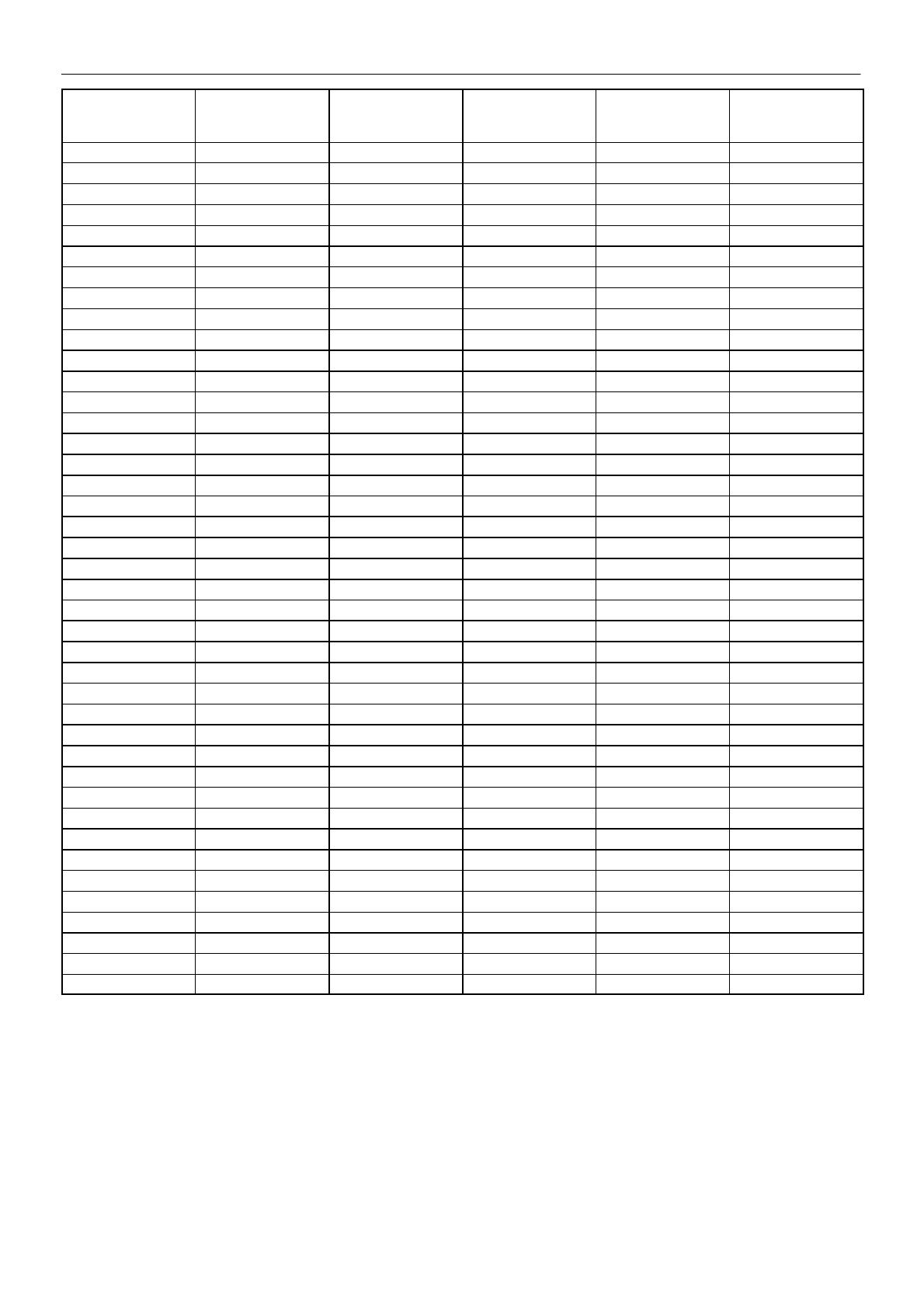
8.0 GENERAL INFORMATION
TS1A–13A
http://air.irco.com
15
Model / Electrical Compressed Air,
m
3
/min (scfm) (1),
(2)
Dryer Pressure
Drop, bar (psi) (1),
(2), (3)
Cooling Air Flow,
m
3
/hr (cfm)
(1), (2), (3)
Nominal Package
Amps (1), (2), (3)
Maximum Package
Amps
TS–1A, 230/1/50 9.0 (319) 0.16 (2.3) 4,200 (2,470) 10.4 12.7
TS–1A, 230/1/60 9.0 (319) 0.16 (2.3) 4,800 (2,820) 10.2 11.8
TS–1A, 230/3/60 7.0 (250) 0.13 (1.8) 5,500 (3,230) 8.5
TS–1A, 460/3/60 7.0 (250) 0.13 (1.8) 3,200 (1,880) 4.4
TS–2A, 230/1/50 14.0 (494) 0.19 (2.8) 4,400 (2,580) 13.3 18.4
TS–2A, 230/1/60 14.0 (494) 0.19 (2.8) 3,700 (2,170) 10.9 17.0
TS–2A, 230/3/60 9.6 (340) 0.20 (2.8) 1,800 (1,050) 8.7
TS–2A, 400/3/50 14.0 (494) 0.19 (2.8) 3,400 (2,000) 4.9 6.9
TS–2A, 460/3/60 9.6 (340) 0.20 (2.8) 1,800 (1,050) 4.8
TS–3A, 230/3/60 13.0 (460) 0.23 (3.2) 5,500 (3,230) 12.5
TS–3A, 380/3/60 15.8 (560) 0.23 (3.4) 4,600 (2,700) 6.1 8.4
TS–3A, 400/3/50 15.8 (560) 0.23 (3.4) 5,400 (3,170) 5.8 8.2
TS–3A, 460/3/60 13.0 (460) 0.23 (3.2) 3,000 (1,760) 6.1
TS–4A, 230/3/60 16.4 (580) 0.24 (3.4) 5,100 (3,000) 13.2
TS–4A, 380/3/60 19.2 (676) 0.28 (4.0) 3,900 (2,290) 8.5 9.5
TS–4A, 400/3/50 19.2 (676) 0.28 (4.0) 6,000 (3,530) 8.0 9.7
TS–4A, 460/3/60 16.4 (580) 0.24 (3.4) 4,800 (2,820) 6.8
TS–5A, 230/3/60 19.2 (680) 0.21 (3.0) 6,200 (3,640) 15.3
TS–5A, 380/3/60 23.4 (827) 0.15 (2.2) 7,300 (4,290) 9.2 10.0
TS–5A, 400/3/50 23.4 (827) 0.15 (2.2) 6,000 (3,530) 8.6 10.9
TS–5A, 460/3/60 19.2 (680) 0.21 (3.0) 6,100 (3,590) 7.7
TS–6A, 380/3/60 28.0 (987) 0.25 (3.6) 7,600 (4,470) 9.8 11.9
TS–6A, 400/3/50 28.0 (987) 0.25 (3.6) 7,500 (4,410) 9.3 12.3
