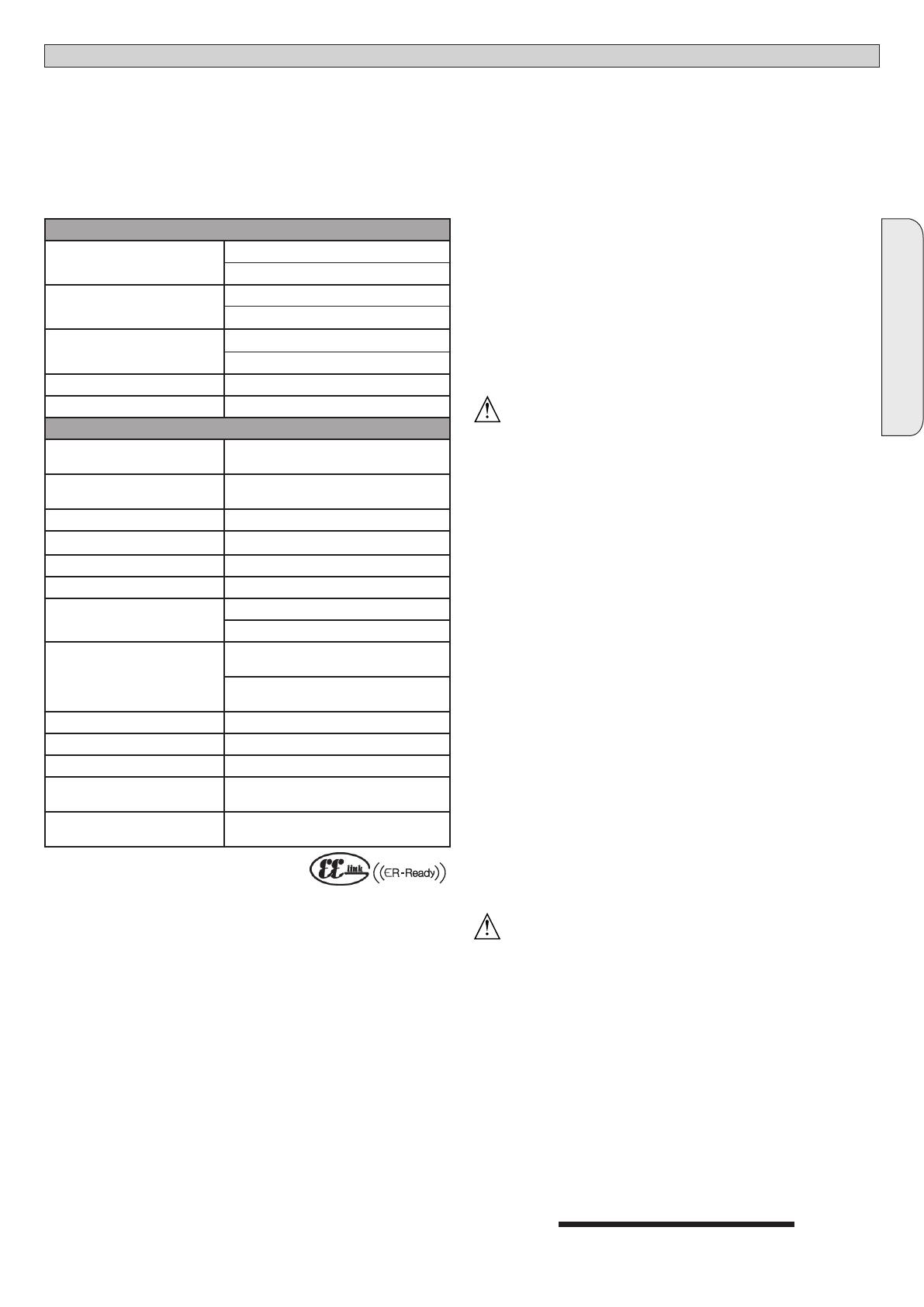
ENGLISH
INSTALLER WARNINGS
Anything that is not explicitly provided for in the installation ma-
nual is not allowed. The operator’s proper operation can only be
guaranteed if the information given is complied with. The Firm shall
not be answerable for damage caused by failure to comply with the
instructions featured herein.
