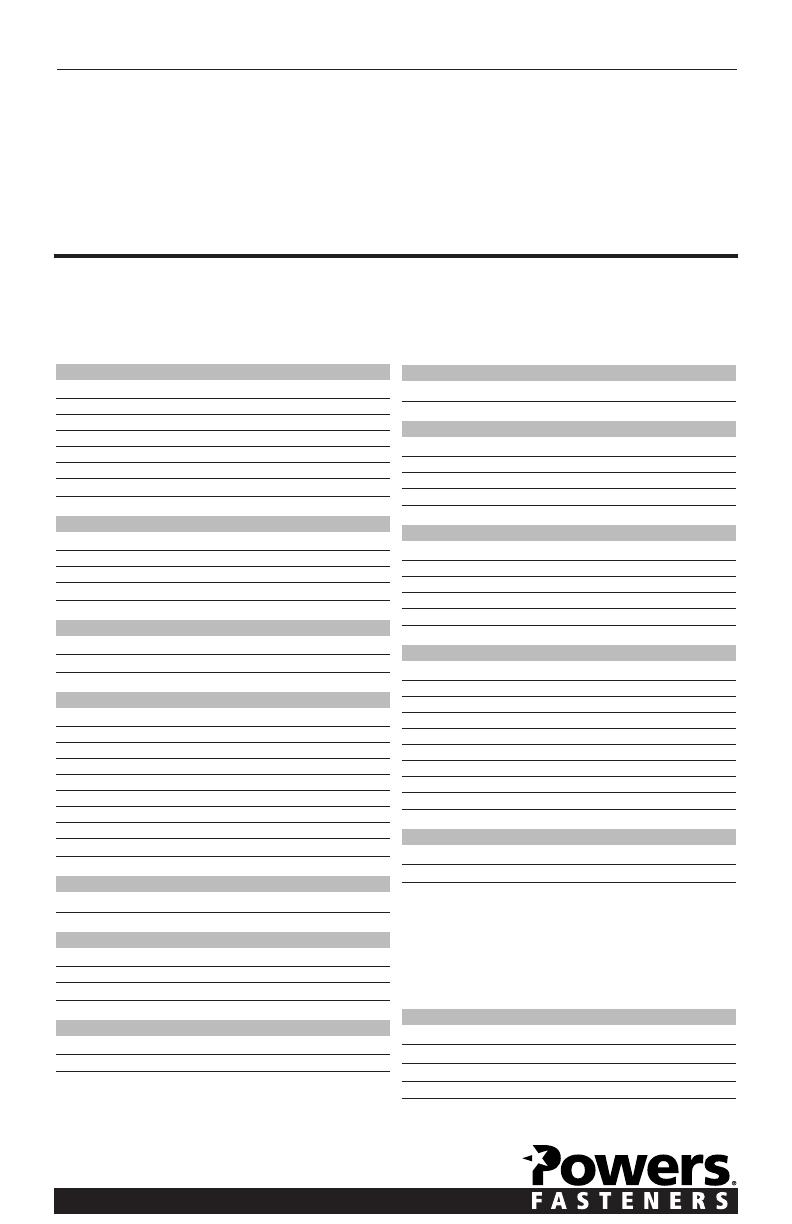
Fastener Selection
Guide
.300 HEAD DIAMETER DRIVE PINS
CAT. STD. STD. HEAD SHANK WT./
NO. SHANK LENGTH BOX CTN. DIA. DIA. 100
50012 1/2"K 100 5000 .300 .143 .5
50016 5/8"K 100 5000 .300 .143 .5
5
0022 3/4" 100 5000 .300 .143 .5
50026 1" 100 5000 .300 .143 .6
50030 1-1/8" 100 1000 .300 .143 .7
50032 1-1/4" 100 1000 .300 .143 .8
50034 1-1/2" 100 1000 .300 .143 .9
.300 HEAD DIAMETER DRIVE PINS WITH TOP HAT
CAT. STD. STD. HEAD SHANK WT./
NO. SHANK LENGTH BOX CTN. DIA. DIA. 100
50136 1/2" K 100 5000 .300 .143 .5
50138 5/8"K 100 5000 .300 .143 .5
50140 3/4" 100 5000 .300 .143 .5
50144 1" 100 5000 .300 .143 .6
.300 HEAD DIAMETER STEP SHANK PINS
CAT. STD. STD. HEAD SHANK WT./
NO. SHANK LENGTH BOX CTN. DIA. DIA. 100
50158 3/4" Step Shank100 1000 .300 .143/130 .5
50159 1" Step Shank 100 1000 .300 .143/130 .6
.300 HEAD DIAMETER DRIVE PINS -MASTER PACK
CAT. STD. STD. HEAD SHANK WT./
NO. SHANK LENGTH BOX CTN. DIA. DIA. 100
50980 1/2" K 1000 5000 .300 .143 .5
53300 5/8" K 1000 5000 .300 .143 .5
51040 3/4" 1000 5000 .300 .143 .5
51100 1" 1000 5000 .300 .143 .6
51160 1-1/4" 1000 5000 .300 .143 .8
51340 1/2"K TH 1000 5000 .300 .143 .5
53400 5/8" K TH 1000 5000 .300 .143 .5
51400 3/4" K TH 1000 5000 .300 .143 .5
51520 1" K TH 1000 5000 .300 .143 .6
.300 HEAD DIAMETER DRIVE PINS WITH 3/4" WASHER
CAT. STD. STD. HEAD SHANK WT./
NO. SHANK LENGTH BOX CTN. DIA. DIA. 100
50070 3/4" 100 1000 .300 .143 1.6
.300 HEAD DIAMETER DRIVE PINS WITH 7/8" WASHER
CAT. STD. STD. HEAD SHANK WT./
NO. SHANK LENGTH BOX CTN. DIA. DIA. 100
50090 1" 100 1000 .300 .143 1.9
50092 1-1/4" 100 1000 .300 .143 2.0
50094 1-1/2" 100 1000 .300 .143 2.1
.
