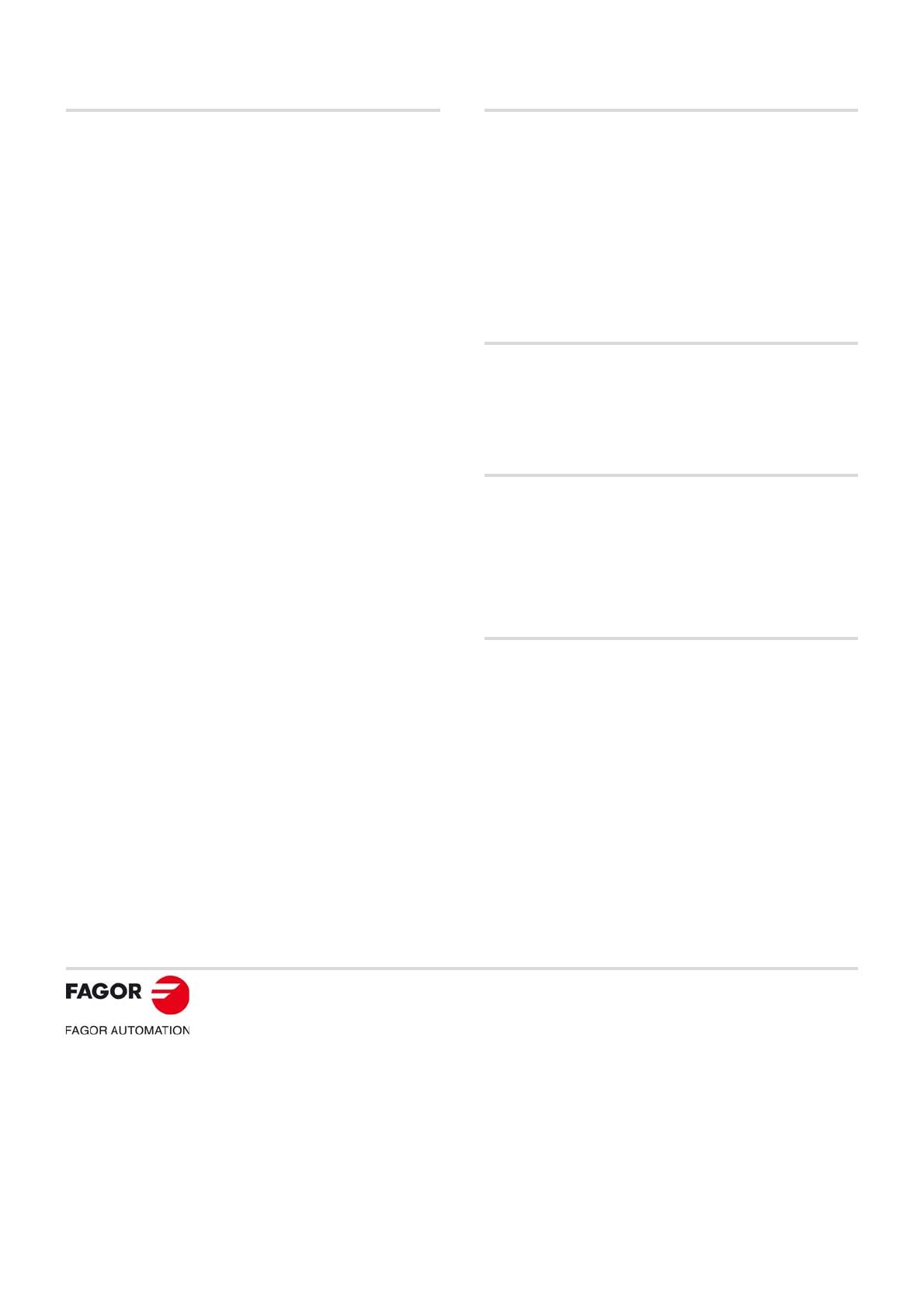
PAGE VIERGE
·2·
Tous droits réservés. La reproduction totale ou partielle de cette documentation
est interdite, de même que sa transmission, transcription, traduction ou son
enregistrement dans un système de récupération de données sans autorisation
expresse de Fagor Automation. Toute copie ou utilisation, totale ou partielle, non
autorisée du logiciel est interdite.