While we will not alter the product’s essential features, the Firm reserves
the right, at any time, to make those changes deemed opportune to
improve the product from a technical, design or commercial point of
view, and will not be required to update this publication accordingly.
WARNING! Important safety instructions. Carefully read and comply with
all the warnings and instructions that come with the product as incorrect
installation can cause injury to people and animals and damage to property.
The warnings and instructions give important information regarding safety,
installation, use and maintenance. Keep hold of instructions so that you can
attach them to the technical le and keep them handy for future reference.
GENERAL SAFETY
This product has been designed and built solely for the purpose indicated herein.
Uses other than those indicated herein might cause damage to the product and
create a hazard.
- The units making up the machine and its installation must meet the requirements
of the following European Directives, where applicable: 2004/108/EC, 2006/95/
EC, 2006/42/EC, 89/106/EC, 99/05/EC and later amendments. For all countries
outside the EEC, it is advisable to comply with the standards mentioned, in ad-
dition to any national standards in force, to achieve a good level of safety.
- The Manufacturer of this product (hereinafter referred to as the “Firm”) disclaims
all responsibility resulting from improper use or any use other than that for
which the product has been designed, as indicated herein, as well as for failure
to apply Good Practice in the construction of entry systems (doors, gates, etc.)
and for deformation that could occur during use.
- Installation must be carried out by qualied personnel (professional installer,
according to EN 12635), in compliance with Good Practice and current code.
- Before installing the product, make all structural changes required to produce
safety gaps and to provide protection from or isolate all crushing, shearing and
dragging hazard areas and danger zones in general in accordance with the
provisions of standards EN 16005 or any local installation standards. Check that
the existing structure meets the necessary strength and stability requirements.
- Before commencing installation, check the product for damage.
- The Firm is not responsible for failure to apply Good Practice in the construction
and maintenance of the doors, gates, etc. to be motorized, or for deformation
that might occur during use.
- Make sure the stated temperature range is compatible with the site in which
the automated system is due to be installed.
- Do not install this product in an explosive atmosphere: the presence of am-
mable fumes or gas constitutes a serious safety hazard.
- Disconnect the electricity supply before performing any work on the system.
Also disconnect buer batteries, if any are connected.
- Before connecting the power supply, make sure the product’s ratings match the
mains ratings and that a suitable residual current circuit breaker and overcurrent
protection device have been installed upline from the electrical system. Have
the automated system’s mains power supply tted with a switch or omnipolar
thermal-magnetic circuit breaker with a contact separation that meets code
requirements.
- Make sure that upline from the mains power supply there is a residual current
circuit breaker that trips at no more than 0.03A as well as any other equipment
required by code.
- Make sure the earth system has been installed correctly: earth all the metal parts
belonging to the entry system (doors, gates, etc.) and all parts of the system
featuring an earth terminal.
- Installation must be carried out using safety devices and controls that meet
standards EN 12978 and EN 16005.
- Impact forces can be reduced by using deformable edges.
- In the event impact forces exceed the values laid down by the relevant standards,
apply electro-sensitive or pressure-sensitive devices.
- Apply all safety devices (photocells, safety edges, etc.) required to keep the
area free of impact, crushing, dragging and shearing hazards. Bear in mind the
standards and directives in force, Good Practice criteria, intended use, the instal-
lation environment, the operating logic of the system and forces generated by
the automated system.
- Apply all signs required by current code to identify hazardous areas (residual
risks). All installations must be visibly identied.
- Once installation is complete, apply a nameplate featuring the door/gate’s data.
- If the automated system is installed at a height of less than 2.5 m or is accessible,
the electrical and mechanical parts must be suitably protected.
