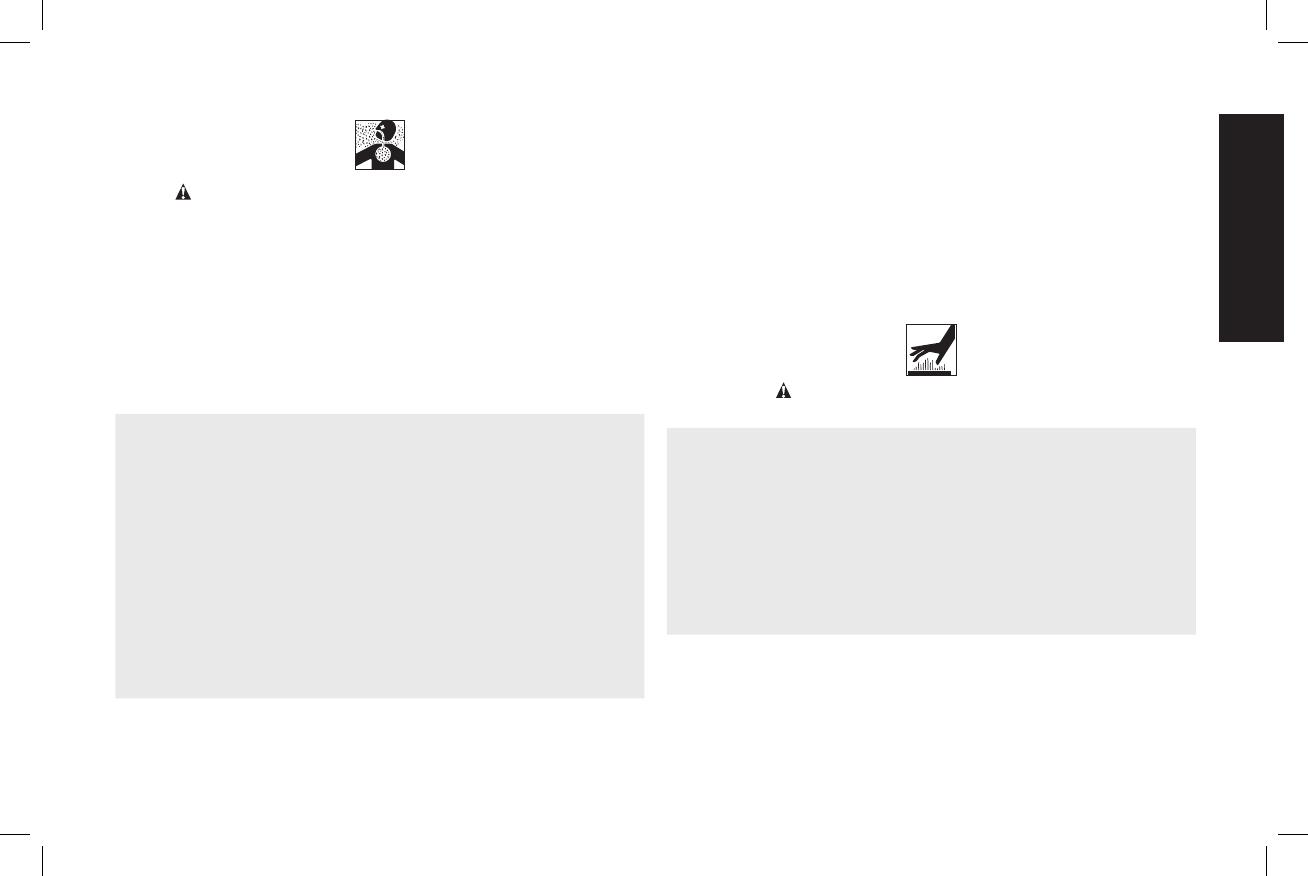
7
English
DANGER: RISK TO BREATHING (ASPHYXIATION)
WHAT CAN HAPPEN HOW TO PREVENT IT
• Breathing ex haust fumes
will cause se ri ous injury
or death! En gine exhaust
con tains carbon mon ox ide,
an odorless and deadly gas.
• Always operate air compressor
outside in a clean, well
ventilated area. Avoid enclosed
areas such as garages,
basements, storage sheds,
which lack a steady exchange
or air. Keep children, pets
and others away from area of
operation.
• The compressed air directly
from your compressor is not
safe for breathing. The air
stream may contain carbon
monoxide, toxic vapors,
or solid particles from the
air tank. Breathing these
contaminant's can cause
serious injury or death.
• Air obtained directly from the
compressor should never be
used to supply air for human
consumption. In order to use air
produced by this compressor
for breathing, suitable filters and
in-line safety equipment must
be properly installed. In-line
filters and safety equipment
used in conjunction with the
compressor must be capable
of treating air to all applicable
local and federal codes prior to
human consumption.
• Sprayed materials such as
paint, paint solvents, paint
remover, insecticides, weed
killers, may contain harmful
vapors and poisons.
• Work in an area with good
cross ventilation. Read and
follow the safety instructions
provided on the label or safety
data sheets for the materials
you are spraying. Always use
certified safety equipment:
NIOSH/OSHA respiratory
protection designed for use with
your specific application.
WARNING: RISK OF HOT SURFACES
WHAT CAN HAPPEN HOW TO PREVENT IT
• Touching exposed metal such
as the compressor head,
engine head, engine exhaust
or outlet tubes, can result in
serious burns.
• Never touch any exposed
metal parts on compressor
during or immediately after
operation. Compressor will
remain hot for several minutes
after operation
• Do not reach around
protective shrouds or attempt
maintenance until unit has
been allowed to cool.