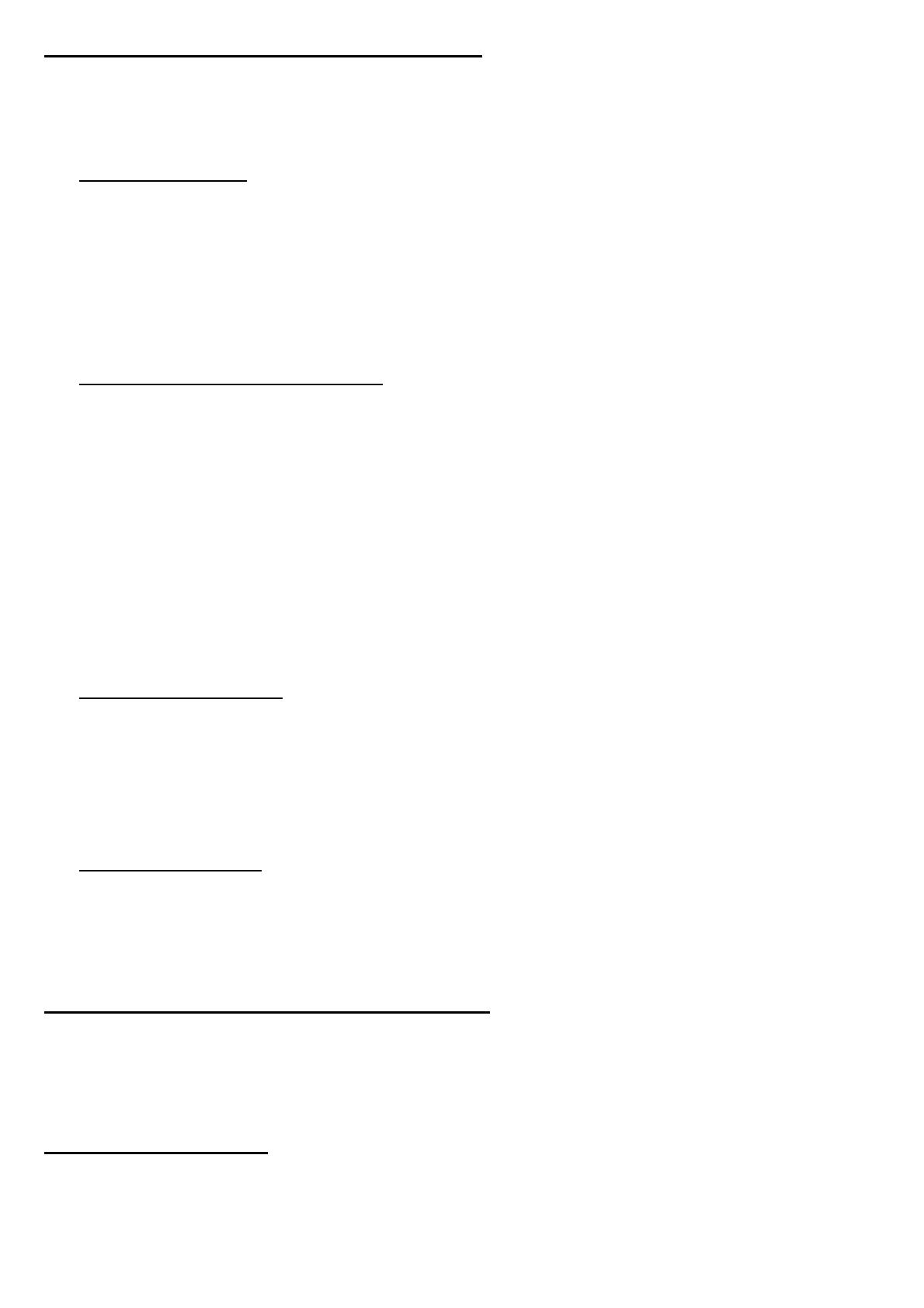
- 8 -
2. DISPONIBILITÉ DU FILETAGE RIGIDE
À partir de cette version il est possible d'effectuer des filetages typiques (avec compensateur) "P630(3)=0" ou des filetages rigides
"P630(3)=1".
Pour effectuer des filetages rigides, la CNC doit contrôler la broche, en vérifiant à chaque moment sa vitesse de rotation et en fournissant
à l'armoire électrique le signal nécessaire pour que la broche tourne à la vitesse sélectionnée.