- Install any xed controls in a position where they will not cause a hazard, away
from moving parts. More specically, hold-to-run controls must be positioned
within direct sight of the part being controlled and, unless they are key operated,
must be installed at a height of at least 1.5 m and in a place where they cannot
be reached by the public.
- Attach a label near the operating device, in a permanent fashion, with informa-
tion on how to operate the automated system’s manual release.
- Make sure that, during operation, mechanical risks are avoided or relevant
protective measures taken and, more specically, that nothing can be banged,
crushed, caught or cut between the part being operated and surrounding parts.
- Once installation is complete, make sure the motor automation settings are
correct and that the safety and release systems are working properly.
- Only use original spare parts for any maintenance or repair work. The Firm dis-
claims all responsibility for the correct operation and safety of the automated
system if parts from other manufacturers are used.
- Do not make any modications to the automated system’s components unless
explicitly authorized by the Firm.
- Instruct the system’s user on what residual risks may be encountered, on the
control systems that have been applied and on how to open the system manu-
ally in an emergency. give the user guide to the end user.
- Dispose of packaging materials (plastic, cardboard, polystyrene, etc.) in accord-
ance with the provisions of the laws in force. Keep nylon bags and polystyrene
out of reach of children.
WIRING
WARNING! For connection to the mains power supply, use: a multicore cable
with a cross-sectional area of at least 5x1.5mm
2
or 4x1.5mm
2
when dealing
with three-phase power supplies or 3x1.5mm
2
for single-phase supplies (by
way of example, type H05 VV-F cable can be used with a cross-sectional area
of 4x1.5mm
2
). To connect auxiliary equipment, use wires with a cross-sectional
area of at least 0.5 mm
2
.
- Only use pushbuttons with a capacity of 10A-250V or more.
- Wires must be secured with additional fastening near the terminals (for example,
using cable clamps) in order to keep live parts well separated from safety extra
low voltage parts.
- During installation, the power cable must be stripped to allow the earth wire
to be connected to the relevant terminal, while leaving the live wires as short
as possible. The earth wire must be the last to be pulled taut in the event the
cable’s fastening device comes loose.
WARNING! safety extra low voltage wires must be kept physically separate from
low voltage wires.
Only qualied personnel (professional installer) should be allowed to access
live parts.
CHECKING THE AUTOMATED SYSTEM AND MAINTENANCE
Before the automated system is nally put into operation, and during maintenance
work, perform the following checks meticulously:
- Make sure all components are fastened securely.
- Check starting and stopping operations in the case of manual control.
- Check the logic for normal or personalized operation.
- Check that all safety devices are working properly and that the anti-crush safety
device (if tted) is set correctly.
- Impact forces can be reduced by using deformable edges.
- Make sure that the emergency operation works, where this feature is provided.
- Check opening and closing operations with the control devices applied.
- Check that electrical connections and cabling are intact, making extra sure that
insulating sheaths and cable glands are undamaged.
- While performing maintenance, clean the sensors’ optics.
- When the automatic door operator is out of service for any length of time,
activate the emergency release (see “EMERGENCY OPERATION” section) so
that the operated part is made idle, thus allowing the door to be opened and
closed manually.
-
If the power cord is damaged, it must be replaced by the manufacturer or their
technical assistance department or other such qualied person to avoid any risk .
- The maintenance described above must be repeated at least once yearly or at
shorter intervals where site or installation conditions make this necessary.
WARNING!
Remember that the drive is designed to make the gate/door easier to use and
will not solve problems as a result of defective or poorly performed installation
or lack of maintenance
SCRAPPING
Materials must be disposed of in accordance with the regulations in force. There
are no particular hazards or risks involved in scrapping the automated system. For
the purpose of recycling, it is best to separate dismantled parts into like materials
(electrical parts - copper - aluminium - plastic - etc.).
DISMANTLING
If the automated system is being dismantled in order to be reassembled at another
site, you are required to:
- Cut o the power and disconnect the whole electrical system.
- Remove the actuator from the base it is mounted on.