300 HEAD DIAMETER DRIVE PINS WITH 1" WASHER
CAT. STD. STD. HEAD SHANK WT./
NO. SHANK LENGTH BOX CTN. DIA. DIA. 100
50108 1-1/4" 100 1000 .300 .143 2.2
50110 1-1/2" 100 1000 .300 .143 2.3
.300 HEAD DIAMETER DRIVE PINS WITH 1-7/16" INSULATION WASHER
CAT. STD. STD. HEAD SHANK WT./
NO. SHANK LENGTH BOX CTN. DIA. DIA. 100
50122 1-1/2" 100 1000 .300 .143 2.1
1/4"-20 THREADED STUDS
CAT. THREAD SHANK STD. STD. HEAD SHANK WT./
NO. LENGTH LENGTH BOX CTN. DIA. DIA. 100
5
0320 1/2" 1/2"K 100 5000 1/4" .143 .8
50322 3/4" 1/2"K 100 1000 1/4" .143 1.1
50326 3/4" 3/4" 100 1000 1/4" .143 1.2
50328 1/2" 1" 100 1000 1/4" .143 1.2
.300 HEAD DIAMETER PINS WITH CEILING CLIPS
CAT. SHANK STD. STD. HEAD SHANK WIRE WT./
NO. LENGTH BOX CTN. DIA. DIA. HOLE 100
50363 1" 100 1000 .300 .143 0.278" 3.4
50364 1" 100 1000 .300 .143 0.278" 3.5
50368 1" 100 1000 .300 .143 0.278" 3.0
50370 1-1/4" 100 1000 .300 .143 0.278" 3.7
50374 1-1/4" 100 1000 .300 .143 0.278" 3.2
.300 DIAMETER HEAD DRIVE PINS WITH BX CABLE STRAPS AND CONDUIT CLIPS
CAT. STD. STD. HEAD SHANK WT./
NO. DESCRIPTION BOX CTN. DIA. DIA. 100
50150 1" 100 1000 .300 .143 3.5
50152 1-1/4" 100 1000 .300 .143 3.7
50380 1/2" EMT 1-1/4" pin 100 1000 .300 .143 3.4
50381 1/2" EMT 1" pin TH 100 1000 .300 .143 3.3
50382 1/2" EMT 1" pin100 1000 .300 .143 3.3
50384 3/4" EMT 1-1/4"pin 100 1000 .300 .143 3.5
50385 3/4" EMT 1" pin TH 100 500 .300 .143 3.4
50386 3/4" EMT 1" pin100 1000 .300 .143 3.3
50388 1" EMT 1" pin TH 25 250 .300 .143 3.2
.300 HEAD DIAMETER PIN WITH REBAR BASKET CLIP
CAT. STD. STD. HEAD SHANK WT./
NO. DESCRIPTION BOX CTN. DIA. DIA. 100
50702 32mm w/ basket clip 100 100 8mm .143 4.0
50704 37mm w/ basket clip 100 100 8mm .143 4.1
Powder Load
Selection Guide
.22 CALIBER “A”
CAT. POWER LOAD STD. STD. MASTER WT./
NO. LEVEL COLOR SIZE BOX CTN. CTN. 100
50500 1 Gray .22A 100 1000 20000 .33
50502 2 Brown .22A 100 1000 20000 .33
50504 3 Green .22A 100 1000 20000 .33
50506 4 Yellow .22A 100 1000 20000 .33
the minimum fastener shank length required. Do not
select a shank length longer than that required for the
application. An excessively long shank can burnish or
polish the hole created in the steel resulting in a
reduction in load capacity. To determine the minimum
threaded length, add the thickness of the fixture and the
nut / washer thickness. The nut and washer thickness is
equal to the nominal thread diameter.
Do not over tighten threaded studs, the maximum
tightening torque is listed in the table below. Use of a
nut setter is recommended to reduce the possibility of
over tightening the fasteners. For critical applications,
perform a job site test.
K=Knurled TH=Top Hat
6 P7201
MODEL P7201 CAT. NO.52004/Deluxe Kit 52005/Blister Pack