Considérations générales:
Le filetage rigide consiste en une interpolation entre la broche et l'axe Z.
Il est recommandé que les temps d'accélération/décélération de la broche et de l'axe Z soient égaux.
Les erreurs de poursuite de la broche et de l'axe Z doivent être proportionnelles. Par exemple, si le filetage est fait à F1000 mm/
min., S1000 t/mn (pas de filetage = 1 mm) et on obtient comme erreur poursuite Z=1 mm (observés) et S=360 degrés, on peut
dire que les deux axes sont parfaitement synchronisés.
Dans le but d'ajuster la réponse de la broche, accélération et décélération, dans chacune des gammes, on dispose d'un paramètre
d'accélération/décélération pour chaque gamme de broche.
Comme le gain de l'axe Z est différent pendant l'usinage et pendant le filetage rigide, la CNC dispose de 2 paramètres, un pour
chaque cas.
La sortie FILETAGE_ON (I97) est active chaque fois qu'un filetage rigide est effectué.
Paramètres machine en rapport avec la broche:
P800 Numéro d'impulsions du codeur de broche (0...9999)
P601(7) Signe de la sortie S analogique associée à M19 (0 ou 1)
P609(2) Sens de comptage de la broche (0 ou 1)
P612(8) Type d'impulsion de référence machine dans la broche (0 =Négatif, 1= Positif)
P719 Signal analogique minimum de la broche (0...255)
P719=0 ==> 2,5 mV P719=10 ==>25.0 mV (10 x 2.5)
P719=1 ==> 2,5 mV P719=255 ==>637.5 mV (255 x 2.5)
P717 Fenêtre d'arrêt de la broche. Numéro d'impulsions de comptage (0...255)
La CNC applique internement aux signaux de mesure du codeur un facteur de multiplication x4.
Ainsi, avec un codeur de 1000 impulsions par tour et P717= 100, la fenêtre d'arrêt sera: (360°/4000)x100= ±9°
P718 Gain proportionnel K de la broche (0...255)
Fixe le signal correspondant à 1 impulsion de comptage d'erreur de poursuite du codeur de la broche.
Signal (mV.) = P718 x Erreur de Poursuite (impulsions) x 2,5 mV / 64
P751, P747, P748, P749 Durée rampe d'accélération/décélération de la broche en gamme 1,2,3,4 (0...255) Valeur 1=20 ms
P746 Gain feed-forward de la broche en filetage rigide (0...255)
P750 Gain proportionnel K1 de l'axe Z pendant le filetage rigide (0...255)
P625(1) Le début du filet se trouve synchronisé avec Io de la broche (0=Non, 1=Oui)
Entrées des systèmes de mesure:
P630(4) = 0 Le connecteur A5 s'utilise pour la mesure de la broche et pour la mesure du volant associé à l'axe Z
Les deux mesures doivent être commutées extérieurement.
P630(4) = 1 Le connecteur A5 s'utilise seulement pour la mesure de la broche.
Le connecteur A6 s'utilise pour la mesure du volant associé à l'axe X.
Le connecteur A4 s'utilise pour la mesure du volant ou volants associés aux axes Y, Z.
La sortie O46 du PLC indique l'axe que se déplace en tournant le volant branché au A4.
Si O46=0 se déplace Y et si O46=1 se déplace Z.
Programmation en code ISO
Se programme à l'aide de la fonction G33 (filetage) en devant indiquer l'avance de l'axe et la vitesse de la broche.
Exemples: G33 Z -10 F1000 S1000 M3 F1000 S1000 M3
G33 Z-10
Les fonctions G00, G01, G02 et G03 annulent la fonction G33.
3. VERSION DE SOFTWARE DANS LA CNC
À partir de cette version, quand on accède à l'écran qu'affiche le cheksum de chacune des Eproms,
[Modes Auxiliaires] [Modes Spéciaux] [8]
La CNC affichera, le cheksum de chacune des Eprom et la Version de Software dont dispose la CNC. Par exemple: Version 3.1
4. PROTÈGE-ÉCRAN
Quand on personnalise le paramètre machine “P626(7)=1” La fonction protège-écran agit de la façon suivante:
Après chaque période de 5 minutes sans qu'aucune touche ne soit tapée, ou bien si la CNC n'a rien à actualiser sur l'écran, le signal
vidéo est éliminé et l'écran s'éteint. En tapant sur n'importe quelle touche le vidéo réapparaît.