- Remove all the installation’s components.
- See to the replacement of any components that cannot be removed or happen
to be damaged.
THE DECLARATION OF CONFORMITY CAN BE VIEWED ON THIS WEBSITE:
WWW.BFT.IT IN THE PRODUCT SECTION.
AVVERTENZE INSTALLATORE (PORTE) D812061 00200_01
INSTALLATION MANUAL
1) GENERAL OUTLINE
Motorised crosspiece for automatic double sliding doors (mod. VISTA TL 2) or
four-leaf door (mod. VISTA TL 4).
Complete with control panel. Accessories available for producing a complete
installation.
RIGHT-HANDED version (opening to the right, looking at the door from the inside,
Fig. E) and LEFT-HANDED version (opening to the left, looking at the door from
the inside, Fig. F) available for VISTA TL 2 models .
2) TECHNICAL SPECIFICATIONS
MECHANICAL SPECIFICATIONS
Opening width
mod. VISTA TL2: 750 to 3250 mm
mod. VISTA TL4: 1600 to 4400 mm
Door load capacity
mod. VISTA TL2: 120 kg x 2
mod. VISTA TL4: 80 kg x 4
Door size
mod. VISTA TL2: 450 ÷ 1700 mm/door
mod. VISTA TL4: 450 ÷ 1150 mm/door
Protection rating IP X0 (Not for installation outdoors)
Crosspiece dimensions See Fig. C
ELECTRICAL SPECIFICATIONS
Power supply
230V- 220V~ ±10%, 50Hz single-phase
120V~ ±15% 50/60Hz
Power input
Rated: 160W
Maximum: 800 W
Fuses see Fig. P
Accessories power supply 31,5 VDC max 500mA
Power supply V SAFE 24V max 30mA
Alarm output and door status Contact max 24V 0,5A
Opening/closing speed
mod. VISTA TL2: Adjustable up to 1 m/s
mod. VISTA TL4: Adjustable up to 2 m/s
Approach speed
mod. VISTA TL2: in the range 5 to 10 cm/s
in automatic mode
mod. VISTA TL4: in the range 10 to 20cm/s
in automatic mode
Temperature range -20°C (no condensation) + 50°C (inside cover)
Operating cycle Continuous at 25°C
Emergency batteries (optional extras) 2 x 12V 1.2Ah
Radio-receiver built-in Rolling-
Code
Frequency 433.92 MHz
Max. n° of remotes that can be
memorized
63
Usable transmitter versions:
All ROLLING CODE transmitters compatible with
3) PREPARING THE ELECTRICAL SYSTEM
Prepare the electrical system (g. A), referring to the standards in force. Keep
mains power connections well separated from service connections (photocells,
safety edges, control devices, etc.).
Keep mains power connections well separated from safety extra low voltage
connections. Secure the power cable by means of the cable clamp located in
the transformer’s cover. Connect the power cable so that the earth wire (yellow/
green) is longer than the other wires.
4) IDENTIFICATION OF COMPONENTS (Fig. AA)
In the standard composition, the automated VISTA TL system is made up of:
1 Load-bearing header in oxidized aluminium
2 Power supply unit complete with bipolar switch, mains fuse and noise lter
3 Microprocessor-based control unit ARIA - EVO
4 DC gearbox
5 Optical encoder for detecting travel and checking for obstacles
6 Driven pulley
7 Drive belt
8 2 Door runners with 2 wheels on bearings, anti-derailment wheel, height and
depth adjustable
9 Prole for fastening door leaves
10 Rubber travel limit stops
11 Rubber hinge
The following accessories are available to complete installation:
12 BBV Battery-powered panic device
13 ERV Electromagnetic bolt and manual release
14 VISTA SEL Digital function pushbutton unit (optional extra)
15 RIP Infrared radar operating over a narrow angle
16 FPA1 Photocells (1 amplier, 1 transmitter, 1 receiver)
FPA2 Photocells (1 amplier, 2 transmitters, 2 receivers)
17 Cover
18 Brush (code P111618 L=14; code P111618 00001 L=20; code P111618
00002 L=27)
19 code P111660 sealing prole and code P111661 brackets for sealing proles
20 RIP Automatic sliding door safety and opening sensor
21 PRV S20.A18 Floor guide for 20-mm door proles + PRV S20GD.19 TELESCOPIC
Floor guide for 20-mm door proles (Fig. D)
PRV L40 GD.70 Floor guide for 40-mm door proles + PRV L40GD.78 TELESCOPIC
Floor guide for 40-mm door proles (Fig. D)
PPA TL Glass doors calliper (Fig. AD)
22 SBV TL VISTA TL support beam
5) FASTENING METHOD
- Assembling the Cover (Fig. B).