TS–6A, 460/3/60 25.4 (900) 0.18 (2.5) 7,600 (4,470) 10.1
TS–7A, 380/3/60 31.5 (1,113) 0.23 (3.4) 7,600 (4,470) 11.6 14.4
TS–7A, 400/3/50 31.5 (1,113) 0.23 (3.4) 7,500 (4,410) 11.3 14.0
TS–7A, 460/3/60 30.2 (1,070) 0.25 (3.6) 7,700 (4,530) 11.7
TS–8A, 380/3/60 40.2 (1,420) 0.26 (3.7) 10,900 (6,410) 14.5 17.6
TS–8A, 400/3/50 46.5 (1,643) 0.26 (3.7) 10,800 (6,350) 14.4 18.2
TS–8A, 460/3/60 35.6 (1,260) 0.25 (3.6) 14,000 (8,240) 14.5
TS–9A, 380/3/60 51.0 (1,800) 0.30 (4.3) 12,400 (7,290) 16.7 22.6
TS–9A, 400/3/50 51.0 (1,800) 0.30 (4.3) 14,600 (8,590) 15.6 20.0
TS–9A, 460/3/60 43.6 (1,540) 0.35 (5.0) 12,100 (7,120) 17.0
TS–10A, 460/3/60 49.5 (1,750) 0.40 (5.7) 14,900 (8,760) 18.8
TS–10A, 380/3/60 62.4 (2,203) 0.22 (3.2) 16,300 (9,590) 17.8 22.7
TS–10A, 400/3/50 62.4 (2,203) 0.22 (3.2) 18,200 (10,710) 17.2 23.2
TS–11A, 400/3/50 71.5 (2,527) 0.22 (3.2) 20,400 (12,000) 21.1 26.3
TS–11A, 460/3/60 56.6 (2,000) 0.42 (6.0) 17,000 (10,000) 22.7
TS–12A, 400/3/50 80.7 (2,850) 0.21 (3.1) 32,400 (19,060) 27.9 33.0
TS–12A, 460/3/60 63.7 (2,250) 0.43 (6.1) 19,600 (11,530) 23.2
TS–13A, 460/3/60 68.8 (2,430) 0.45 (6.5) 23,100 (13,590) 28.0
(1)
All standard 230v/1/50Hz, 230v/1/60Hz, 380v/3/60Hz, 400v/3/50Hz machines rated at 25_C ambient, 7 barg inlet, 35_C inlet, and 35_C pressure
dew point inlet.
(2)
All standard 230v/3/60Hz, 460v/3/60Hz, and 575v/3/60Hz machines rated at 85_F ambient, 125 psig, 100_F inlet, and 100_F pressure dew point
inlet.
(3)
Data reported at compressed air flow condition stated in table.
(4)
575v data is not specifically published since it is a 460v dryer shipped with a transformer.