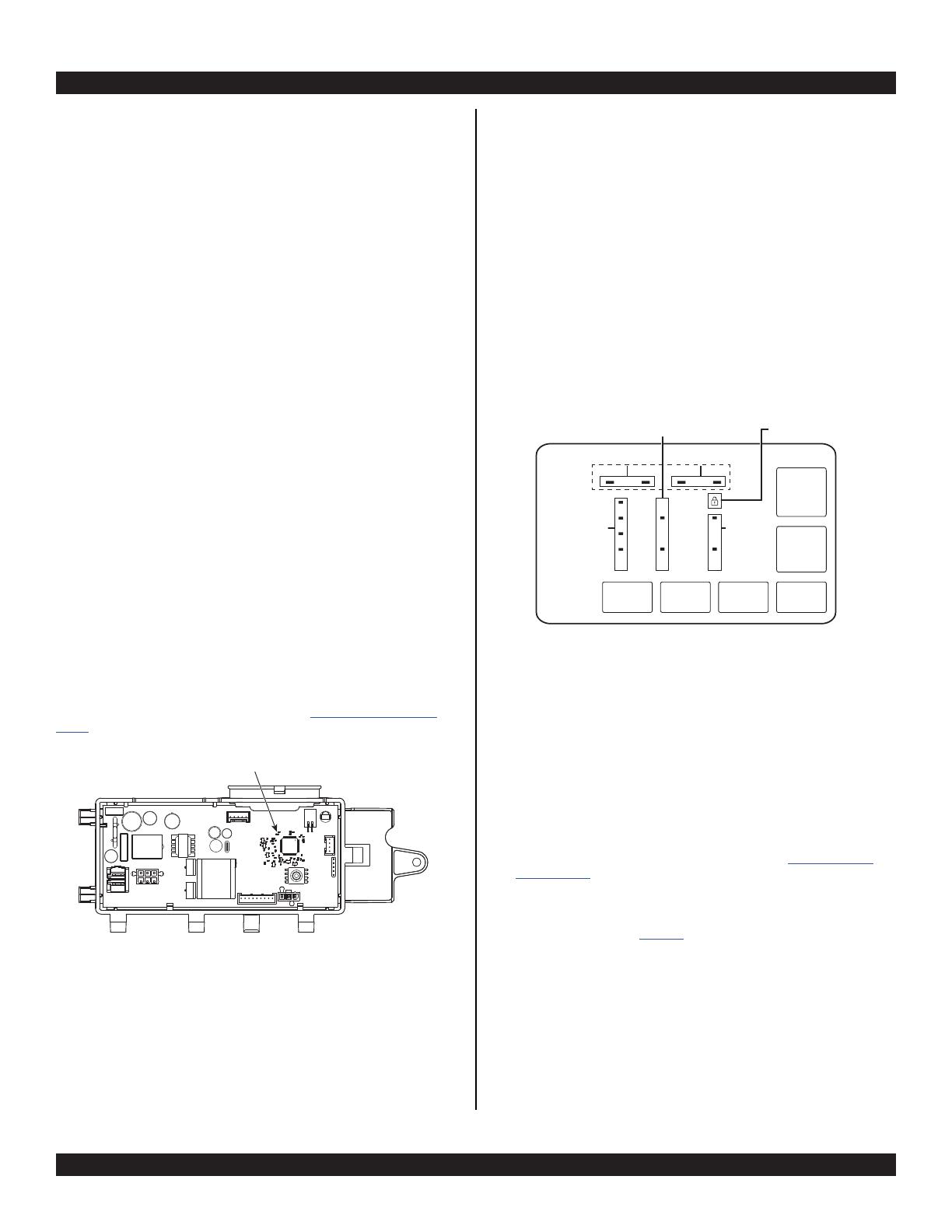
FOR SERVICE TECHNICIAN’S USE ONLY
DO NOT REMOVE OR DESTROY10
SERVICE GUIDE
Before servicing, check the following:
Ƀ
Make sure there is power at the wall outlet.
Ƀ
Has a household fuse blown or circuit breaker tripped? Was a regular
fuse used? Inform customer that a time-delay fuse is required.
Ƀ
Are both hot and cold water faucets open and water supply hoses
unobstructed?
Ƀ
Make sure drain hose is not sealed into drain pipe, and that there is an
air gap for ventilation. Ensure drain height is between 39" (991 mm)
and 8' (2.4 m) above the floor.
Ƀ
All tests/checks should be made with a VOM (volt-ohm-milliammeter)
or DVM (digital-voltmeter) having a sensitivity of 20,000 Ω per VDC or
greater.
Ƀ
Resistance checks must be made with washer unplugged or power
disconnected.
IMPORTANT: Avoid using large diameter probes when checking
harness connectors as the probes may damage the connectors upon
insertion.
Ƀ
Check all harnesses and connections before replacing components.
Look for connectors not fully seated, broken or loose wires and
terminals, or wires not pressed into connectors far enough to engage
metal barbs.
Ƀ
A potential cause of a control not washer functioning is corrosion
or contamination on connections. Use an ohmmeter to check for
continuity across suspected connections.
Ƀ
To properly check voltage:
1. Unplug appliance or disconnect power.
2. Attach voltage measurement probes to proper connectors.
3. Plug in appliance or reconnect power and verify voltage reading.
4. Unplug appliance or disconnect power after completing voltage
measurements.
DIAGNOSTIC LED – MAIN CONTROL (ACU)
A troubleshooting tool has been implemented onto the main control
board—a diagnostic LED.
LED Flashing – The Control is detecting correct incoming line voltage and
the processor is functioning.
LED OFF or ON – Control malfunction. Perform TEST #1: Main Control
(ACU), to verify main control functionality.
Figure 1 - Diagnostic LED
SERVICE MODE
These tests allow factory or service personnel to test and verify all
inputs to the main control board. You may want to do a quick and
overall checkup of the washer with these tests before going to specific
troubleshooting tests.
ACTIVATING SERVICE MODE
1. Be sure the washer is in standby mode (plugged in with all LEDs
off).
2. Follow the steps below within 8 seconds:
dz Press and Release Key 1
dz Press and Release Key 2
dz Press and Release Key 3
dz Repeat this 3 button sequence 2 more times
3. If this test mode has been entered successfully, all indicators on
the HMI will be illuminated for 1 second then will be turned OFF.
After this, If there are no saved fault codes, the STATUS indicators
(Sense, Soak, Wash and Done) will blink two times and then all the
indicators will be turned OFF.
LED group 2
LED group 5
LED group 6
LED
group 1
LED
group 3
LED group 4
Key 6/
POWER
Key 5/
START
Key 4Key 3
Key 2
Key 1
Figure 2: Diagram of the HMI screen and navigational buttons.
Unsuccessful Activation
If entry into Diagnostic mode is unsuccessful, refer to the following
indications and actions:
Indication: None of the LEDs will turn on.
Action: Turn on the appliance by pressing the POWER Button or rotating
the knob and select any cycle.
➢
If LEDs turn on after pressing the POWER Button or turning the
knob, then try to enter Service mode again: repeat step 2 mentioned
in activating sequence and complete it within 8 seconds. If these
re-entry procedures fail to enter into Diagnostic mode, there is likely
a faulty button in the HMI. Replace the HMI.
➢
If no LEDs come on after selecting the cycle, go to TEST #1: Main
Control (ACU).
Activation with Saved Fault Codes
If there is a saved fault code, it will be flashing in the display. Review the
Fault/Error Codes table on page 16 for the recommended procedure. If
there is no saved fault code. All LEDs will turn OFF.
LED
Location
Status
Indicator