- Cable Passage - drill the side panels to allow cables to pass through.
6) DETERMINING HEADER FASTENING HEIGHT (Fig. D)
The fastening height HFT of the VISTA TL header must be measured where the
oor is at its highest (Fig. D). This is to prevent the possibility of the moving door
leaf getting stuck once installation is nished. Once installed, the height of the
doors can still be adjusted by means of the special adjusters on the runners (Fig. K).
WARNING: The VISTA TL header must be fastened so that it is perfectly
horizontal. This condition must be met to ensure that the automated
system operates properly.
6.1) Fastening to wall (above an opening) (Fig.E-F)
6.2) Mounting between two walls (inside door opening space) (Fig. G)
To position the header symmetrically with respect to the doorway opening, no
matter what kind of installation you are dealing with (above an opening, inside
an opening, etc.), you need to mark both the centre line of the structural opening
and centre line of the VISTA TL header. Fasten the VISTA TL header, lining up the
two marks (Fig. G).
7) POSSIBLE INSTALLATIONS
A number of installation methods for the automated system are listed below:
7.1) Wall mounting (Fig. I-D)
It is best to attach shims in line with the fastening holes already made in the
header. That way, the fastening points will sit on a solid base and you will avoid
the track bending while screws are being fastened. In the event fastening holes
have to be drilled in addition to those already made, drill them approx. every
600-800 mm: this will also depend on what kind of surface you are dealing with
(concrete, brick, wood, iron, etc.).
7.2) Ceiling mounting (Fig. AB)
This type of installation is particularly suitable if the door leaf and xed panel are
made from frameless glass, and hence are not load-bearing.
7.3) Incorporated in door frame (Fig. AC)
The supporting beam is incorporated in a load-bearing door frame or a at
prole is built into the frame that must be thick enough to fasten the VISTA TL
header securely.
8) DOOR ASSEMBLY AND ADJUSTMENT
8.1) Framed doors
For the measurement of door support proles and the doors themselves, see
Fig. AG-AI.
8.2) Glass doors (Fig. AD)
The clamping system PPA can be used only for 10 mm-thick tempered glass
doors or laminated safety glass doors.
It must not be used with double glazing. For the sake of simplicity, reference is
made to glass doors from hereon in.
- No holes must be made in the sheet of glass
-
Clamp PPA must be fastened to the door mounting prole as illustrated in Fig.
AD.
9) DOOR INSTALLATION AND ADJUSTMENT
- Installing the Doors (Fig. J).
- Adjusting the Doors (Fig. K).
10) FLOOR GUIDE AND SLOW DOOR GUIDE (Fig. D)
- Framed doors (Fig. D)
- Glass doors (Fig. AD)
See the relevant instruction manual for their assembly.
11) ADJUSTING TRAVEL LIMIT STOPS (Fig. L)
If the positions of the RH and LH travel limit stops (parts. 10 Fig. AA) need to be ne-
tuned, carefully check the travel and alignment of the runners carrying the doors.
It is important to remember that the position of the travel limit stops also deter-
mine the control board’s self-learning.
----------------------------------------------------------
D812041 00100_01
VISTA TL (ARIA-EVO) - 21