L'information contenue dans ce manuel peut être sujette à des variations dues
à des modifications techniques. Fagor Automation se réserve le droit de modifier
le contenu du manuel sans être tenue à en communiquer les changements.
Toutes les marques enregistrées ou commerciales figurant dans le manuel
appartiennent à leurs propriétaires respectifs. L’utilisation de ces marques par
des tiers pour leurs propres fins peut aller à l’encontre des droits des
propriétaires.
La CNC peut réaliser d’autres fonctions que celles figurant dans la
documentation associée, mais Fagor Automation ne garantit pas la validité de
ces applications. En conséquence, sauf autorisation expresse de Fagor
Automation, toute application de la CNC ne figurant pas dans la documentation
doit être considérée comme "impossible". En tous cas, Fagor Automation
n'assume aucune responsabilité en cas de blessures, dommages physiques ou
matériels, subis ou provoqués par la CNC, si celle-ci est utilisée de manière
différente de celle expliquée dans la documentation concernée.
Le contenu de ce manuel et sa validité pour le produit décrit ont été vérifiés.
Même ainsi, il se peut qu'une erreur involontaire ait été commise et c'est pour
cela que la coïncidence absolue n'est pas garantie. De toute façon, on vérifie
régulièrement l'information contenue dans le document et on effectue les
corrections nécessaires qui seront comprises dans une édition ultérieure. Nous
vous remercions de vos suggestions d’amélioration.
Les exemples décrits dans ce manuel sont orientés à l'apprentissage. Avant de
les utiliser dans des applications industrielles, ils doivent être convenablement
adaptés et il faut s'assurer aussi que les normes de sécurité sont respectées.
SÉCURITÉS DE LA MACHINE
Il est de la responsabilité du fabricant de la machine d'activer les sécurités de
celle-ci dans le but d'éviter des accidents personnels et des dommages à la CNC
ou aux installations qui y sont connectées. Pendant le démarrage et la validation
des paramètres de la CNC, il y a lieu de vérifier l'état des sécurités suivantes.
Si l'une des sécurités est désactivée, la CNC affiche un message
d'avertissement.
• Alarme de mesure pour axes analogiques.
• Limites de logiciel pour axes linéaires analogiques et sercos.
• Surveillance de l'erreur de poursuite pour axes analogiques et sercos (sauf
la broche), aussi bien sur la CNC que sur les asservissements.
• Test de tendance sur les axes analogiques.
FAGOR AUTOMATION n'assume aucune responsabilité en cas d'accidents
personnels et de dommages physiques ou matériels subis ou provoqués par la
CNC s'ils sont dus à l'annulation d'une sécurité quelconque.
PRODUITS À DOUBLE USAGE.
Pour les produits fabriqués par FAGOR AUTOMATION à partir du 1er avril 2014,
chaque produit inclus suivant le Règlement UE 428/2009 dans la liste de produits
à double usage, comprendra dans son identification le texte MDU et aura besoin
de la licence d'exportation suivant la destination.
TRADUCTION DU MANUEL ORIGINAL
Ce manuel est une traduction du manuel original. Ce manuel, ainsi que les
documents découlant de celui-ci, ont été rédigés en espagnol. En cas de
contradictions entre le document en espagnol et ses traductions, la rédaction en
langue espagnole prévaudra. Le manuel original portera la mention "MANUEL
ORIGINAL".
AMPLIATIONS DE HARDWARE
FAGOR AUTOMATION n'assume aucune responsabilité en cas d'accidents
personnels et de dommages physiques ou matériels subis ou provoqués la CNC
s'ils sont dus à la modification du hardware par du personnel non autorisé par
Fagor Automation.
La modification du hardware de la CNC par du personnel non autorisé par Fagor
Automation implique l'annulation de la garantie.
VIRUS INFORMATIQUES
FAGOR AUTOMATION garantit que le logiciel installé ne contient aucun virus
informatique. L'usager est tenu de filtrer l'équipement de tout virus afin d'en
garantir son bon fonctionnement. La présence de virus informatiques dans la
CNC peut provoquer son mauvais fonctionnement.
FAGOR AUTOMATION n'assume aucune responsabilité en cas d'accidents
personnels et de dommages physiques ou matériels subis ou provoqués par la
CNC s'ils sont dus à la présence d'un virus informatique dans le système.
La présence de virus informatiques dans le système implique la perte de la
garantie.